Interview【Sodick User Report】 Tokamachi City, Niigata
Niigata Precision Co., Ltd.
Discovering new customers through a combination of being the first to adopt high-precision fabricating equipment and artisanal techniques
~Creating replicas of Japanese swords with the Sodick Machining Center (MC) ~
Niigata Precision is mainly engaged in machining precision components and automated machinery used at production sites. In the field of component manufacturing, the company is skilled in microfabrication at the μm level, handling a wide variety of materials including ceramic and cemented carbide. In automated machinery construction, their framework covers everything from accommodating detailed customer specifications in the design phase, to component machining, assembly, and testing. In recent years, they have devoted themselves to developing new domains, beginning with direct-to-consumer efforts such as producing sophisticated replicas of Japanese swords.
The support behind their spirit of taking on challenges is their aggressive equipment investments. Niigata Precision is fastidious about adopting high-precision machinery, possessing a machining center (MC) and a full lineup of equipment such as various electrical discharge machines. Boldly adopting a Sodick linear motor-driven MC, a piece of equipment that is over-engineered for their main business, led to their Japanese sword replica business and the resulting business of developing medical scalpels. The company is making it their mission to distinguish themselves from others by focusing on staff education in machinery handling and by taking on difficult machining jobs that no other company can duplicate.
The main factory and Mechatronics Center located in Tokamachi City. The Uonuma Factory and Technical Center are located in Uonuma City.
Niigata Precision was established in 1996. The name comes from the founder's desire to become the most precise metal machining operation in all of Niigata Prefecture. Initially, the company mainly machined components for automated machinery, but in 2007 the Automated Machinery Department was established and they began designing and producing automated equipment. Currently, the main factory and Mechatronics Center are located in Tokamachi City, Niigata, with the Uonuma Factory and Technical Center in Uonuma City. At the two factories and two centers, the company machines components, designs and produces automated machinery, as well as develops and manufactures direct-to-consumer products. There are 43 employees at the company.
Component fabrication and
solid automated equipment production
Since their inception, the company has specialized in small-lot production of palm-sized components, handling not only their main area of automated machinery components, but also plastic mold components and optical equipment components. In addition to the stainless steel used in automated machinery components, the company is known for their machining knowledge of ceramic and cemented carbide. Because machining and grinding ceramics creates fine dust particles that could adversely affect fabrication equipment, Niigata Precision keeps ceramic and cemented carbide fabrication at the main factory, while automated machinery component machining is handled at the Uonuma Factory. Also, at the Technical Center, which was opened next to the Uonuma Factory in 2016, the company has established a component prototyping framework to meet customer machining demands.
Design and production of automated machinery has finally gotten on track in recent years, becoming an area of growth. In 2018, the Mechatronics Center was opened as a base specializing in automated machinery.
The automated machinery components designed here are machined at the Uonuma Factory, then returned to the Center for assembly and inspection before being shipped out around the country and the globe.
President Teruhiko Hoshi says, "Although there are many companies who are involved in both design and assembly, there are very few who handle the entire process, including design, machining, and assembly.
You could say that's what we're known for." The company's current focus is automated machinery several meters in size for manufacturing automobile connectors, which inserts terminals, conducts quality checks, and packages the products, while transporting the components. Because automated machinery generally handles a single product, the design team develops a new product according to customer demands each time an order is received.
President Hoshi says, "In addition to our main component machining and integrated automated machinery production, we are dedicated to taking on new domains."
Differentiation through
active equipment investment
Niigata Precision is known for working with materials that are difficult to machine, and their integrated production of automated machinery, and one thing that has helped distinguish them from other companies is active investment in high-precision machining equipment. For example, the electrical discharge machines used in machining plastic mold components use the Sodick ALN600G linear motor drive, high-speed, high-performance wire-cut EDM, the AP3L ultra-precision die-sinker EDM, and the K1BL NC ultra-fine small-hole drilling EDM, allowing them to handle microfabrication processes, such as for connector molds.
There are many mold manufacturers in Niigata Prefecture that handle large workpieces, but it is rare for any to specialize on microfabrication as Niigata Precision does. The company also possesses an oil-type wire-cut EDM that can process components with greater precision than water-type equipment.
