Interview【Sodick User Report】 New Taipei City, Taiwan
Grand Dynasty Industrial Co.,Ltd.(GDI)
Dramatic Advances in Mold Making Through Metal 3D Printing and
Full Digitalization
3D molding of efficient cooling circuits inside the mold improves the productivity for plastic molded products.
Taiwanese plastics manufacturer, Grand Dynasty Industrial Co.,Ltd. (GDI)
Case Study of Introducing Sodick Metal 3D Printers
Taiwanese plastics manufacturer, Grand Dynasty Industrial Co.,Ltd. (GDI), has fully digitalized mold making in-house. They use metal 3D printers to enhance the productivity of plastic molding production. This advanced mold making is supported by high-performance Sodick machines, including metal 3D printers, high-speed milling centers, and V-LINE® injection molding machines.
GDI is a Taiwanese plastics manufacturer that was a family-run small injection molding plant for about 10 years after the company was founded in 1984.
However, the business was greatly expanded in 1993 when the son of the founder and current president, Dr. Lawrence Lin, joined the company. Dr. Lawrence Lin was a talented graduate who attained a Ph.D. in Polymer Science and Plastic Engineering from the University of Massachusetts in 1989. In the 10 years after he joined the family business in 1993, he developed the company into a mid-sized plastics manufacturer with customers mainly in the US, UK, and Germany.
Currently, the company's sales are NT$800 million (about 2.9 billion yen), with the US and European customers comprising the entire sales, broken down as 60% in the US, 25% in the UK, and 10% in Germany. The company has 220 employees and opened its third plant in Taiwan in 2019.
30% of Molds Fabricated by Metal 3D Printer
According to President Lin, the strength of the company is its thorough knowledge of molds, molding materials, and injection molding technologies.
GDI's major products are special items such as tool parts, sporting items, and fire fighting equipment. They handle all stages of the process from the design and manufacture of the mold to the molding of the product. About 70% of molds are machined and the remaining 30% fabricated by metal 3D printer.
Two Sodick OPM250L metal 3D printers were introduced in 2017. The OPM250L is a compound machine tool that offers metal lamination and cutting functions. It deposits metal powder (SUS) in 0.05 mm layers on the machining tank table, and molds it by melting and solidifying the powder layer by laser irradiation. Finishing with a cutting tool is performed after a certain number of lamination cycles. This process is repeated to achieve highly accurate machining of thick molded objects.
President Lin says that he has been paying attention to additive manufacturing for 30 years. That was the time just after 3D printers for resin modeling were commercialized in the United States in 1987 when various technologies were being developed and commercialized.
President Lin explains that he became interested in additive manufacturing after hearing about its superiority from an acquaintance in the mold-making industry in the US at that time.
His interest did not fade, and about 10 years ago he began to actively research metal 3D printers to utilize them in his own business.
