New manufacturing
by AM (Additive Manufacturing)
Value for what no one can do
Sodick’s metal 3D printer
In February of this year, HAMADA KOUSYOU CO.,LTD, which handles everything from the production of resin and press molds to the production of small amounts of molding, introduced metal 3D printers using the business reconstruction subsidy. The aim is to provide a molded product for a security lens cover that suppress warping, using a mold with a freely designed water tube that has a high cooling effect.
Yukio Hamazaki says, “In the future, we want to make things that can only be made with metal 3D printers.” We interviewed the president about the company’s initiatives.
The company was founded in 1982 by President Hamazaki as a consignment manufacturer of die design. Originally, President Hamazaki was responsible for the design of equipment and dies at a parts manufacturer. “At that time, designs were handwritten by drafters and defects in drawings were covered by processing.” Since the design was quick and we were able to arrange for the modification of the drawings and molding, we were nominated by various users.” (President Hamazaki)
In addition, the president of the company told him to learn how to process, so he learned CAM (at the time it was automatic programming). “At a time when NC was not common. I cannot forget when I showed a craftsman how to use CAM and he murmured, 'Our time is over.’” More than that, I felt that it was profitable to do things people aren't doing.
Based on this experience, after founding the company, we not only took on design orders but also began producing molds, such as ZAS molds, rubber, resin, and press molds, one after another. However, with the belief that “molds are just one part of our business. To make money, we need to do things that other companies don't do,” so we started developing our own brand products. "AUTO CLOSER" which automatically opens and closes windows in response to rain, wind, etc. and a split manufacturing method of helical gear and worm gear (patented) were developed.
Patented helical and worm gears
About seven years ago, President Hamazaki began examining the usefulness of metal 3D printers. When he learned CAM, he probably had the experience that “manufacturing that other companies can’t do is profitable.” “In addition, since only necessary materials are used, energy-saving manufacturing is possible. It also meets the trend of SDGs (sustainable development goals)" (President Hamazaki).
In February of this year, Sodick’s metal 3D printer “OPM250L” was introduced using the fourth reconstruction subsidy. The aim is to print a free water pipe in a resin mold to make a molded product of a security lens cover that suppresses sink and warping. "Even if the performance of the security lens has been improved, it is necessary to increase the degree of transparency of the cover in order to make the best use of it. To prevent sink and warping, we need molds made by 3D printers that can print free water pipes,” said Takashi Yasue, general manager of the resin and metal departments, and prototypes have already been produced.
Printing a mold for a security lens cover that requires excellent surface roughness
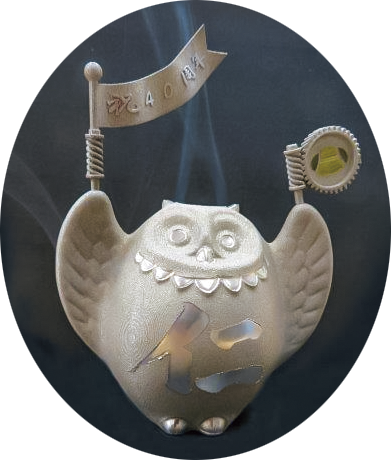
The printed “fragrant owl”
is hollow inside and
can be filled with incense.
Nevertheless, we are planning to use metal 3D printers in a wide range of fields, not just for security lens covers. President Hamazaki has already envisioned several uses. First, molds for molded products with uneven wall thicknesses. “Since we can design cooling water pipes freely, we can create parts that were previously difficult to print.” The rest are parts with undercuts. “We want to create components that can only be made with 3D printers and make people wonder how they were made.”
As in the case of CAM, President Hamazaki says that machining that no one can do is not only an appealing point that other companies don’t have but a potential means of creating value. At the age of 70, he laughs and says,
“I want to retire now,” but his motivation to take on challenges has not waned yet.