金属3Dプリンタと
一気通貫のデジタルデータによる
金型づくりで躍進
効率的な冷却回路を金型内部に3D造形してプラスチック成形品の生産性を向上
台湾のプラスチック製品メーカ、Grand Dynasty Industrial Co.,Ltd.(GDI)
台湾のプラスチック製品メーカGrand Dynasty Industrial Co.,Ltd.(GDI)は、自社で行う金型づくりを完全にデジタルデータ化している。また、プラスチック成形の生産性を向上するために金属3Dプリンタを駆使している。そんな先進的な金型づくりを支えるのがソディックの金属3Dプリンタ、ハイスピードミーリングセンタ、V-LINE®射出成形機などの高性能マシンだ。
台湾のプラスチック製品メーカのGDIは、1984年の創業から10年ほどは家族で経営する小規模な射出成形工場だった。
しかし、創業者のご子息で現董事長の林健祥氏が入社した1993年を機に事業を大きく拡大した。林董事長は1989年に米国マサチューセッツ大学でポリマー化学、プラスチック工学で博士号を取得した俊才であり、1993年に家業に加わるとその後の10年間で米・英・独に主な取引先を持つ中小規模のプラスチック製品メーカへと成長させた。
現在、同社の売上は8億台湾ドル(約29億円)で、国別の取引先は米国60%、英国25%、独国10%とほぼ100%が欧米企業だ。社員数は220人で2019年には台湾に3つめの工場を稼働させている。
金型の30%を金属3Dプリンタで製造
当社の強みは金型、成形材料、射出成形の各技術を熟知していることです(林董事長)
同社の主力製品は工具用品、スポーツ用品、消防用装備品などの特殊用品であり、金型の設計・製造から製品の成形までを手掛けている。金型の70%は機械加工で、30%を金属3Dプリンタで製造している。
金属3Dプリンタは、2017年にソディックの「OPM250L」を2台導入した。OPM250Lは、金属積層と切削加工の2つの機能を併せ持った複合加工機であり、加工槽テーブルに金属粉末(SUS)を0.05mmずつ敷きつめ、その粉末層をレーザ照射で溶融凝固させて造形する。一定の積層サイクルごとに切削工具による仕上げ加工を行い、これを繰り返すことで厚い造形物を高精度に加工する。
林董事長は積層造形について「30年前から注目していた」と言う。ちょうど樹脂造形用の3Dプリンタが米国で商品化(1987年)されて間もない頃であり、さまざまな技術が開発され製品化が図られていた最中だ。
「当時、米国で金型関連の知人から積層造形の優位性を聞かされて興味を持ちました」(林董事長)
その興味は褪せることなく、今から10年前には自社の事業にも活用すべく金属3Dプリンタを積極的に調べるようになった。
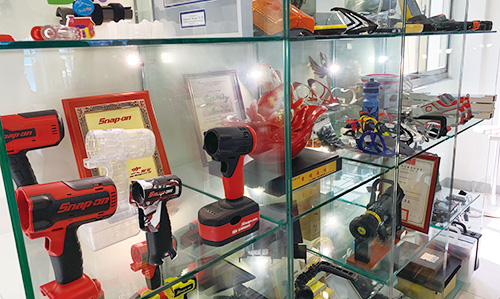
工具などGDIが製造するプラスチック製品
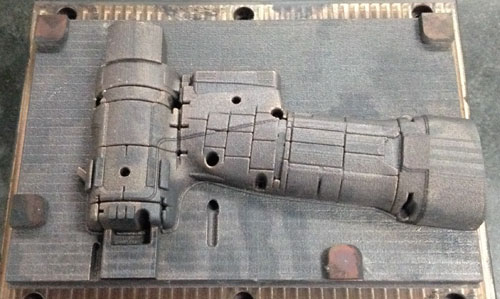
金属3Dプリンタで大型金型を製造する
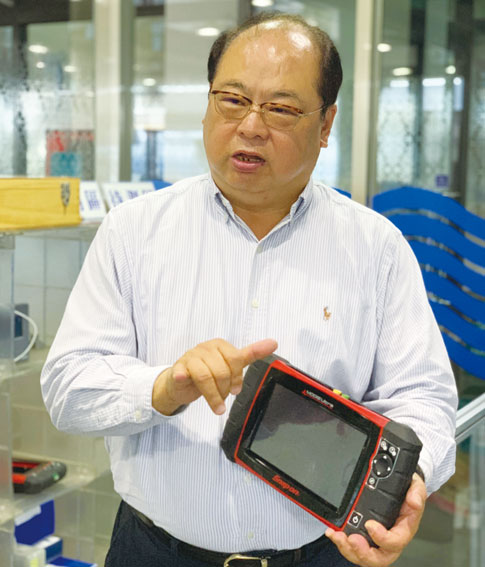
林健祥董事長
いろいろと検討した結果、使いやすくて便利なうえ、
ソディック台湾の手厚いアフターサービスが決め手となり、
ソディック製金属3Dプリンタを導入しました(林董事長)
同社が3Dプリンタで造形する金型は、キャビ・コアの寸法が最大でタテ250mm×ヨコ250mm×高さ250mmと大きい。
また、この金型で数十万ショットの射出成形をするには耐久性が求められるため、型材にはSUS(ステンレス鋼材)を用いる。マルエージング鋼を取り扱う金属3Dプリンタのメーカは多くあるが、SUSで大きな寸法の金型を積層造形できるという条件を適えるためにソディックの金属3Dプリンタを選択した。
金属3Dプリンタで金型を製造するメリットの1つとして、任意の3次元形状を作製できることがある。GDIでもそのメリットを活かした金型づくりを実践している。
