Sodick IoT
of Industrial Machine
Real time visualization of
moulding sites!
Sodick's IT/IoT*1 applications contribute to smartification of moulding sites.
- Traceability
Enables confirmation and tracking of the production history of moulded products, which improves quality stability. - Preventive maintenance
Realization of maintenance activities by finding failures / signs of defects of injection moulding machines, moulds, and incidental equipment - Productivity improvement
Improvement in operation efficiency by objectively understanding the conditions that do not contribute to production, such as suspension and setup
- IT(= Information Technology), IoT( = Internet of Things)
- MES (Manufacturing Execution System), IF (Interface)
Quality & Production Total Management System
V Connect Optional product
Central Management of Overall Moulding System Data on Moulding Sites
This is the main application of the IT/IoT system for Sodick's injection moulding machines.
Various moulding data can be acquired by connecting the "V Connect" file server and several injection moulding machines online, which can be confirmed on the client's PC.
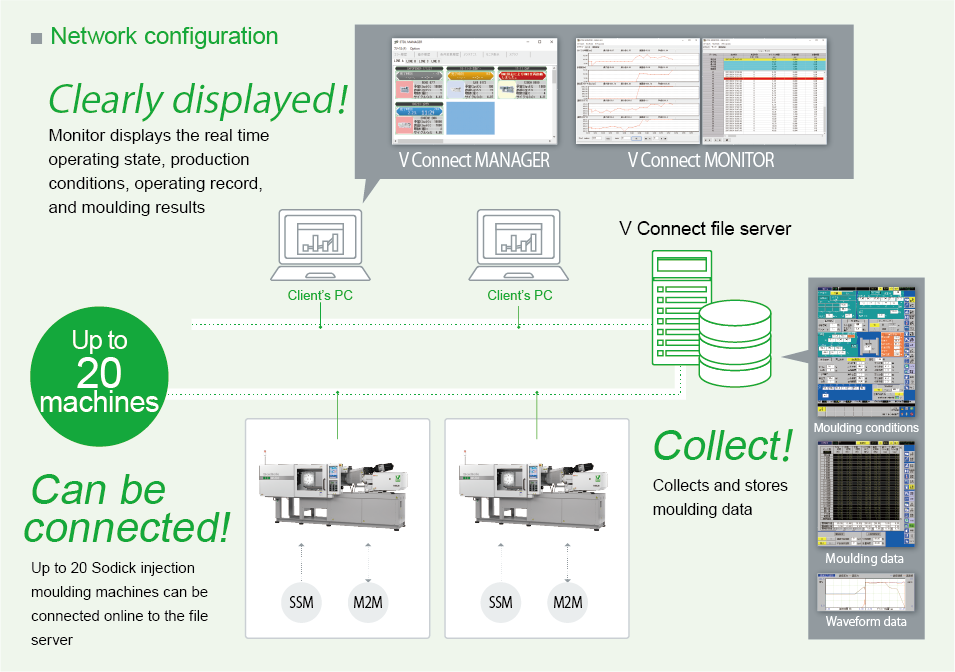
Data to be Collected and Stored
Moulding conditions
Each set value of the moulding machine operation
Waveform data
Shot axis waveform of speed and pressure, and time axis waveform
Log data
Various logs including errors, operation and changes of conditions
Process monitoring
Actual moulding data for process monitoring item
V Connect Recommended Operating Environment
* Please contact a sales representative for details on the recommended environment.
OS | Windows 10 Professional、Windows Server 2016 |
---|---|
CPU | Core i5 (2.0 GHz) or later |
RAM | 8GB or more |
VGA | 1024x768 pixels or more display area |
