スマートフォンやPC、家庭用ゲーム機など身近な電子機器に欠かせないコネクタ。
京都府宇治市に工場を構えるトップは、そのコネクタ向け精密金型の設計・製作から量産までを手がけている。
材料特性を考慮した金型設計やμm単位での金型加工、不良品を見逃さない自動全数検査体制などが強み。
中でも成形には長年培った独自のノウハウがあり、ソディック製の射出成形機「LP20EH3」を駆使して微細コネクタの安定量産を実現している。
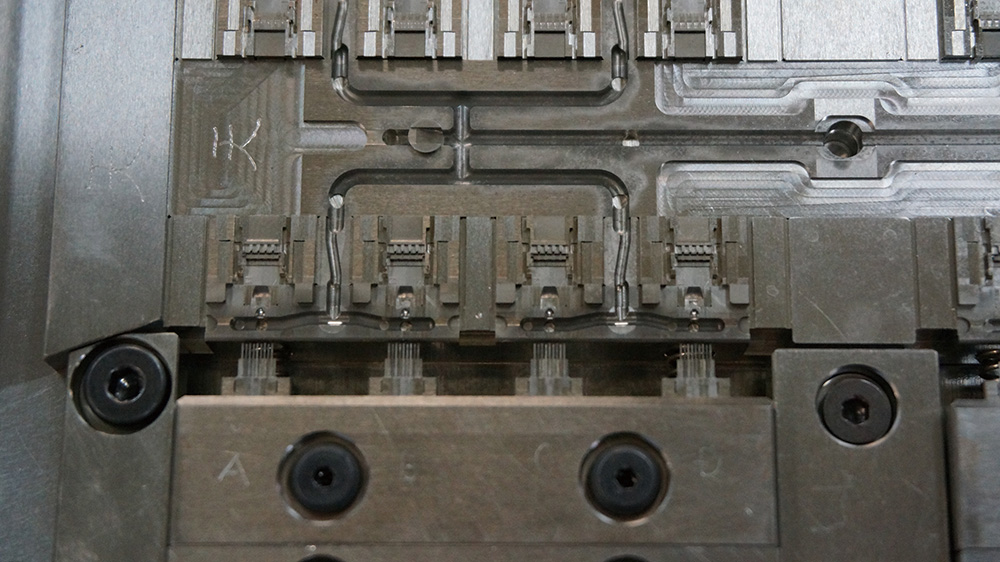
μm単位の金型加工技術と
独自の成形ノウハウで
コネクタの超微細化ニーズに応える
ソディックの成形機でバリ削減とハイサイクルを両立
同社の主要製品であるコネクタ
スマートフォンやPC、家庭用ゲーム機など身近な電子機器に欠かせないコネクタ。
京都府宇治市に工場を構えるトップは、そのコネクタ向け精密金型の設計・製作から量産までを手がけている。
材料特性を考慮した金型設計やμm単位での金型加工、不良品を見逃さない自動全数検査体制などが強み。
中でも成形には長年培った独自のノウハウがあり、ソディック製の射出成形機「LP20EH3」を駆使して微細コネクタの安定量産を実現している。
1988年、研削加工の技術者として働いていた月野年英社長が独立して同社を立ち上げた。当初は研削盤での部品加工のみを手がけていたが、顧客から「金型にも目を向けてみてはどうか」と促され、放電加工やフライス加工、組付けなどの技術をもつスタッフを集めて金型製作の体制を構築。1996年に精密金型の受注を開始した。それから7年後の2003年には、子会社のKTPに射出成形機を導入して成形事業もスタート。2012年に成形事業を吸収し、現在は社内で金型設計・製作から量産まで一貫して行っている。
現在の同社の主力製品は、長さ数mmから数cmの微細コネクタ。スマートフォン向けが多いが、PC・家庭用ゲーム機やAIサービス向けクラウドプラットフォームに使われるものもある。成形する素材はLCP(液晶ポリマー)やPPS(ポリフェニレンサルファイド)がメイン。8個取りや16個取りの金型を使い、1種類の製品を平均で月産200万個、多いもので月産1,000万個生産している。また、比較的大きな製品として、工作機械のジョイント部品も製造している。
コネクタを安定的に量産するための金型づくりに欠かせないのが、同社の祖業でもある研削加工技術である。コネクタには端子の入る微細な溝があり、雌型に雄型のピン(突起)を突き当ててできる隙間に樹脂を充填してこの溝を成形している。溝の数(「極数」と呼ぶ)はコネクタの種類ごとに異なり、例えばあるシリーズのコネクタでは9~61まで極数のバリエーションがある。極数が9であれば9本のピンを、61であれば61本のピンを重ね合わせて金型に組み込む。このピンを研削盤でいかに精度良く削り出せるかが、金型の出来を大きく左右する。
しかも、「公差1μmと図面に書かれているからといって、ピン1本当たり1μmの誤差が許されるわけではありません」と月野社長は話す。1μmの誤差でも20本重ねれば20μmになり、マイナスの誤差であれば金型に隙間ができてバリが発生する。
「10本、20本と重ねたときの誤差を1μmや2μmにおさめるのが難しく、ピン1本ずつの誤差はゼロに等しい。それを実現するための研削加工精度が、金型づくりのカギを握ります」(月野社長)。
同社はニッコー製の平面研削盤「F-515HD Ⅱ」を10台保有し、6人のベテラン技術者がμm単位の加工を担当している。また、研削加工の後に行う放電加工の精度も重視しており、ソディック製の超精密形彫り放電加工機「AP1L」、ワイヤ放電加工機「AQ325L」など放電加工機はソディック製で揃えている。
加工技術に加え、精密成形に対応した成形設備も強みだ。射出成形機の導入にあたっては精度面を重視する。コネクタ1個の重さはわずか数mgであり、わずかな量の材料を安定して計量するための制御技術が必須となる。また、金型の破損を防止するために型締めの直進精度も重要となる。同社はこうした観点から、ソディック製の「LP20EH3」(以下、EH3)をはじめとする型締め力18~50tの射出成形機33台を保有。LCPの成形にはソディック製を、PPSには他社製をというように素材と成形機との相性を考慮して使い分けている。