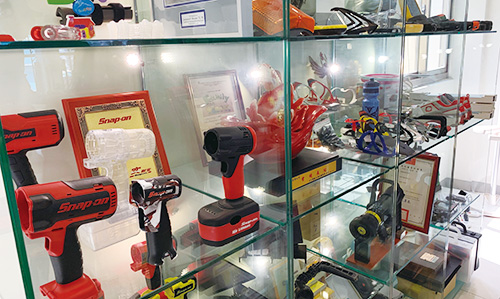
Tools and plastic parts manufactured by GDI
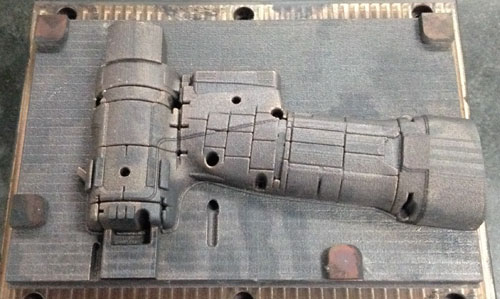
Fabricating Large Molds by Metal 3D Printer
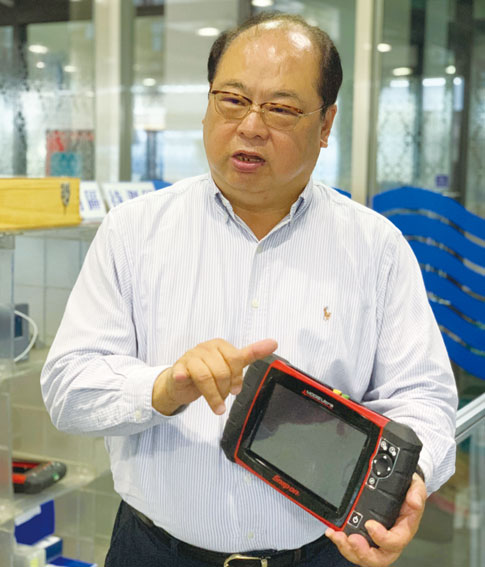
President Lawrence Lin
President Lin explained that, as a result of various investigations, they introduced easy-to-use and convenient Sodick metal 3D printers, and Sodick Taiwan's solid after-sales service was a decisive factor.
The molds that the company fabricates using 3D printers have maximum cavity and core dimensions of 250 mm in length × 250 mm in width × 250 mm in height.
Further, due to the durability required to perform hundreds of thousands of injection molding shots with these molds, SUS (stainless steel) is used as the mold material. Although many manufacturers produce metal 3D printers that handle maraging steel, they chose Sodick's metal 3D printers that satisfy the requirements for additively manufacturing large sized molds from SUS.
Freely Incorporate Cooling Circuits to Enhance the Cooling Effect
One of the advantages of fabricating metal molds with a metal 3D printer is the ability to make any three-dimensional shape you want. GDI exploits this advantage in its mold-making activities.
This is the fabrication of the cavity cooling circuits. As conventional machining is a removal process, it suffers from inevitable shape limitations when making cooling circuits in molds. Although it was possible to design cooling circuits with curved lines and three-dimensional shapes, it was in practice impossible to actually make them. GDI tried to prove the efficacy of metal 3D printers by forming cooling circuits in a mold for automobile parts (250 mm × 250 mm × 250 mm). A cooling circuit produced by conventional cutting machining processes mainly comprises straight tubes, but a metal 3D printer is able to make free-form tubes. As these cooling circuits can reach places that cannot be reached by conventional cooling circuits and cover a wider range of the product surface, they are effective for cooling the cavity.
At GDI, a temperature difference of 47ºC existed between the cavity and the core after injection molding with conventional cooling circuits, but using cooling circuits formed by a metal 3D printer dropped this by 10.5ºC to 36.5ºC. A large temperature difference between the cavity and core results in warping of the product after molding. Reducing this temperature difference after injection molding (correcting the imbalance between heat dissipation and heat absorption) was able to improve the warping of the products (up to 49% improvement).
The mold used for this demonstration was additively manufactured and machined from SUS over 52 days. There is a high risk of cracks forming when additively manufacturing such large molds. Thanks to the manufacturing expertise acquired by GDI through repeated trial and error (determining the cause and conditions of crack development and adjusting the modeling parameters to avoid it), the mold for this demonstration could be fabricated without any cracks.
Subsequently, GDI has been actively utilizing metal 3D printers for mold manufacturing and have created molds that achieve the desired cooling effect, free of cracks in 58 of 60 cases.