HDD | 500GB or more |
Communication port | LAN (1000 BASE-T supported) |
Power supply for moulding machines | IM4、IMC7、IMC6、TRD6 |
Max No. of moulding machines for control | 20 |
Shot data 1,000 shots | about 510 KB |
Waveform file | about 100 KB |
Conditions file | about 40 KB |
Log data 1,000 | about 100 KB |
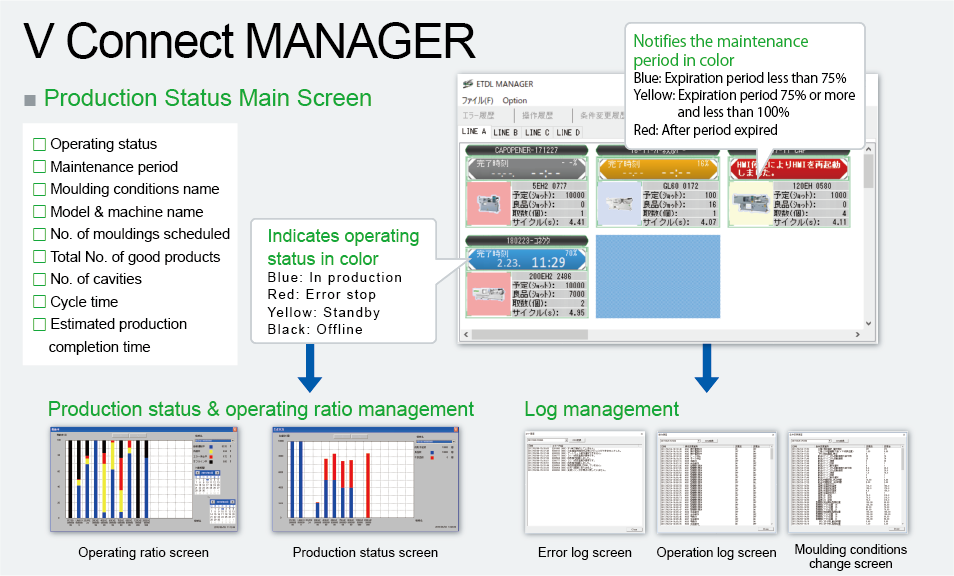
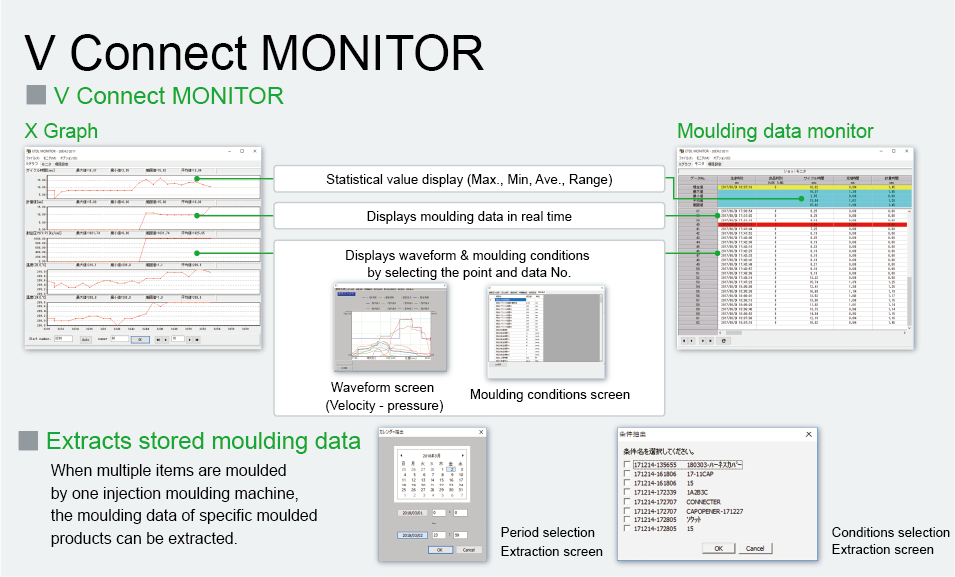
Even Easier to use New Functions
CC unit supported
Registering the plunger diameter of each moulding machine displays the X Graph, Monitor, injection position of the waveform screen and injection speed data in the CC unit.Date/time specified data extraction (Narrowed down)
Setting the start and end date and time displays the shot data of the period on the monitor and X Graph.(Maximum of 50,000 data)Type specified data extraction (Narrowed down)
This is a type narrowing down function used when a large amount of shot data is acquired by the "Date/time specified data extraction" function. Selecting the type (moulding conditions) from the list enables extraction of any shot data.Linking function between each history content and product type
Links each log (error, operation, conditions change and maintenance) and type or moulding conditions of the moulding machine for display.
Data Management Tool for Resin in Mould
SSM Sodick Scientific Moulding Optional product
Visualize the data of the resin in the mould
for full utilization to further improve productivity!
The injection pressure and resin pressure in the mould by the V-LINE® without backflow of the injected resin has excellent correlation, which enables double-checking of the moulded product quality. Actively proposes numericalization of the behavior of the resin in the mould to be used for various applications.
