Interview【Sodick User Report】 Edogawa Ward, Tokyo
Matsuki Inc.
Embodying the next generation of mold manufacturers with proven plastic model mold technology and an unique range of in-house products
Leveraging Sodick electrical discharge machines and machining centers
Many people become captivated by plastic models in their childhood, and continue to enjoy them as a hobby into adulthood. Matsuki (Edogawa Ward, Tokyo) is a mold manufacturer that is primarily involved with the injection molds needed to make such plastic models. Under the leadership of Takatsugu Suzuki, who was appointed Representative Director and President in 2013, the company branched out to develop BtoC products while continuing to develop technology to meet the changing demands of the market, which drove increased brand recognition and a rise in orders.
The company first introduced a Sodick die-sinker EDM in 2008, which was followed by the implementation of two Sodick machining centers on the production line. They reported improvements in production efficiency and cost savings, expressing satisfaction with the performance and quality of after-sales service.
The company was first founded in 1978 by President Takatsugu Suzuki’s father, Teruhiko. Mr. Teruhiko trained in the mold division of Marusan Shoten, a model manufacturer believed to be the first in Japan to produce plastic model molds. After gaining experience there, he founded Matsuki as a plastic model mold manufacturer, using the skills he acquired. Since its founding, the company has focused on producing molds for 'scale models,' which produce a faithful scaled reproduction of aircraft, battleships, cars, and other vehicles, as well as 'character models' that bring characters from anime works to life in three-dimensional form. The company rode a boom in character models shortly after the company’s founding in 1979, which coincided with the airing of world popular robot anime that captivated young boys, and this tailwind propelled the company to a robust wave of growth.
President Suzuki first joined the company in 2007. After studying literature at university, he worked for a period at a group company of a major paper manufacturer. It was then that, Mr. Teruhiko, who had led the company until then, experienced a decline in health. Answering a call to “help out with the company,” Takatsugu came on board. After joining the company, he was put in the field, working in mold production using CAD and electrical discharge machining, as well as handling sales. However, in 2013, he was suddenly asked by Mr. Teruhiko to take over running the company, and at the young age of 32, he became the new President. It was not long after that Mr. Teruhiko passed away. “I was honestly surprised to be suddenly thrust into the role of President. Although he attempted to reassure me with comments like, 'You’ll be fine, just call on me if you need anything,' I can't help but wonder if he had a premonition about his own situation,” said President Suzuki. Despite the uncertain start, President Suzuki reflects, “The support of our experienced employees played a major part in helping me navigate this path.”
Mold technology creating organic lines and textures
Compared to industrial parts, plastic models rarely require stringent dimensional accuracy, which is why “appearance is everything,” according to President Suzuki. “We cannot allow for sink marks, and we must carefully consider the placement of parting lines to hide them from view, ensuring that they are positioned in less noticeable areas when the model is complete,” he adds.
The machining techniques required also continue to evolve with changes in market demand. Until now, the company primarily focused on producing scale models and other mechanical models. However, as times changed, character models featuring organic lines and textures, such as the popular bishoujo figures, have also gained in popularity. “Reproducing the texture of hair and clothing presents its own challenges, and requires fine adjustments to the surface roughness during electric discharge machining and surface texturing to achieve the desired effect,” Mr. Suzuki explains. Additionally, the company not only reproduces skin texture through surface roughness, but they also utilize their expertise in multi-color molding technology and unique know-how to portray textures like skin tone. “The quality of such texture reproduction is largely determined by the finish of the mold,” he states.
The fitting adjustments required to express the subtle movements of the joints in character models have become increasingly precise. Each model manufacturer deals with different focus points on orders, and since it often involves a subjective 'element of nuance,' it requires the ability to accurately interpret customer requests and translate them into mold designs. Against this backdrop, the company has increasingly become involved in product design in recent years.
Increased brand recognition with the production of plastic model lures
At the same time, since 2019, the company has been engaged in the development and manufacturing of its own BtoC products as part of efforts to advance new business development initiatives. The first product released as part of this initiative is the 'Plastic Model Lures,' which are modeled after fishing lures. President Suzuki, who sought to take on the challenge of developing the company’s own products in-house, casually brought up the idea to employees during a conversation. It was then that a few fishing enthusiasts among the staff suggested, “Let’s make a model of a lure.” “Upon further inquiry, I was surprised to find that the team had actually been nurturing the idea of developing in-house products and had already created manufacturing data for lures,” Mr. Suzuki adds. The discussions progressed swiftly, and succeeded in completing the product using a prototype of an in-house injection molding machine.