The samples produced on the same machine ten years ago consist of two components machined separately and assembled, with a clearance of 2 μm on a side for each component. A spiral component smoothly slides out from a component that appears to be a simple cube. One could say that this is a good example for showcasing the company's technical prowess.
On the other hand, they have adopted machining equipment that is a bit over-engineered for their everyday work. This is thanks to Mitsuo Hoshi, the president until 2018 and the current president's father. Word from the top was that they wanted a linear motor drive MC, resulting in adopting the MC430L, Sodick's first linear motor drive mass-produced MC. Teruhiko, the current president who at the time managed the Manufacturing Department thinks back on that time, saying, "To be honest, the machinery was so good that I wondered how we could possibly use it in production." Niigata Precision also adopted a 5-axis control MC that they would have hardly any chance to use as they mainly machined components on 2 or 2.5 axes.
The ALN600G wire-cut EDM and K1BL NC ultra-fine small-hole drilling EDM
Samples and mold components produced on Sodick EDMs
Instant orders for replicas
submitted to JIMTOF
The equipment, which had at initially seemed to be superfluous, was first used when Teruhiko was appointed as the president in 2018. Several years prior, the company had announced their policy of "Challenging the Future," and began exhibiting samples made using their precision component machining techniques at trade shows. Visitors who stopped by their booth were captivated by the playful samples they saw on display, such as a portable shrine and Kinkaku-ji Temple that fit in the palm of one's hand, and mirrored balls.
Japanese swords were what caused direct-to-consumer business to flourish. However, they were a mere 50 mm long and not particularly sophisticated.
"It was thanks to Sodick that we were able to begin seriously making replicas of Japanese swords," says President Hoshi.
The 29th Japan International Machine Tool Fair (JIMTOF) was held in November 2018. At the time, we asked a number of companies who use Sodick equipment to display machining samples at the Sodick JIMTOF booth, one of which was Niigata Precision.
Mr. Hoshi says, "Usually we would display our main product line of automated machinery components.
But JIMTOF is a massive trade show, and upon hearing the names of some of the other companies Sodick contacted, we realized we couldn't display something we made just for fun. After some debate, when showing a Japanese sword sample, Sodick said 'That'll be fine! Let's go with that,' giving us the push we needed.
There was only one month until the exhibition so we had no choice but to do it."
A team of mainly two people, consisting of Atsushi Eguchi, director and manager of the Future Project Department and President Hoshi began a trial and error process in Japanese sword sample making.
The only Japanese swords in existence are several hundred years old. Naturally, there were no blueprints or 3D models needed for machining. Despite this, based on documentation and photos that showed the blade length, width, and curve, they created 3D models in CAD/CAM which they then reduced in size. The team used the Sodick UH430L linear motor drive MC, succeeding in machining a sample from a sheet of steel hardened to over 55 HRC. In order to create a sample that was as close to the real thing as possible, they made many unique adjustments to the machining pathway and workpiece holding method, resulting in something that can be called true artisanal techniques.
When they were displayed at JIMTOF, visitors from overseas wanted to buy them immediately. The company then began building a production framework at a rapid pace. They decided to make the replicas at 1/6 to 1/7 the actual size in consideration of the Firearms and Swords Control Law, which regulates the possession of bladed items. Because the original Japanese swords come in many different lengths, the actual scale is represented in the replicas. The lineup currently consists of six different swords, including the Heshikiri Hasebe, the beloved sword of Oda Nobunaga and a national treasure, and the Ichigo Hitofuri, a famous sword from the collection of Toyotomi Hideyoshi. The latest addition to the collection is the famous Tsurumaru Kuninaga sword made by Kuninaga during the Heian period, which not only includes a faithful recreation of the blade itself, but also the sword fittings including the guard, pattern, and scabbard.
Replicas of Japanese swords made using the UH430L
From Japanese swords to medical scalpels
The full features of the UH430L were utilized in machining replica swords. Director Eguchi, who was in charge of machining, praises the Sodick MC, saying, "General ball screw drive MCs tend to experience errors when used for a long period of time because the grease runs out, resulting in friction, however, a linear motor drive system, which generates thrust thanks to the attraction and repulsion of magnets, is a non-contact method, making it reliable because it doesn't cause such problems. Also, the specs of this device are useful in adding hamon patterning to the sword and in situations where attention to surface quality is important."
