Core Technology 07 Straight-Hydraulic Mold Clamping System
Meaning to close the mold
Injection molding is a manufacturing process for producing products by injecting melted plastic materials into a mold then cooling it to solidify it.
Clamping force is necessary to hold the mold together against the pressure of the melted materials being injected to keep resin from spilling out.
Conventional toggle type mold clamping systems open and close using a link mechanism with a movable platens bushing fitted onto four tie-bars, therefore position accuracy and trajectory repeatability were inconsistent, resulting in the inability to fully appreciate the precision of the molds.
In other words, even if molds are created with extraordinary precision, damage or bumps in the product could occur due to slippage or gaps created during the opening and/or closing of the mold.
Introducing the Direct Pressure Mold Clamping System
Sodick has continued its pursuit for a precision straight mold clamping system.
We place importance on the idea of the clamping force to be consistent with what the mold was designed for in order to release the product from the mold without adding any stress.
To improve mold positioning and trajectory repeatability and successfully minimize damage to the mold, Sodick’s proprietary Direct Pressure Mold Clamping System uses four technologies: long-span support, LM guide platen support, a central ball screw driving mechanism and a tie-bar holdless platen.
Molding machines using the Direct Pressure Mold Clamping System or V-LINE® System provide the following benefits:
- Molding stability with minimal inconsistencies.
- Improvement in production planning flexibility since minimal machine deviance allows production under the same molding conditions when the same mold is mounted on different molding machines.
- Improvements after a mold modification can be easily ascertained allowing users to accumulate modification know-how.
- Molds last longer.
- Highly reliable numerical control makes learning molding techniques and creating molding conditions easier.
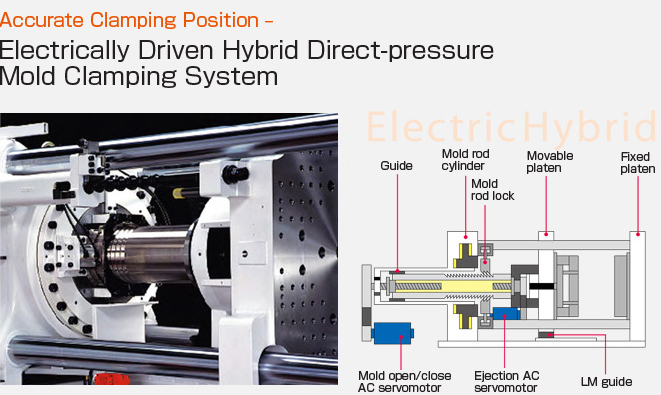