The plastic model lure in-house product, and other plastic models molded using the molds developed by the company.
When the company later exhibited the plastic model lures at a large art and hobby exhibition, it caught the attention of comedians who share information about plastic models. A video featuring the company was published on their YouTube channel, 'Yoshimoto Plastic Model Club,' and gained significant attention. “The development of the plastic model lures has driven brand recognition, leading to inquiries from lure manufacturers with whom we had no previous relationship,” he explains. The company is currently working on the development of a second in-house product.
The development of the plastic model lure has led to an increase in new inquiries.
The company is working on the development of a second in-house product.
‘Accuracy,’ ‘speed,’ and ‘service’
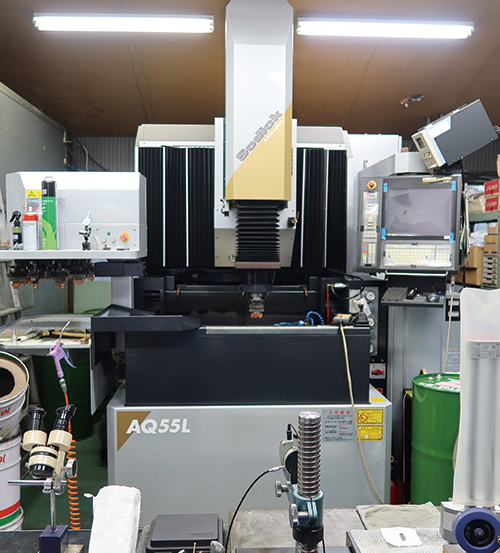
The NC die-sinker EDM AQ55L is
acclaimed for its precision and speed.
Since its founding, Matsuki has enhanced its plastic model mold production technology to meet market demands while also pioneering a new path in the development of in-house products. President Suzuki places great trust in the Sodick die-sinker EDMs and machining centers (MC) that were successively introduced around 2010. “Since I joined the company, we have primarily mainlined Sodick machines,” states Mr. Suzuki.
In 2008, the first Sodick product introduced after President Suzuki took office was the AQ55L, which was the latest NC die-sinker EDM at the time. Mr. Suzuki noted that it was the “high precision and fast processing speed,” that were the deciding factors in the decision to go with the AQ55L. At that time, it was common for nearly all plastic model parts to be given their shape using die-sinking electrical discharge machining, and such tools were essential for the company.
However, the die-sinker EDM from another manufacturer that was mainly being used at the time could not achieve the desired surface roughness, and machining was a time-consuming process. The machine was also plagued with regular cable breakages in the spindle, which caused errors. This was one of the key issues that needed to be addressed to improve production efficiency. “When comparing a number of electrical discharge machines, I was impressed by how much faster the electrode jumping movement of the AQ55L was compared to others. Most impressive was that the desired surface roughness was being achieved despite the increased jump speed. With this, I believed this could be the answer to the issues we were facing at that time,” Mr. Suzuki recalls.
There were other benefits to Sodick products that only became apparent after they were introduced on the production floor. “I remember being impressed at the attentiveness of the after-sales service,” Mr. Suzuki adds. When the AQ55L was introduced, President Suzuki had just been thrust into his role from another industry and had limited knowledge about molds, and even less about electrical discharge machining. “Not only that, my background was in literature. To begin with, even some of the most basic operations proved a challenge, but whenever I called with beginner’s concerns, they would promptly come over, listen, and address the issues,” he shared. Previously, most after-sales support consultations were only ever handled over the phone, but the willingness of Sodick representatives to assist someone inexperienced like me in person helped build a strong sense of trust.
From electrical discharge machining to direct machining with a MC
This strong sense of trust served as a strong source of encouragement, prompting Matsuki to choose Sodick again when a new machining center was needed. In 2009, Matsuki introduced a standalone MC430L unit, followed by a HS430L unit in 2014. Both were the latest models at the time, featuring linear motor drives that enabled high-speed and high-precision positioning. They are also equipped with a structure providing a high level of rigidity to minimize vibration, and they boast high-speed performance of up to 40,000 min-1, enabling precision micromachining with small end mills using shallow cuts.