Setting of optimal moulding conditions
Automatic sorting of defective products
Quality control
Mould evaluation
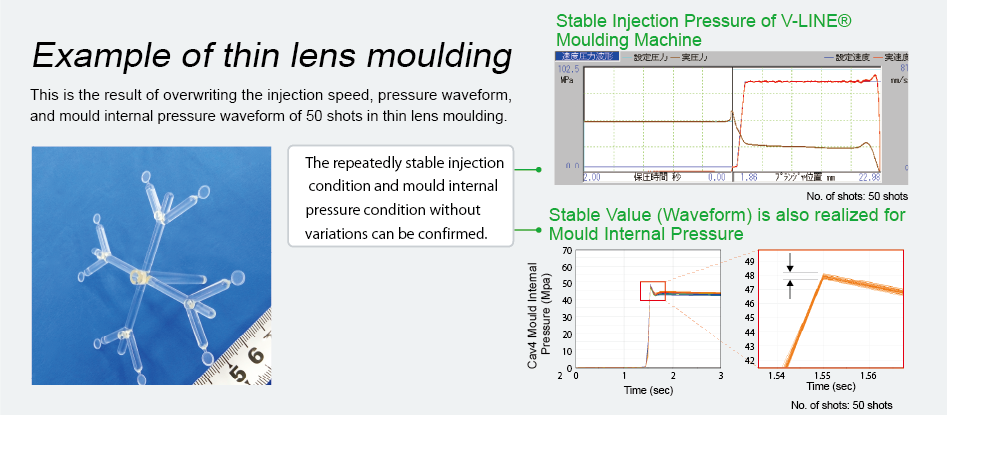
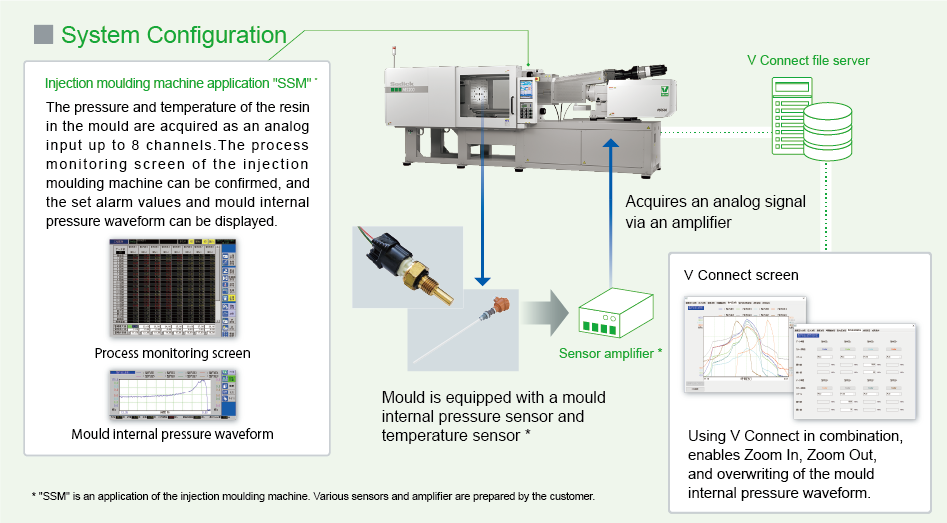
Machine to Machine Communication Function
M2M Machine to Machine Optional product
Constructed a traceability system by
integrating various data of the moulding system!
Sodick's injection moulding machine provides a function to perform mutual communication with peripheral equipment (devices) which constitutes the moulding system, such as the sprue picker and dryer.
The traceability system can be constructed by performing centralized and integrated management of the operating data of the moulding machine and peripheral equipment in the operation screen of the injection moulding machine.
ON/OFF operation of peripheral equipment
Various settings
Monitoring of operating status
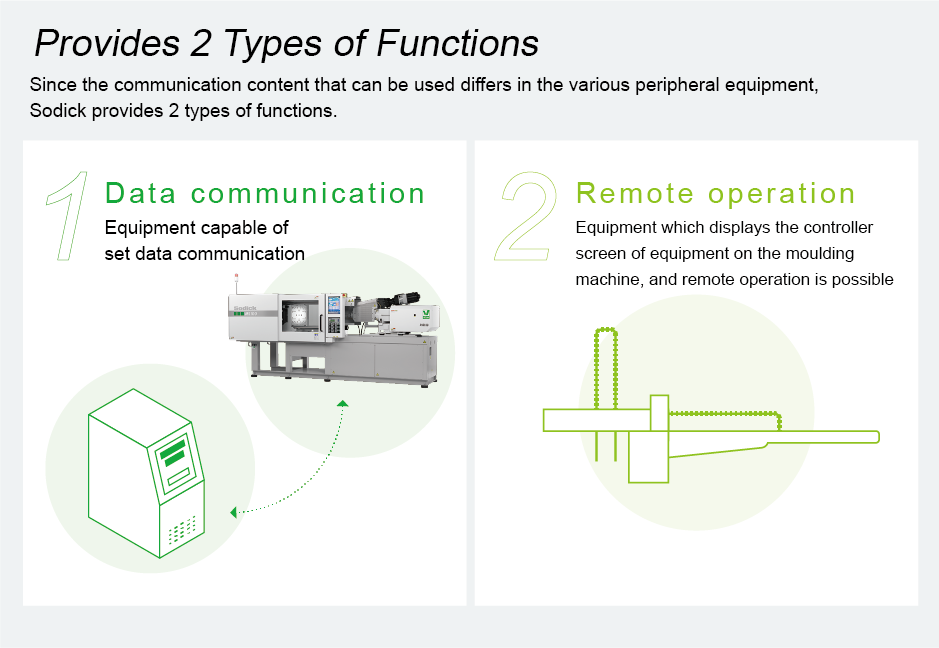
1. Data Communication | 2. Remote Operation | |
---|---|---|
Typical equipment | Mould temperature controller, material dryer | Traverse robot, hot runners |
Connection | Connected via serial cable Direct connection: 1 unit Equipment with relay function can communicate with up to 2 units |
Communication via LAN cable Connection is possible with several equipment via a HUB relay |
Communication port | RS-422/485 (Additional construction of terminal block is required) |
LAN (Setting of device name of moulding machine, and IP address) |
Equipment side data | Acquired by injection moulding machine | Display only, acquisition not possible |
Advantage | Injection moulding machine side performs integrated management of the equipment conditions |
If the equipment is supported, individual management is not required |