Interview【Sodick User Report】 Higashikurume City, Tokyo
Okugi Manufacturing Y.K
Specializing in machining ultra-precision parts by wire-cut electrical discharge
Correctly differentiating the use of oil and water EDM
President Yukihiro Wake with Linear Motor Drive Ultra-Precise Wire-Cut EDM AP200L
OKUGI Co. Ltd. of Higashikurume City, Tokyo, is a metal processing company that specializes in wire-cut electrical discharge machining.
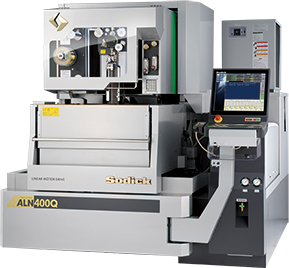
Linear Motor Drive,
High-Performance Wire-Cut EDM
ALN400Q
While they also handle die-manufacture and press work, the core business is ultra-precision parts machining.
They boast diverse customers across the semiconductor and medical industries, as well as research institutes.
The company possesses two wire-cut electric discharge machines using oil and two using water and is able to appropriately differentiate the use of wire diameters from 0.03 to 0.2 mm to meet the customer's required specifications. A particular specialty is oil EDM using ultra-fine wires that allows machining to a surface roughness of 0.1 μm Rz and dimensional accuracy of ±1 μm.
Despite being a small company, OKUGI actively works to improve work efficiency through the remote control of machines and digitalization of information management.
They take on new challenges every day, such as actively distributing videos on YouTube and developing playful products that incorporate the best of their technology.
Never-say-die attitude
Founded in 1951, OKUGI originally manufactured press dies and mass-produced items. As die manufacture by electric discharge machining began to become more widespread in the 1980s, the company starting sub-contracting out wire-cut electric discharge machining to an external partner company.
However, as the cost of payments to the partner company started to blow out, they decided to introduce their own wire-cut electrical discharge machine.
But that wasn’t the only reason. President Yukihiro Wake, the second generation of the founder, confesses his feelings at the time, saying, "I wanted to win the acknowledgment of the senior employees." "As the son of the president, I was always looked on with curious eyes by people wondering ‘what can the man do?’."
So, I thought, "I’ll do wire-cut electrical discharge machining that no one in the company can do." (President Wake)
In 1985, when purchase permission was given by his predecessor, he was introduced to five machine manufacturers through a trading company.
He then made drawings in the same way as when he sub-contracted work to the external partner company, and had them demonstrate production by inputting information from the design drawings. As a result, OKUGI introduced Sodick's water-type wire-cut electrical discharge machine EPOC-500, which has a large, easy-to-see screen and seemed to be the easiest to operate.
But he struggled at first. This was the era before modern CAD and producing the drawings was a nightmare. To make things worse, there was no-one to consult within the company, and he had to handle all the design, setup, and post-processing himself. If he didn’t understand something, he relied on contacting the Sodick Technology Center for advice. "Then, with my never-say-die attitude, I just kept on driving forward." (President Wake)
However, after a few years, he acquired all sorts of expertise related to machining. The timing was good for the company, as it was constantly receiving orders for die-cutting LCD film from special film manufacturers. They couldn't keep up with one machine and increased the number of machines to three. As the wire-cut electrical discharge machines are semi-automatic, after you set one up, you can move on to some other job.
That is how he learned how to manage his work.
Paving the way with foresight
The turning point came in late 1990. At that time, a Sodick sales representative told Mr. Okugi about their AP200 oil-type EDM machine and suggested they give it a try. Until that time, the limit of the wires that could be used on the water-type EDM machines was 0.15 mm diameter, but the oil-type EDM machine used ultra-fine wires of 0.05 mm or even 0.03 mm diameter and they were told that "not many places are machining with such ultra-fine wires."
When he heard that story, Mr. Wake remembered how a special film manufacturer client had advised him that they need to have their own technological capabilities so that the company can survive even if they lose this current work. "It wasn't recommended by anyone beyond that, but I decided to introduce the oil-type EDM machine because I thought it would be useful, provided I had know-how about ultra-precision machining." (President Wake)
At that time, the number of film die-cutting jobs was increasing, so they didn't need to embark on ultra-precision machining, but he saw it as an opportunity for capital investment. A few years later, much of the demand for press dies went to China, and film die-cutting jobs were also on the decline. There was demand only for plastic molds, but this wasn’t a tasty proposition because of the excessive competition. Therefore, he decided to take the plunge and shift the company’s focus to ultra-precision parts machining.
"There are a lot of companies around here that do 5-axis machining , but wire-cut electrical discharge machining is definitely far superior in terms of accuracy," says Mr. Wake. For example, if you are asked to make the corner radius of a small square hole in the hundredths of a millimeter range, that is difficult to handle by machining. Waveguides have a square hole in the middle of a round hole, and even if the positional relationship to the round hole has a tolerance of ±2 μm, the company's technology can properly finish it to that those dimensions.
Properly differentiating water-type and oil-type EDM machines
At the moment, the company has four wire-cut electrical discharge machines. The water-type EDM machines are AQ560L and ALN400Q and the oil-type EDM machines are AP200 and AP200L, all manufactured by Sodick. Among these, the company specializes in oil EDM with ultra-fine wires.
Regarding the difference between water and oil types, Mr. Wake points out that oil offers better surface accuracy and more stable finishing dimensions. Compared to water, oil offers better insulation and a narrower discharge gap, which saves discharge energy and makes it suitable for micromachining with a small machining allowance using fine wires. Also, oil-type EDM machines are more resistant to corrosion and rust than water-type machines. In the case of a water-type EDM machine, the workpiece must be taken out immediately after machining. With an oil-type EDM machine, however, corrosion and rust do not occur if the workpiece is immersed for a while, letting you take time in setting up post-processing.