President Suzuki cites 'the ability to experiment and handle new applications' as an important criterion when selecting production equipment. The idea of introducing a new machining center initially arose from interactions with clients, where he sensed the potential usefulness of a MC that could handle new tasks. “Up until that point, electrical discharge machining was our main focus, but as I learned more about machining centers, I realized that all our machining processes could be done using direct machining,” he said. While there are machining centers from other manufacturers, Matsuki opted against using them due to issues with failure rates and precision. After seeing the MC430L in action, Mr. Suzuki felt confident that it could achieve precise finishes with direct machining. “At that time, there were no other linear motor-driven machining centers available, so they stood out in terms of functionality. This, along with the quality of the after-sales service was the driving factor in our decision to introduce the machining centers,” Mr. Suzuki continued.
After introducing the MC430L, he became confident that Matsuki could produce molds with the same precision using direct machining. While we initially faced skepticism from model manufacturers regarding the shift from electrical discharge machining to MC-based direct machining, they ended up praising the finished molds as being of equal quality. Not only could processing time be significantly reduced compared to electrical discharge machining, but the material costs for electrodes and overall machining costs were also lowered. This led to the decision to unify mold machining under machining centers with the introduction of the HS430L. At the time, there were very few mold manufacturers using direct machining with machining centers for plastic model mold production. “We saw other manufacturers attempt to follow our lead, but they were unable to replicate our success. I believe our success largely stemmed from our existing machining know-how, and the dedication of our research-minded team,” Mr. Suzuki added. By integrating mold machining using machining centers, we were able to increase the number of molds we were capable of producing.
However, we have recently seen a shift in the precision requirements from model manufacturers, leading to a return to electrical discharge machining. Direct machining using machining centers inevitably produce a corner radius, and there have been an increasing amount of feedback indicating that the corners are not defined well enough. “While electric discharge machining has its own limitations, it is seeing a resurgence to effectively meet these requirements,” Mr. Suzuki explained. The price of copper, the material used for electrodes, has surged, leading to rising costs. However, we are currently striving to overcome these challenges with our inherent capabilities on the production floor.
The Sodick machining center MC430L and HS430L
Bringing new production site and capital investments into view
New orders have increased following the development of our plastic model lure products. However, due to the changing situation in China and the depreciation of the yen, mold production that was previously done in China is being reshored to domestic facilities, leading to greater expectations for further order increases. President Suzuki expresses his determination, stating, “Our challenge moving forward will be to effectively address the situation at hand.” “Currently, production is only taking place at our headquarters factory, but I feel that we may need to seek out new production sites in the future,” he continued.
The company is also actively considering capital investment opportunities. Recently, President Suzuki has expressed a desire to upgrade the wire-cut EDMs that have been in operation on the production floor for nearly 20 years, even before he joined the company. The candidate for replacement being considered is, again, a Sodick wire-cut EDM. Specifically, the company is considering the 'AL Series i Groove + Edition,' which features a wire rotation mechanism that allows for machining the entire workpiece from top to bottom using an unabraded wire by feeding the wire while rotating it. “I have strong confidence in the high level of precision achieved with this machine. I also hope that the quality of after-sales service will continue in the future,” President Suzuki added.
As the company approaches its 50th anniversary, it aims to further enhance their mold production technology for plastic models, which they have consistently developed since their inception, utilizing superior machinery and the advanced technical capabilities of the team. At the same time, they will continue to embody a vision for a new generation of mold manufacturers by expanding their range of in-house products, backed by robust technology and fresh ideas.
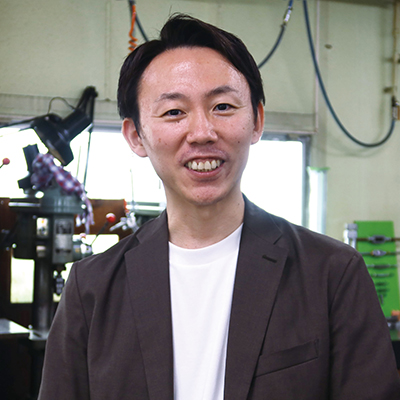
Representative Director
Takatsugu Suzuki
Matsuki Inc.
- Address
- 2-1-7 Matsushima, Edogawa-ku, Tokyo, 132-0031
TEL : 03-3656-5766
- Representative
- Representative Director
Takatsugu Suzuki
- Established
- 1978
- No. of employees
- 12