高精度な成形機があっても、それを使いこなすノウハウがなければコネクタの安定量産はできない。成形する材料により、充填速度や金型温度、サイクルタイムなどを細かく調整している。例えば、PA46(ポリアミド46)のように成形機内での長時間の滞留により変性しやすい材料では、サイクルタイムを短く設定。短いサイクルタイムに対応できる成形品の取出し機も社内で設計・開発する徹底ぶりだ。
また、コネクタ製造に不可欠な品質管理にも自社開発の装置を活用している。市販のパーツフィーダやカメラ、画像検査システムに、自前の搬送装置を組み合わせた画像検査装置を製作し、全数検査を自動化して、目視による検査のばらつきやミスを撲滅した。当初はコネクタの種類ごとに専用機をつくっていたが、現在は種類の異なるコネクタにも対応できる汎用機の開発を進めている。
「不良品が流出すれば顧客だけでなくエンドユーザーにも迷惑がかかります。画像検査装置による全数検査は、品質保持のために必須だと考えています」(月野社長)。
同社が追求するコネクタの安定量産に欠かせないのがソディック製の射出成形機だ。最初の1台を導入したのは10年ほど前で、それから徐々に台数を増やしてきた。現在、33台の射出成形機のうち最も多い10台をEH3が占めている。
ソディック製を導入する前に使っていた射出成形機は、型開閉の速度が速い「トグル式」でサイクルタイムの短縮には有利だったものの、成形時のバリが課題だった。樹脂の中でもLCPは溶融時の粘度が低く、バリが出やすい。そこで、ソディックの営業担当者から提案を受け、金型の広い面積を均一な圧力で締めつけられる「直圧式」の「LD20EH2」(EH3の前身)を導入。結果、バリは改善し、型ずれのトラブルも削減できた。また、可塑化と射出の工程を分離するソディック独自の「V-LINE®」による樹脂の正確な可塑化・計量・充填能力は、トップが求める射出成形機の要素にしっかりと合致していた。
一方、今度はサイクルタイムが問題になった。同社のように小物部品を大量生産する現場では、1秒の違いが製造コストに大きく影響する。トグル式のスピードに慣れた目には、直圧式の “一呼吸置くような動作” がかなり気になったという。
この問題を解決したのが2015年に導入したEH3だった。成形製造部を統括する前田広志部長は、「EH3はお世辞ではなくすごい機械。サイクルタイムはトグル式の射出成形機とほぼ同等で、繰り返し精度も非常に高く、トグルで起きていたピンが折れるトラブルはまったくなくなりました」と評価する。LD20EH2ではサイクルタイムが速くて8秒、これをEH3では3.5秒にまで短縮し、大幅な生産性アップを実現した。同社では、工場を見学に来た顧客にEH3の導入を勧めるほど、同機に信頼を置いている。
電子機器の小型化・高機能化が進む中、基板に組み込まれるコネクタはより小さなサイズが必要となる。そのため、同社では溝のピッチが0.2mmと、従来の0.25mmよりもさらに狭ピッチのコネクタに挑戦している。月野社長は、「ピッチが狭くなることで、小型になり機能も高まりますが、金型加工や成形はより難易度が増します」と話す。
コネクタの高機能化に伴い、「人の感覚に頼らない成形」(月野社長)をどう構築していくかが今後の課題だ。「実はコネクタの成形では、立上げ時の条件設定や量産中のロット検査など、人の感覚に頼っている部分がまだ多いのです」と月野社長。成形条件の設定は前田部長をはじめとするベテランの知見が頼り。また、成形機からロギングデータを取得し、成形品質の変動を感知して不良が出た場合は成形機を止める仕組みをすでに構築しているが、微細なコネクタの場合は捉えきれない不良もあるため4時間ごとのロット検査が不可欠となっている。AIや各種センサを使い、成形機内でこれらを完結できれば大幅な省力化につながる。
前田部長は、金型監視装置のモニタ画像を成形機の操作画面で確認できるようにしたいと考えている。金型の破損を防ぐために成形機に監視装置を取り付けているが、モニタ画像の確認画面と成形機の操作画面が別々にあるため、オペレーターがあちこち見なければならず使い勝手が悪い。素早い操作が求められる立上げ時の事故を防ぐためにも、監視装置と成形機との連携が必要だという。
今後は狭ピッチコネクタをはじめとする既存顧客のニーズに応えるとともに、微細コネクタ製造で培った技術を活かした新規顧客の開拓にも力を入れる。月野社長が「精度を要する医療機器分野などの需要を掘り起こしていきたい」と語るように、部品加工から金型製作、コネクタの量産へと事業の幅を広げてきた同社は、すでに次のステップを見据えている。