国内でのモノづくりにこだわり
シンプルかつ存在感のある眼鏡フレームを提案
~ソディック製の工作機械や成形機を積極的に導入し、メーカとして成長を図る~
田中 聖太郎 代表取締役
タナカフォーサイトは、パッド(鼻あて)やパッドアームなど鼻回りの眼鏡部品を中心に、眼鏡フレーム全体の製造までを手がける福井県鯖江市の眼鏡メーカだ。数千円の海外製フレームが多く出回る中、国内でのモノづくりにこだわり、シンプルでありながらユーザの心をつかむ付加価値の高いフレームを次々と提案。年代や生活スタイル別のラインアップを拡充し、直販も行うことで市場での認知度を高めつつある。
同社の得意とするのが、デザイン性の高いチタン製フレームや生分解性プラスチックを使った肌に優しいパッド。それらの製造では、ソディックの工作機械や成形機が重要な役割を果たしているという。製造の自動化や効率化にも力を入れており、新規設備の導入によりさらなる成長を図っている。
眼鏡メーカ、部品メーカが集積する福井県鯖江市
福井県鯖江市は日本を代表する眼鏡フレームの生産地であり、数多くの眼鏡メーカや部品メーカが集積している。1900年代初頭に冬の農閑期にも収入を得られる手段として福井県足羽郡麻生津村字生野(現・福井市生野町)で眼鏡づくりが始まり、やがて鯖江市にも広がっていった。現在、日本製眼鏡フレームの9割が福井県でつくられている。
同社の創業は1945年。田中聖太郎社長の祖父が眼鏡部品の販売会社をスタートし、当時福井県で増えつつあった眼鏡工場に部品を供給するようになった。1958年には田中社長の祖母が田中喜代商店の名義で部品製造も手がけるようになる。「眼鏡はもともとイタリアで誕生し、日本では東京や大阪で眼鏡製造が盛んになった後、福井に広がりました。祖父母は大阪から鯖江に出てきたので、資本となる田畑もなく、大掛かりな製造設備を入れるのは難しかった。そこで最初はハンドプレスのような小さな機械を使って部品をコツコツとつくっていたのです」(田中社長)。
眼鏡のフロント(正面部分)とテンプル(つる)をつなぐ開閉部の「飾り鋲」といった小さな部品の製造から始め、徐々にパッドやブリッジ(左右のレンズをつなぐ鼻にかかる部分)などに広げていった。
眼鏡部品製造で60年以上の歴史をもつ同社だが、実は代々続いた会社ではない。祖母から父、そして田中社長と代替わりするたびに、別会社を設立して元の会社を買い取り、新たな事業形態を探るということを繰り返してきた。父親が1972年に設立した田中製作所では、素材メーカと提携してシリコーンパッドの製造を始めたほか、イタリアのミラノやフランスのパリで開催される眼鏡の国際見本市に積極的に参加して海外市場の掘り起こしを図った。
「私も父から『大きな借金をして会社を買いとれ。後は好きに仕事をすればいい』と言われて、そのとおりにやってきました。自ら会社を立ち上げることで、“創業者としての熱意”をもち続けることができたと考えています」(田中社長)。
父親の立ち上げた田中製作所で2000年から社長を務め、2005年に不動産管理および持ち株会社としてタナカフォーサイトを設立。2007年に田中製作所の全業務を引き継いだ。田中製作所は部品メーカとして確固とした地位を築いていたが、経営のトップである田中社長の頭にあったのは、「最終製品までを手がけるフレームメーカになりたい」という思いだった。
「180もの工程を経る眼鏡づくりは分業が基本で、部品メーカと、その部品メーカから部品を集めて最終製品にするフレームメーカとの役割がはっきりわかれています。フレームメーカへの転身を図る部品メーカは失敗する、というジンクスまである。若かったこともあって、どのタイミングで業態転換を図るか、当時はいろいろと悩みました」と田中社長は振り返る。
転機は数年前に訪れた。ミラノで開かれた国際見本市に十数年ぶりに出展し、新しいコンセプトのフレームを発表したところ、欧州のフレームメーカから注文が殺到したのだ。発表したのはチタン製フレーム。1枚の板をプレス成形したいわゆる「一体型」で、溶接部がなくシャープで洗練された印象が特徴だった。また、構成部品はすべてねじで固定する方式のため、購入したフレームメーカが好きな部品と組み合わせることもできた。