On the other hand, water-type machines take the winner’s flag in terms of cooling efficiency and machining speed. In addition, as each oil-type EDM machine requires 500 liters of electric discharge machining oil, fire protection equipment is essential. As a result, OKUGI does the oil EDM in a separate building from the main factory.
A water EDM machine is employed when using wires of 0.1 mm diameter or above. Using this class of wire in an oil EDM machine requires a longer machining time.
Whether to use water or oil EDM is determined by considering the cost requirements of the customer and the geometry of the machined product.
Performing water-type wire-cut electrical discharge machining
Prior arrangement with the customer is important
In recent years, oil-type wire-cut electrical discharge machining has become quite popular, but OKUGI’s technological expertise is superior to other companies in the industry. "Someone in our industry who uses a wire-cut EDM machine made by another company boasted that he had machined a 0.04 mm diameter groove using 0.02 mm diameter wire. He was shocked when I told him that we could do the same thing with 0.03 mm diameter wire." (President Wake)
Mr. Wake is proud that OKUGI is second to none in terms of processing technology, even compared to others in the industry who use the same Sodick wire-cut EDM machines.
So what’s the difference if they all use the same machines? "Current EDM machines thread the wire automatically, but for many years I did that myself. That's why, even after I started using automatic wire threading, I can still understand the condition that the wire and workpiece are in at any time." (President Wake)
They also use jigs well. For example, the company has grinding machines because it used to use to make molds. Mr. Wake explains, "Grinding off surplus plate after removing the part, and putting the workpiece on it lets you make it horizontal, and making a single hole in the plate allows you to obtain all the coordinates. When you want to tilt the workpiece, you do not actually tilt the workpiece itself but tilt the jig and put the workpiece on it. More stable dimensions can be obtained by making a simple and effective jig rather than by a poor attempt at clamping ."
However, Mr. Wake once said, "The most important thing is to make arrangements with customers in advance."
Most ultra-precision machined parts have a small order quantity. In particular, there have recently been many orders for a single item with a tolerance of ±2 μm.
However, even if a customer orders only one part, OKUGI asks them to supply at least two material blanks. The first blank is used to determine the dimensions and manufacture starts on the second blank after the measurements are complete. They properly communicate to the customer the approximate thickness of the desired blank material and the need for a jig for machining. In addition, they carefully ask about the customer's environment, such as whether the workpiece will be subjected to hole drilling or other post-processing that may change the dimensions after delivery. "Making arrangements in advance avoids failures and ensures most customers are satisfied, even if we exceed the original budget," said Mr. Wake.
Operation remote from the machines
OKUGI also employs Sodick's DiPro CAD/CAM programming software that automatically recognizes the wire machined parts in the drawing and makes it easy to create the program. His son, Naomichi Wake, is good at utilizing this function. In particular, rather than using this function in front of the machine, the company feels it is advantageous to remotely control the machine from a personal computer.
"A simple shape or creating a single drawing is handled more easily in front of the machine, but when it involves somewhat more complicated operations such as nesting, it's better to do it carefully in another place." (Naomichi) While Naomichi is performing these operations using DiPro in the measurement room next to the factory, the machine is doing another job so there is no wasteful setup.
A timer function is also valuable. The company's machining setup is basically done by the evening when they’d really like to switch to automatic operation mode and go home. But you have to come back to work at night, as the machine stops to perform core processing called "cut-off." However, if you are not in a hurry and know that the core processing takes an hour to complete, you can set the timer to one hour before you leave for work. This frees you from night shifts which can be exhausting.
"It may seem like a simple function, but it's a very helpful feature for us," says Naomichi.
President Yukihiro Wake and his son Naomichi
Self-made goods as gifts sent to payers of the hometown tax
Some goods produced by the company are sometimes talked about around town. One of these is the metal jigsaw puzzle.
These are completely different from the products they usually make, but they started making them to showcase the company's technology at exhibitions .
Thinly slice hardened SKD material. After polishing comes an elaborate construction process in which each piece is cut out by wire-cut electric discharge machining and assembled when 25 pieces is reached. The clearance between the pieces is 5 μm, and are so fine that they look like a single piece of metal polished to a shiny finish.
"You might think it's just merchandise, but they embody our technological expertise," said Mr. Wake.
These jigsaw puzzles are given as thank-you gifts to payers of the hometown tax in Higashikurume City
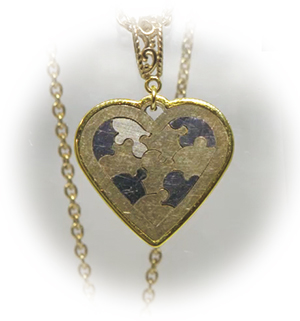
Thanks to their uniqueness, these goods are also used as thank-you gifts to payers of the hometown tax in Higashikurume City, Tokyo. In addition to the jigsaw puzzles, OKUGI also makes nameplates and antibacterial hooks.
"Due to the small number of orders for each ultra-precision part manufactured by EDM, it is essential to increase the number of customers. Recently, orders have come from all over Japan, probably because of the success of our ingenious web site. However, technological innovation is always advancing day by day, and we have to be careful not to miss the wave," said Mr. Wake.
Yukihiro Wake, Representative Director, President
Okugi Manufacturing Y.K
- Address
- 3-14-27 Hachimancho, Higashikurume City, Tokyo
203-0042
TEL:042-471-0867
FAX:042-478-2076
- Founded
- 1951
- Established
- 1957
- Number of employees
- 6
- Capital
- 5 million yen
- URL
- https://okugiss.jp/