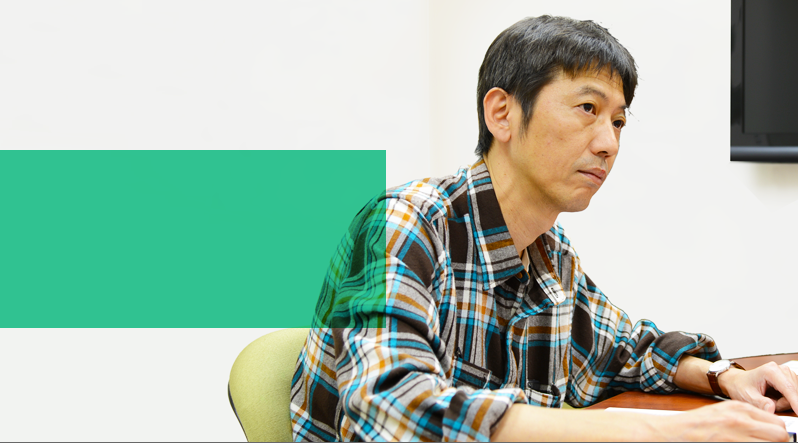
Center Director Working as a hardware engineer in lockstep with the progress in linear motor-mounted machines to create Sodick's leading-edge technologies. Interviewer: Miki Shimamura, Caribou Inc.
<Profile>
After developing power supplies for die-sinker electrical discharge machines at JAPACK'S Inc., he transferred to Sodick in 1992. He was assigned to the Research and Development Division and worked on the commercialization of electroless circuits and finishing circuits for wire-cut electrical discharge machines. From about 1999, he participated in our project to develop a motion controller suitable for linear motors. When Sodick America was established in 2000, he moved to America. After 11 years in the U.S., he returned to Japan in 2011 and re-joined the Research and Development Division. He was appointed as the Center Director of the Advanced Research Center when it was newly established in 2012.
Linear motors are now used in almost all Sodick products.
You were involved with this plan from the experimental stages and
I hear that you witnessed a dramatic moment in the laboratory,
didn't you?
We released an electrical discharge machine incorporating linear motors in 1998. But the incident occurred about one year before that when I entered the testing laboratory alone to test an electrical discharge machine fitted with prototype linear motors. I'd set up the testing environment and I'll never forget the moment I did the first machining test. When I ran the machine, the machining rate was so fast it overturned all common sense. It was probably 2 or 3 times faster. It was so fast that I literally thought “This just isn't possible!” Then a colleague who came to watch the test also said “Something must be wrong here.” But after we performed repeated checks together, the power of linear motors turned out to be real. I had previously worked on several developments that improved machining performance but I had never before experienced such a dramatic jump in performance. It is normally hard to get even a 5% or 10% performance improvement.
How long did the research take?
It took two years. We initially installed linear motors not on a die-sinker electrical discharge machine but on another machine, and the performance wasn't great. We then wanted to try them on an electrical discharge machine. At that time, there was an affiliated company which produced its own linear motors, and we decided to use them.
You then managed to commercialize it.
I heard you celebrated with all staff members.
As a step toward commercialization, we installed the No. 1 mass production prototype in the Research Center at company headquarters. We checked that it operated correctly under the oversight of its inventor, Chairman and Representative Director Furukawa, and several others. After safely confirming that the No. 1 prototype worked as expected, Mr. Furukawa brought out some drinks. Everyone in the testing laboratory then raised a toast to the machine. It was 2 or 3 pm in the afternoon.
That was the instant when our development became a product.