Core Technology 06 V-LINE®方式(V-ライン®)
プラスチック成形の難解さ
工作機械ではNCプログラムを使って素材から部品を削り出しますが、プラスチック成形では、金型に溶融樹脂を注入、冷却固化して取り出すという一連のプロセスを繰り返します。 大量生産に適した工法でありながら、成形機本体に加え金型、樹脂、成形条件が絡み合い、また熱交換をともなう手法のため見える化が困難とされていました。
成形現場での不確実さ
- 金型の精度と成形されたプラスチック製品の精度が必ずしも一致しない。
- 成形条件は成形機だけに依存するものではなく、金型、樹脂、あるいは環境によって変化する。
- 日々、成形品の出来映えが変化する。
- テスト成形で金型を修正しても、イメージ通りの結果が得られない。
- ピン折れ等の金型破損が散発する。
など、安定した成形を行うにはKKD(経験・勘・度胸)が必要と言われることさえある、不確定要素が高い状態でした。
ソディックの成形への方向性
成形現場では『射出成形=不確実』との認識が甘受されていました。 ソディックの射出成形機開発は、“既存技術には何らかの問題が潜んでいるのでは” との疑問からスタートしました。 ソディックの誇る放電加工機、ワイヤ放電加工機、またマシニングセンタを用いて、高精度な金型を作っても必ずしも、BESTな成形品が保証されるわけではない。 また、成形品生産の経験が少なくても技術に裏付けされた成形技術により、不安定要素を出来るだけ少なくして製品の立ち上げ、製品化を少しでも早く行い、お客様のもの作りをお手伝いしたいとの思いから成形機開発を行いました。
V-LINE®方式による抜群の信頼性
まず、着目したのは当時の主流成形方式であるインラインスクリュ方式への疑問でした。
インラインスクリュ方式の成形機には 逆流防止機構があります。
この方式では、射出に合わせて受動的にチェックリングが着座しますので、着座完了までに逆流を許容しつつ充填していることとなります。
成形を不安定にする最大のポイントがここにあると判断しました。
ソディックでは、可塑化と射出の工程を分離するV-LINE®方式を採用しました。この方式により逆流ゼロ方式を開発しました。
計量後、能動的に通路を遮断完了、次に射出動作を行なうので、計量された樹脂は全て金型へ注入されます。
V-LINE®方式の登場で充填量が正確になり、ここで初めて数値制御が可能になったと言えます。
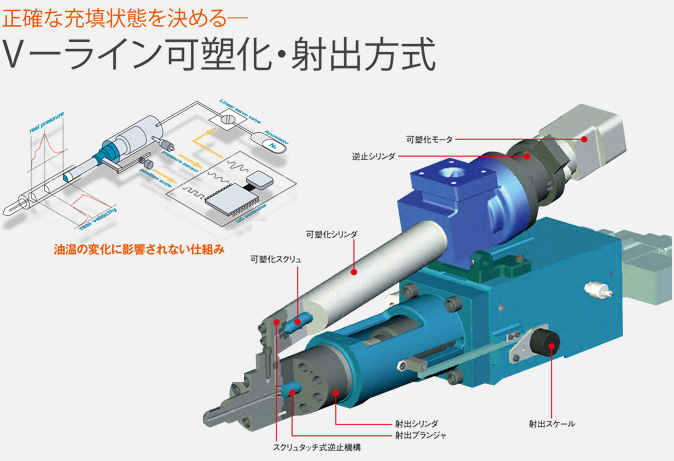
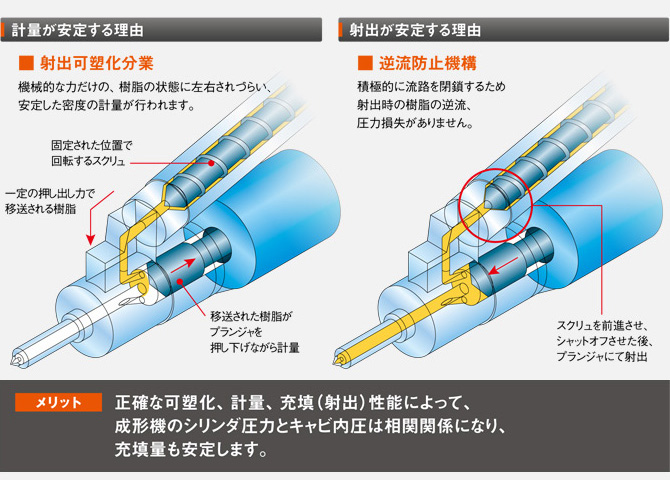