それはキャビティの冷却回路の作製だった。従来の機械加工で金型の冷却回路を作製する場合、除去加工のためどうしても加工する形状に制限があった。曲線や3次元形状の冷却回路を設計できるものの実際の作製は不可能だった。そのため同社では、自動車部品用金型(250mm×250mm×250mm)の冷却回路の作製に金属3Dプリンタを使って効果を実証してみた。従来のような切削加工で作製する冷却回路は直線の配管が主体になるが、金属3Dプリンタを用いれば自由曲線の配管を作製できる。そのため、従来の冷却回路では到達できない個所やより広範囲な製品面にも配管を作製できることから、キャビティの冷却に効果を発揮できる。
実際、同社でも従来工法による冷却回路では射出成形後のキャビ・コアの温度差が47℃だったが、金属3Dプリンタで作製した冷却回路により射出後の温度差を36.5℃と10.5℃も下げられた。キャビ・コアの温度差が大きいと成形後の製品に反りを発生させてしまうが、射出成形後の両者の差を小さく(放熱と吸熱の不均衡を是正)できたことにより、製品の反りを改善できた(最大49%の改善)。
この実証では、SUSを用いて52日間で金型を積層造形・加工した。これだけ大きな寸法の金型を積層造形する場合、クラック(割れ)が発生するリスクが高いが、同社では事前にトライ&エラーを重ねながら造形ノウハウ(クラックが発生する原因と条件およびそれを回避するための造形のパラメータの調整)を蓄積し、実証ではみごとにクラックなく金型を造形できた。
その後、同社では金型製造に金属3Dプリンタを積極的に活用し、これまで60型中58型でクラックなく、冷却効果も目的通りの金型を造形している。
同社はOPM250Lに続き2019年にソディックの金属3Dプリンタ「LPM325」を2台導入した。
「切削が必要な金型はOPM250L、切削の必要ない金型はLPM325で造形します」(林董事長)
LPM325は、3D造形と造形物への(2次加工用の)基準面加工のみに機能を限定することで、造形速度を大幅に向上させた機種であり、ソディックの独自技術である「SRT工法」も適用できる。このSRT工法の機能を搭載したLPM325を導入し、金型を3D造形する。
「SRT工法」とは、金属3Dプリンタで必ず発生する残留応力を抑えるための、いわゆる焼入れ処理を応用した技術である。レーザで金属粉末を溶融・凝固させる金属3Dプリンタでは、残留応力によって造形物を収縮させて歪みや反りが発生してしまう。その収縮に対して熱を加えることで、収縮と膨張を相殺し歪みを抑えるのがSRT工法の原理である。実際にソディックの試験ではSRT工法で歪み量を従来の1/10に抑制している。
LPM325では歪みが原因となるクラックをSRT工法によって防げますし、
より大きな金型を3D造形できます(林董事長)
また、LPM325でMRS(Material Recycle System:金属粉末材料の自動排出・供給装置)を付属した。従来は、金属粉末の供給と造形後に残された余分な材料と切粉の回収は作業員が行っていた。それを自動化したのがMRSであり、「金属パウダーの供給や造形後の回収に作業員が不要になり、造形工程の自動化にたいへん有効」(林董事長)と評価が高い。
ソディック製金属3Dプリンタ「LPM325」2台
省人省力化を実現するMRS(金属粉末材料の自動排出・供給装置)付き
同社の金型づくりは完全にデジタルデータ化されている。顧客から供給される3次元の製品データから3次元CADで金型を設計(モデリング)する。その設計モデルをもとに3次元CAE(Moldex3D)で成形品の樹脂流動解析を行い、3次元CAMで加工データを作成した後NCデータに変換して機械加工する。
また、金属3Dプリンタで造形する場合も、モデリングと樹脂流動解析、STLデータへの変換、造形用スライスデータの作成といったようにデジタルデータを一気通貫させて金型を作製する。さらに、成形後の製品は3次元イメージスキャナでスキャニングし、顧客の製品データと照合させて差異があれば修正する。こうした金型づくりのデジタルデータ化は、設計・製造をスピーディにするばかりでなく、成形した製品の品質保証に効果を発揮する。