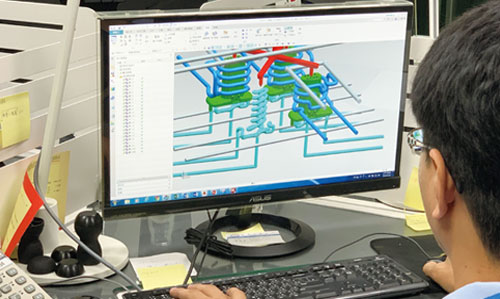
Improving the molding quality with freely
designed cooling circuits
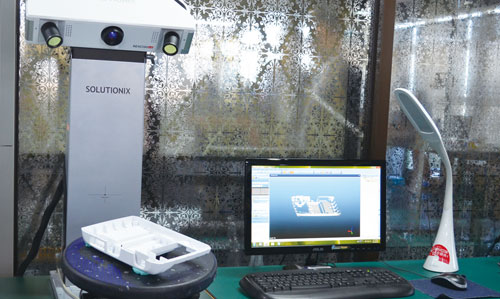
Testers and measuring instruments to guarantee
the quality of molded products
Dividing Use of Two Types of Metal 3D Printers
Following the OPM250L, GDI introduced two Sodick LPM325 metal 3D printers in 2019. President Lin explains that the OPM250L is used for molds that need cutting machining, while the LPM325 is used for molds that do not require cutting machining.
The LPM325 is a model that significantly improves the fabrication speed by limiting the functions to 3D forming and machining of reference surfaces only (for secondary machining). Sodick's proprietary SRT method can also be applied. The LPM325 incorporating SRT method functions was introduced for 3D forming of molds.
The SRT method is a technology that applies a quenching treatment to suppress residual stresses that always occur with metal 3D printers. In a metal 3D printer that melts and solidifies metal powder with a laser, residual stresses occur that make the molded object shrink and cause distortion and warping. The principle of the SRT method is to apply heat to the contractions to cancel out any contraction and expansion and suppress the distortion. In Sodick tests, the SRT method suppressed the distortion to 1/10 of the conventional value.
President Lin explained that by using the LPM325, the SRT method eliminates the cracks caused by distortion and permits the 3D fabrication of larger molds.
In addition, the LPM325 is equipped with an MRS (Material Recycle System) that automatically supplies and discharges the metal powder material. Previously, workers had to supply metal powder and collect any excess material and chips left after mold fabrication. MRS automates this process, and President Lin highly regards it as being very effective in automating the fabrication process by eliminating the need for workers to supply the metal powder and collect it after fabrication.
Two Sodick LPM325 Metal 3D Printers
Equipped with MRS that automatically supplies and discharges metal powder material to save labor
Digitalized Mold Making
GDI's mold making is fully digitalized. Molds are designed (modeled) using 3D CAD from the 3D product data supplied by the customer. Based on this design model, the resin flow analysis for the molded product is performed by 3D CAE (Moldex3D) and the machining data is created by 3D CAM, then converted to NC data for machining.
Also, fabrication with a metal 3D printer is fully digitalized, from modeling and resin flow analysis, conversion to STL data, to creation of fabrication slice data. In addition, the molded product is scanned with a 3D image scanner and verified against the customer's product data to correct any differences. Such digitalized mold making not only speeds up design and manufacturing, but is also effective for guaranteeing the quality of the molded products.
Comprehensive Quality Assurance
GDI uses 1,300 types of plastic materials to mold its products, including PE (polyethylene), PP (polypropylene), PPE (modified polyphenylene ether) and other thermoplastic, thermosetting, and reinforced plastics. In addition, to manufacture 2,500 kinds of products, they widely use a variety of molding techniques, such as two-color molding, insert molding, precision molding (molding accuracy 0.02 mm), and also handle vacuum printing (printing laminate in vacuum at 150°C).
Inspection of molded tools and special products is also fine and detailed. A range of about 30 testers and measuring instruments is used for quality control, including non-contact microscopes, drop ball testers/drop testers (high-speed camera for impact failure inspection), 3D measuring instruments, temperature/humidity resistance testers, salt spray testers (corrosion test with water containing salt), instruments to measure harmful substances, and high-speed impact testers. A measurement report is always supplied when products are delivered to the customer.
President Lin explains that GDI voluntarily decides which inspection items to select when inspecting a product.
