Interview【Sodick User Report】 Uji City, Kyoto Prefecture
TOP inc.
Responding to the Need for Ultra-fine Connectors with our Micron-level die Machining
Technology and Unique Molding Know-how
Sodick's Molding Machine Combines Burr Reduction and Fast Cycle Time
Connectors, the company's main product line
Connectors are indispensable for familiar electronic devices such as smartphones, PCs, and home-use game consoles.
The top of the factory in Uji City, Kyoto Prefecture, handles everything from the design and manufacture of precision molds for its connectors to mass production.
The company's strengths include mold design that takes material characteristics into consideration, mold machining in micron increments, and an automatic 100% inspection system that does not overlook defective products.
This is especially true in the area of molding, where the company has developed unique know-how over many years, and has achieved stable mass production of fine connectors by making full use of the LP20EH3 injection molding machine manufactured by Sodick.
A male pin is pressed against the female mold to form a connector groove.
In 1988, President Toshihide Tsukino, who worked as a grinding engineer, established the company independently. Initially, the company only handled parts machining with a grinder, but customers urged the company to turn its attention to molds as well, and it gathered together staff with skills in electrical discharge machining, milling, and assembly to build a system for mold production. The company began taking orders for precision molds in 1996. Seven years later, in 2003, we introduced an injection molding machine to our subsidiary, KTP, and started the molding business. In 2012, the company absorbed the molding business and now handles everything from mold design and fabrication to mass production in-house.
Currently, the company's main products are micro connectors ranging from several millimeters to several centimeters in length. Most of them are for smartphones, but some are also used for PCs, home game consoles, and cloud platforms for AI services. The main molding materials are LCP (liquid crystal polymer) and PPS (polyphenylene sulfide). Using 8-cavity and 16-cavity molds, the average monthly production of one type of product is 2 million, and the maximum monthly production is 10 million. It also manufactures joint parts for machine tools as a relatively large product.
Manage the cumulative dimensions of mold pins in μm
Grinding processing technology, which is also the founder of the company, is indispensable for making dies to stably mass-produce connectors. Connectors have fine grooves into which terminals are inserted, and the grooves are formed by filling resin into the gaps created by abutting male pins (protrusions) against female molds. The number of grooves (called “number of pins”) varies from one connector type to another; for example, a certain series of connectors has variations in the number of pins from 9 to 61. If the number of pins is 9, then 9 pins are incorporated into the mold; if the number of poles is 61, then 61 pins are incorporated into the mold. How accurately the pin can be machined with a grinder greatly affects the quality of the die.
Furthermore, President Tsukino says, “Even if the drawing says that the tolerance is 1 µm, it does not mean that an error of 1 µm per pin is allowed.” Even a 1 µm error would be 20 µm if 20 pieces are stacked on top of each other, and a negative error would result in a gap in the mold and burrs.
“It is difficult to limit the error to 1 µm or 2 µm when 10 or 20 pins are stacked on top of each other, and the error for each individual pin is close to zero. The grinding accuracy required to achieve this is the key to mold making,” says President Tsukino.
Pins machined with a grinder. Skilled craftsmanship shines through
The company has 10 surface grinders “F-515HDII” made by Nikko, and six veteran engineers are in charge of machining in micrometers. The company also emphasizes the precision of electric discharge machining, which is performed after grinding, and has a full lineup of Sodick electric discharge machines, including Sodick's AP1L ultra-precision die-sinker EDM machine and the AQ325L wire-cut EDM machine.
For the electric discharge machine, we chose Sodick products with an emphasis on precision.
In-house development of automation and inspection equipment
In addition to its machining technology, the company's strength lies in its molding equipment for precision molding. When introducing injection molding machines, emphasis is placed on the accuracy aspect. Each connector weighs only a few milligrams, making control technology essential for stable weighing of small amounts of material. The straight-line accuracy of mold clamping is also important to prevent mold damage. From this perspective, the company owns 33 injection molding machines with mold clamping forces of 18 to 50 tons, including Sodick's LP20EH3 (hereinafter referred to as EH3). Sodick's products are used for LCP molding, while other companies' products are used for PPS molding, taking into consideration the compatibility between the material and the molding machine.
Even with high-precision molding machines, stable mass production of connectors is not possible without the know-how to use them. Depending on the material to be molded, the filling speed, mold temperature, cycle time, and other factors are finely adjusted. For example, for materials such as PA46 (polyamide 46), which easily degenerates after a long residence time in the molding machine, the cycle time is set shorter. The company also designs and develops moldings that can handle short cycle times.