「当時、世界の眼鏡生産は中国への依存が高まり、欧州のフレームメーカでは部品の組立てやめっき、表面処理などに必要な技術や設備が失われていました。そうした中で、ねじ止めだけで完成するデザイン性の高いフレームを提供すれば、各社が好きな部品を組み合わせてオリジナルの眼鏡をつくれると考えたのです」(田中社長)。
狙いどおり、同社のチタン製フレームの一部を買い取り、バッファロー・ボーン(水牛の角)の部品と組み合わせるなどして、各社がオリジナルブランドを展開し始めた。
提案したコンセプトが受け入れられたことで「フレームメーカまでもう一息」と考えた田中社長は、生産体制を強化するべく、それまで保有していなかった放電加工機やマシニングセンタ(MC)、プレス機を次々導入。デザイン会社の経営統合も進め、フレームの企画からデザイン、金型設計・製作、プレス加工、溶接、組立てまでを手がける現在の体制を一気につくり上げた。大手フレームメーカといえども部品の組立てが主で金型製作や部品成形は他社に頼むことが多い中で、多額の設備投資に踏み切った背景には、「もう一度、日本でモノづくりに向き合いたい」(田中社長)という強い思いがあった。
この転換期において、田中社長が「大きな出来事だった」と語るのがソディックとの出会いである。
溶接のないチタン一体成形の眼鏡
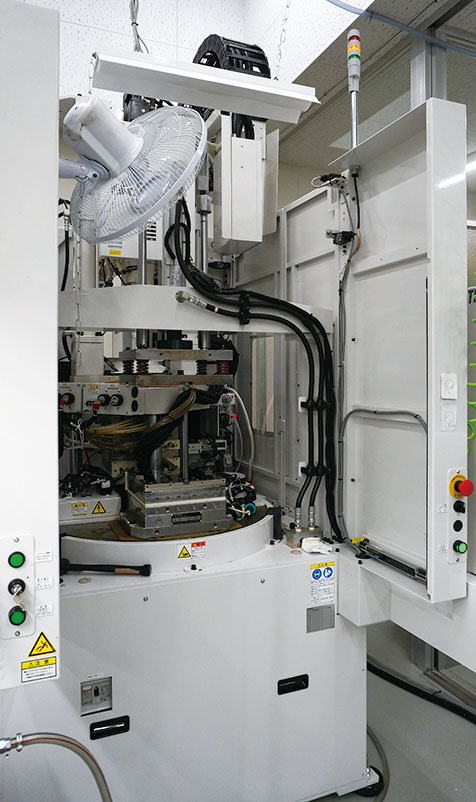
ソディック製成形機に切り替え、
材料ロスを85%削減
同社がソディック製品を初めて購入したのは2017年。田中製作所時代から手がけるパッドを成形するための単動式の竪型射出成形機「TR40EHV」とロータリ式の竪型射出成形機「TR20VRE」が最初だった。それまで使っていた成形機は古いこともあって成形が安定せず、季節によっては不良率が2割にのぼることもあった。困った田中社長が以前勤めていたプラスチック金型メーカに助言を求めたところ、「地元にいいメーカがあるじゃないか」と福井県坂井市に事業所を置くソディックを教えられたのだという。
ソディック製成形機への切替え効果は劇的だった。両機はいずれもソディック独自の可塑化射出装置「V-LINE®」を搭載しており、可塑化と射出を分業化することで安定した成形を実現する。これにより不良率はほぼゼロになった。さらに、材料ロスを85%削減し、年間で数千万円のコストを抑えることができた。
材料ロスの削減には、射出成形金型に関するソディックの知見も活かされた。現在タナカフォーサイトでは、金属のインサート部品にTR40EHVを使って熱可塑性のナイロン樹脂を被覆し、さらにその上からTR20VREを使って熱硬化性のシリコーンを被覆している。以前はシリコーンの成形にホットランナー金型を使っていたが、ソディックのサポートでコールドランナーを導入し、破棄するランナーをなくすことで材料ロスを大幅に削減した。また、1回の成形での取り数も増やし、生産効率を高めることにも成功した。
射出成形機での成功体験から、放電加工機やMCの導入を考えたとき、田中社長は自然とソディックに話をもちかけていた。
「こういうものをつくりたい」という田中社長の要望に応えるべく、ソディックは工具や周辺機器など他社の製品を含めた生産システム全体を提案。
「何から何までサポートしてもらったおかげで、早期にある程度の生産を立ち上げることができました」(田中社長)。
うわさを聞きつけて、「ソディックに生産システムを丸ごと用意してもらえば、フレームをつくれるようになるらしい」と同社に見学に来る企業もあったという。
現在、同社の展開するフレームは、「Facefonts(フェイスフォント)」、「Points&Lines(ポイントアンドライン)」、「OTO(オト)」、「tsubura(ツブラ)」の4ブランド。女性向けブランドのOTOは、類似品が出回るほどの人気で、金沢の水引細工を目元やテンプルにあしらったコラボ商品も好評を博している。ブランドとして最も新しいtsuburaは、トウモロコシ由来100%の生分解性プラスチックを成形したパッドを採用。トウモロコシの抗菌作用による肌への優しさが特徴だ。