同社の製品成形で使用するプラスチック材料は1300種類にも及び、その内訳はPE(ポリエチレン)、PP(ポリプロピレン)、PPE(変性ポリフェニレンエーテル)など熱可塑性、熱硬化性、強化プラスチックと多岐にわたる。また、製品は2500種類を製造し、そのための成形法も2色成形、インサート成形、精密成形(成形精度0.02mm)と幅広く使いこなし、さらに真空印刷(ラミネートを150℃で真空で焼き付ける印刷)も手がける。
工具や特殊品の成形後の検査も微に入り細にわたる。その設備も非接触顕微鏡、落球試験機・落下試験機(高速カメラで衝撃破壊を検査)、3次元測定器、耐温・湿度測定器、塩水噴霧試験機(塩分を含んだ水で腐食テスト)、有害物質の測定、高速衝撃機など約30種類の試験機、測定器を揃えて品質を保証している。また、顧客に納品する際は必ず測定報告書も添付する。
製品を検査する際、どの検査項目にするかは当社で自主的に決めています」(林董事長)
顧客が求める品質を保証するために、自主的に検査項目と検査機器を選択して検査している。工具や特殊品は使用中に故障や事故があってはならないため、徹底的に検査を施す。特に特殊用品として米国の消防隊員が使用する防炎マスクやガス検知器(火事で発生する煙の有害成分を分析)はかなり厳しく品質が問われる。
例えば防炎マスクでは、高速衝撃機(80m/秒で金属球を当てる)で耐衝撃性を調べる。火災現場でどんな物が飛来して顔に衝撃を受けるかわからないから、消防隊員を守るための耐久性を保証するのだ。これだけ徹底した品質保証は同社の大きな特徴でもある。
同社の金型づくりはデジタルデータ化されていると述べたが、それを支えるもう1つのポイントが高精度な加工機や成形機だ。LPM325の設置スペースは温度23±1℃、湿度47±10%と稼働に最適な環境に保たれ、そこではソディック製ハイスピードミーリングセンタ「UH430L」も稼働している。UH430Lは、リニアモータ駆動の超高速切削加工機であり、新素材に適応したヘッドや加工シミュレーション支援ソフトを搭載している。
林董事長はUH430Lの導入について、「当社で成形する製品の精度が徐々に上がってきているので、ミクロン精度で加工できる高精度な加工機が必要になってきています。そういう意味では将来を見据えての導入です」と言う。
また、将来へ向けての投資という意味では、2019年に導入したソディックの V-LINE® 射出成形 機「MS200」と「GL150A」も同じ位置づけだ。従来の射出成形機の構造は、スクリュと射出シリンダ(計量/充填)が同じ軸の上に配置されたインラインスクリュ方式のため、プラスチックが逆流して充填量にばらつきができてしまうが、V-LINE®は計量と充填の工程を分離した構造のため、プラスチックの逆流がなく充填量が安定するという特徴がある。この2台の成形機の導入について林董事長は「これも今後の投資という意味であり、高性能な成形機を導入して医療機器など製品のバリエーションも広げていきたい」と話す。
GDIの2つの成形工場にある58台の成形機について、その稼働率を工場内に設置したモニタで確認できるようにしている。また、その稼働状況の情報はIoT(Internet of Things)を活用して外部からタブレット端末などでも確認できる。
さらに、顧客にも同様にタブレットで自らの発注した製品の成形状況をモニタリングできるようにしている。デジタルデータによる金型づくりと品質保証という同社の製品づくりに対する自信の一端が、成形の進捗状況の開示という形ともして表れている。
林董事長は「売上は3年後に15億台湾ドル(約54億円)を目指している」という。そのために最新鋭の設備を導入し、スピーディな納品(例えば、2色成形で受注から試験終了まで45日間)と充実した品質検査を武器に成長を図っていくようだ。金属3D造形での金型づくりも比率を増やしていくという。製造に携わる人員が減少傾向にあり、顧客から金属3D造形を指定されるケースもあるからだ。GDIの先進的な金型づくりは留まることを知らない。