The company also utilizes equipment developed in-house for quality control, which is essential for connector manufacturing. The company manufactured an image inspection system that combines a commercially available parts feeder, camera, and image inspection system with its own conveyor system to automate all inspections and eliminate visual inspection variation and errors. Initially, specialized machines were made for each type of connector, but now the company is developing general-purpose machines that can handle different types of connectors.
If defective products are released, not only customers but also end-users will be inconvenienced. We believe that total inspection using image inspection equipment is essential to maintain quality. (President Tsukino)
Inspection room lined with imaging inspection equipment developed in-house
Achieving a significant increase in productivity with a cycle time equivalent to that of the toggle type
Sodick's injection molding machines are indispensable for the stable mass production of connectors that the company pursues. The first one was introduced about 10 years ago, and the number has been gradually increased since then. Currently, the EH3 accounts for 10 of the 33 injection molding machines, the largest number.
The injection molding machine used before the introduction of the Sodick machine was a “toggle type” with a fast mold opening and closing speed, which was advantageous in reducing cycle time, but burrs during molding were an issue. Among resins, LCP has low viscosity when melted and is prone to burring.
Sodick's sales representatives suggested this method, and introduced a direct-pressure “LD20EH2” (LD20EH2 is the predecessor of LP20EH3) that uses uniform pressure to tighten a large area of the mold. As a result, burrs were improved, and troubles of die slippage were also able to be reduced. In addition, Sodick's unique “V-LINE®”, which separates the plasticization and injection processes, accurately plasticizes, weighs, and fills the resin, and was well suited to the injection molding machine elements that top management wanted.
On the other hand, now cycle time became an issue. At a site such as this company, where small parts are mass-produced, a one-second difference can have a significant impact on manufacturing costs. To eyes accustomed to the speed of the toggle type, the “pause for breath” of the direct pressure type was quite noticeable.
The EH3, introduced in 2015, solved this problem. Hiroshi Maeda, general manager of the Molding and Production Department, said, “The EH3 is an amazing machine, and I don't mean that in a flattering way. The cycle time is almost the same as that of a toggle-type injection molding machine, the repeatability is very high, and the pin breakage problems that used to occur with toggle machines have been completely eliminated.”
The LD20EH2 had a fast cycle time of 8 seconds, which was reduced to 3.5 seconds for the EH3, achieving a significant increase in productivity. The company has so much confidence in the EH3 that it recommends its customers who visit the factory to install it.
Sodick's highly acclaimed LP20EH3
Toward “molding that does not rely on human senses”
As electronic devices continue to become smaller and more sophisticated, connectors incorporated into boards need to be smaller in size. Therefore, the company is trying to develop a connector with a groove pitch of 0.2 mm, which is even narrower than the conventional 0.25 mm. President Tsukino says, “Narrower pitch allows for smaller size and greater functionality, but it also makes die machining and molding more difficult.”
As connectors become more sophisticated, the challenge for the future is how to build “molding that does not rely on human senses.” (President Tsukino) “In fact, there are still many aspects of connector molding that rely on human senses, such as setting conditions during start-up and lot inspections during mass production,” says President Tsukino. Maeda general manager and other experienced workers are responsible for setting molding conditions. In addition, although the system has already been constructed to acquire logging data from the molding machine and to stop the molding machine if a defect is found by sensing the variation in molding quality, the lot inspection every 4 hours is indispensable because there are defects that cannot be caught in the case of fine connectors. If AI and various sensors can be used to complete these tasks within the molding machine, it will lead to significant labor savings.
Maeda, general manager, wants to be able to check the monitor image of the mold monitoring device on the operation screen of the molding machine. A monitoring device is installed on the molding machine to prevent mold damage, but the operator has to look all over the place because the monitor image confirmation screen and the molding machine operation screen are separate, which is not user-friendly. To prevent accidents during start-up, which requires quick operation, the monitoring system must be linked to the molding machine.
In the future, the company will focus on meeting the needs of existing customers for narrow-pitch connectors and other products, as well as on developing new customers by leveraging its technologies cultivated in the manufacture of fine connectors. As President Tsukino says, “We would like to cultivate demand in the medical equipment field, which requires precision,” the company, which has expanded its business from parts machining to mold fabrication and connector mass production, is already looking ahead to the next step.
Toshihide Tsukino
Representative Director, President
TOP inc.
- Head office address
- Zip code: 611-0042
32 Kasugamori, Oguracho, Uji City, Kyoto Prefecture
TEL:0774-24-5525
- Representative
- Toshihide Tsukino Representative Director, President
- Established
- 1988
- Business activities
- Ultra-precision plastic mold manufacturing,
Molding and manufacturing, Industrial connectors,
Consumer connectors,
Other precision electronic components
- URL
- https://www.top-kyoto.com/
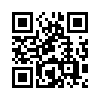