同社のフレームは、どのブランドもごくシンプルなデザインを基本としている。一方、価格帯はOTOで5万円弱(フレームのみ)と決して安くはない。安価なフレームが市場に出回る中、顧客にこの価格を納得してもらうために田中社長が目標としているのが、「宝石をつけたり、金めっきを施したりすることで付加価値を上げるのではなく、シンプルでも『素敵だな』と手に取ってもらえるフレーム」だという。
シンプルかつ存在感のあるフレームを実現するには「マシンの性能や精度が不可欠」(田中社長)であり、ここでもソディックの工作機械が活躍している。例えば、OTOはチタン製のフレームをプレス成形した後、高速MC「UH430L」(最大主軸回転速度60,000min-1)や「TT1-400A」(同40,000min-1)で細かな形状やレンズをはめる溝を削り出している。
高速MC「UH430L」で細かな形状や溝を削り出す
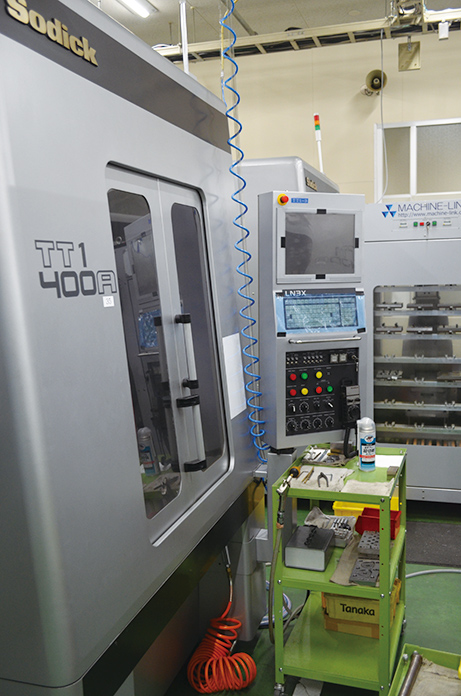
「TT1-400A」とロボットを組み合わせ
自動化に取り組む
また、もともと金型加工用に導入したワイヤ放電加工機「VL400Q」と「ALN400G」は、現在フレームの切り出しに活用。同社では板厚0.8mm以下の場合は、板材を重ねてワイヤ放電加工機でフレーム形状を切り出し、それ以上の厚さの板材ではプレス加工とMCによる削り出しを併用している。
金型を製作せず、ワイヤ放電加工機で板材からフレーム形状を切り出す理由について、田中社長は「ニーズに応じて新製品を市場に送り出すためには立上げのスピードが重要。金型を新たに設計・製作してプレス加工で量産するよりも、ワイヤ放電加工機で切った方が速い」と話す。自社ブランドのフレームはいずれもごく薄い板材を使うことが製品コンセプトとして決まっているため、ワイヤ放電加工機を使う方が製造の柔軟性が高いのだという。
一方、製造の面ではキャパシティの拡大が急務となっている。鯖江市の本社工場と、同社から全設備を供給された大阪府東大阪市の下請けメーカの2拠点で製造を行っているが、今後はいずれの拠点でも設備の更新や自動化を進める。同社の本社工場では、MC2台と多軸ロボットを組み合わせることで、24時間稼働を実現。フレームのレンズ溝を一方のMCで加工し、多軸ロボットでワークを移動させて、もう一方のMCでフレームのねじ穴を加工している。「機械を止めない」をキーワードに、加工だけでなくインサート成形の自動化にも取り組む構えだ。
ワイヤ放電加工機ALN400G と形彫り放電加工機AG40L
ワイヤ放電加工機は金型加工だけでなくフレームの切り出しにも活用
「フレームメーカへの転身を図る部品メーカは失敗する」というジンクスを乗り越え、着々と認知度を高める同社。現状では売上げに占める部品製造の割合が7割を占めるが、将来的には部品とフレームの割合を逆転させる目標を掲げる。
また、自社製品をアピールする場として、小規模フレームメーカとしては珍しく本社内に小売りスペースを設けており、県内外から同社のフレームを求める眼鏡ユーザが来訪するという。「日本のお客様に中国製ではなく日本製の眼鏡をかけてほしい」という田中社長の願いが実現しつつある。
田中社長が日本での生産にこだわるのは、「日本はモノをつくり、輸出することで認められた国」と考え、そのことを誇りに思っているからだ。デジタル技術によるサービスが拡大しても、それで利益を得られるのは一握りの企業にすぎない。
日本のメーカがモノづくりの技術・ノウハウを失えば、日本の若者は自分の国に誇りをいだくことさえできなくなる。
「今やるべきは原点回帰。次の世代に『日本人に生まれて良かった』と思ってもらうためにも、国内のモノづくりを再興させる必要があるのではないでしょうか」(田中社長)。