To guarantee the quality required by the customer, the company voluntarily selects the inspection items and inspection equipment to use for the inspections. Thorough inspections are performed on tools and special products as damage or accidents are not acceptable during use. In particular, special products such as flameproof masks and gas detectors (to analyze harmful components in smoke generated by fires) used by fire fighters in the United States are subjected to quite strict quality inspections.
For example, the impact resistance of flameproof masks is tested with a high-speed impact tester (metal ball impact at 80 m/s). This guarantees the durability to protect the firefighters at a fire site where it’s not possible to know what flying objects may hit the face. Such thorough quality assurance is a major feature of GDI.
Improving Manufacturing Technology with High-Precision Machine Tools and Molding Machines
It was mentioned that GDI’s mold making is fully digitalized, and another point that supports it is high-precision machine tools and molding machines. The location where the LPM325 is installed is maintained at a temperature of 23 ±1ºC and humidity of 47 ±10%, which is the optimum environment for operation. The Sodick UH430L high-speed milling center is also operating there. The UH430L is a linear motor-drive, ultra-high-speed cutting machine equipped with a head adapted to new materials and processing simulation support software.
President Lin explained that the UH430L was introduced because a highly accurate machine tool capable of machining at micron precision was needed due to the gradual increase in the accuracy of the products molded by the company. In that sense, it was introduced with a view to the future.
The Sodick MS200 and GL150A V-LINE® injection molding machines, which were introduced in 2019, are positioned the same way in terms of investment for the future. As the construction of a conventional injection molding machine employs the in-line screw method in which the screw and the injection cylinder (measuring/filling) are arranged on the same axis, the plastic can flow backward and cause discrepancies in the filling volume. However, the V-LINE® is constructed with separate measuring and filling stages to eliminate the backflow of plastic and ensure a stable filling volume. President Lin said that the introduction of these two molding machines was also an investment in the future, and that he wanted to introduce high-performance molding machines to expand the variety of products such as medical devices.
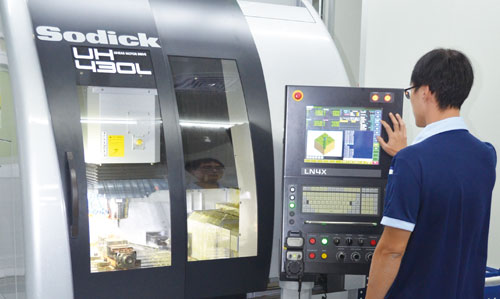
UH430L high-speed milling center introduced
for higher accuracy and finer machining
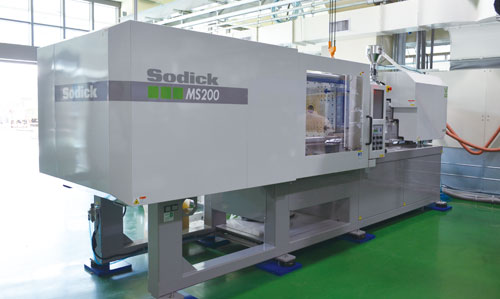
Two Sodick V-LINE® injection molding machines
introduced to expand product variety
Advanced Mold Making that Never Stops
The operation rate of the 58 molding machines installed in the two GDI molding plants can be observed on the monitors installed in the plants. In addition, the Internet of Things (IoT) can be utilized to check information about the operating status using a tablet computer from outside.
Also, the customer can use a tablet to monitor the molding status of the products that were ordered. Part of GDI’s confidence in manufacturing products based on digitalized mold making and quality assurance is also expressed in its disclosure of the molding progress.
President Lin said that they are aiming for sales of NT$1.5 billion (about 5.4 billion yen) in three years. It seems that GDI is striving to grow through the introduction of state-of-the-art equipment, rapid product delivery (for example, 45 days from ordering to completion of testing with two-color molding), and thorough quality inspections. It is said that the proportion of molds made by metal 3D printing will also increase. This due to the decreasing number of people involved in manufacturing and the cases where the customer specifies metal 3D printing. GDI’s advanced mold making activities will never stop.