Making replicas of Japanese swords not only developed a new domain in direct-to-consumer products, but it also led to developing medical scalpels. A medical equipment trading company asked that since Niigata Precision can make Japanese swords, could they make them scalpels? The company obtained medical device manufacturing certification in October 2020 and began manufacturing scalpels for ear surgery.
Niigata Precision also offers original scalpels with exquisitely designed pattern engraved on the handle, and they are considering growing medical equipment manufacturing as the next core business along with component and automated machinery production.
Sodick linear motor drive MCs including the UH430L
Evaluating the stance on
creating new models one after the another
Although Niigata Precision also uses MCs manufactured by other companies, they have only used Sodick EDMs since the company was founded. With all of those years as a user, they trust Sodick completely. President Hoshi says, "We've dealt with Sodick as a company for a long time, and they offer good precision and quick support.
We have no intention of using electrical discharge machines from other companies." Sodick has a branch in Sanjo City, Niigata, and quick access to support lends peace of mind. The company also evaluates Sodick for creating new models one after another. Mr. Hoshi says, "From a user's point of view, I have mixed feelings on the release of a new product right after I buy something (laughs). Even so, it's good to see improved performance when a new model comes out a few years later."
On the other hand, there are issues with electrical discharge machining. Namely, the differences between workers in die-sinking electrical discharge machining. Normally in die-sinking electrical discharge machining, centering is achieved by pressing the electrode against the probe, however, in machining the delicate mold components that Niigata Precision handles, this process is difficult because of the extremely slim electrodes, and workers must rely on intuition in placing them. Mr. Hoshi says, "Sodick MCs have setup support features that use sensor technology.
It would be good if this could be applied to die-sinker EDMs."
Problems have also arisen due to the many pieces of high-precision machining equipment on site. One problem is extended time for warm-up operation, and the other is the influence of the ambient temperature. The higher the precision of the equipment, the longer the warm-up time until machining can begin, which results in wasted waiting time.
Also, it is necessary to strictly control the temperature in the factory in order to reduce the effects of ambient temperature. Mr. Hoshi relates, "I understand that higher precision results in a longer warm-up time, and it's a given that it takes time to make good things. It would be great to make improvements to accomplish this in a shorter period of time." The factory temperature is kept to 23°C currently, and offsetting the effects near the machines would make it possible to set a wider temperature range. This shows that the manufacturer is also being counted on to make adjustments in order to save on electricity spending and help reduce the impact on the environment.
A fusion of high-precision machining
and artisanal techniques
As a company continuing to Challenge the Future, Niigata Precision aims to offer components with greater added value. Mr, Hoshi says, "Until a few years ago, we were forced to compete with Chinese manufacturers on price, but lately in China, fabrication costs are on an upward trend, so the difference from Japan is shrinking. With this in mind, I believe there will be a greater need again for high-quality products."
In such a situation, equipment investment becomes ever more important. For example, EDM is used in the fabrication of minute mold components, however, there is the possibility of increasing need for direct carving via MC. Not having the right equipment at the right time can lead to missed opportunities. Mr. Hoshi says, "I'm gradually beginning to understand the idea of adopting over-engineered equipment from the last generation."
With the introduction of more high-precision machining equipment, the issue becomes training the staff who use it. Niigata Precision is focused on creating venues for young and veteran staff to casually talk. Recently, young staff are much more likely to submissively accept what they are taught, making it difficult to ask questions such as "Wouldn't this be more efficient?" With this in mind, the company has a monthly session where young staffers gather together to discuss issues at sites. The agenda and proceedings are left up to these young employees as a way to help train their ability to question things and improve their communication skills.
In order to beat overseas manufacturers who are mainly focused in China and continue on with "Made in Japan" products, it is important to improve each and every individual member of the staff in addition to using high-precision machining equipment. Mr. Hoshi says, "By continuing the training of young employees, I think the company is gradually improving. In the end, it's people who use the machines."
Focusing on training young staff with the essential skills for high-precision machining equipment
Teruhiko Hoshi, Representative Director, President
Niigata Precision Co., Ltd.
- Address
- 1684-1 Nakajoki, Tokamachi City, Niigata 949-8617 Japan
TEL:025-752-6306
- Representative
- Teruhiko Hoshi, Representative Director, President
- Established
- 1996
- Number of Employees
- 43
- URL
- http://www.np1.co.jp/
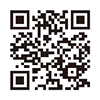