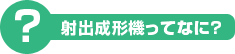
同じ形状の精密なプラスチック製品を大量生産できる機械です。
製造した部品は、自動車、医療業界など多方面で利用されます。
時代をリードする高性能な製品を支える、
ソディックが誇る独自の技術力。
加賀工場で生産するものは、最先端のものづくりを支える機械や技術発展に貢献してきた独自の製品。
その中でも、現在、出荷製品のおよそ90%を占めているのが射出成形機です。その製造工程を追ってみました。
同じ形状の精密なプラスチック製品を大量生産できる機械です。
製造した部品は、自動車、医療業界など多方面で利用されます。
設計
お客様が求める射出成形機の仕様はさまざま。何を製造するのか、どのような環境で製造するのか、標準機にオプションをつけたり、それで実現できないものはカスタマイズして設計します。加賀工場の設計部門は、機械本体、電気回路、ソフトを設計する3部門に分かれていて、1フロアに位置し、各部署が連携を取りながら設計を進行。製品の仕様が完全に決定してから設計に入ることは稀で、お客様のご要望に合わせながら、設計も進みます。
製造・加工
設計が完了したら、必要な部品を調達。部品は国内外のメーカーから調達することもありますが、主要なものは自社で製造していることもソディックの特長です。特に、品質を保つために不可欠なプラスチックを溶融する部品の1つ「可塑化スクリュ」や「可塑化シリンダ」、「射出シリンダ」、「プランジャ」などは加賀工場内で製造。製造する仕様に合わせ、小型なものから大型なものまで工場内で製造しています。
自工場で製造することで、よりスピーディーに納品することもできています。
組立
設計された図面に基づき、組立て製造します。広い工場内に竪型射出成形機の場合は高さ2m以上、横型射出成形機の場合は横3m以上といった大型の製品がずらりと並び組立は進行。基本的に製品ごとに仕様が異なるので、さらにスケールの大きなものや納品先の規格に合わせた塗装などが施されているものも点在。
組立途中で仕様が変わることもあり、この時点で設計担当者が対応することもあります。
出荷検査
完成した製品が正しく稼動するかどうかしっかり確認します。最終的なチェックは1名が担当します。製品ごとに非常に多くのチェック項目があり、製品により1~2週間程度かけて1つ1つていねいに確認していきます。
不明な点があれば、前工程に戻り原因を探っていき、改善していきます。
製品の検査終了後、お客様の立会いのもと、製品確認し、出荷となります。