The Art of Monodzukuri (Techniques for Creating Things)
Principles of Electrical Discharge Machining and Non-Wearable Electrode Circuits
Molds and dies are indispensable for manufacturing.
Molds and dies are the general terms referring to the metal patterns used in the mass production of products.
Products are made using a vast array of molds and dies including stamping dies, forging dies, casting dies, die casting dies, and plastic molds.
Molds and dies are a necessary part of manufacturing. They can be used to manufacture the parts used in cars, smartphones, and other common objects at high quality and high efficiency.
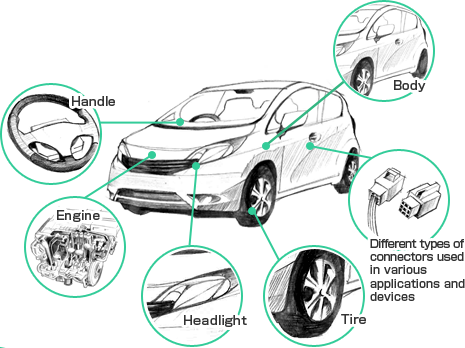
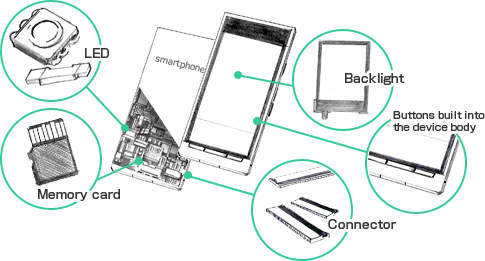
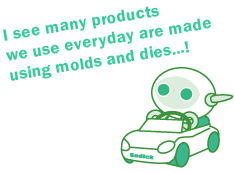
What kinds of metal materials are used to make dies?
Usually, metal materials that are harder even
than standard iron are used.
A variety of materials are used in molds and dies depending on the product being made. Hard metals that are harder than the standard tempered cast iron as well as cemented carbide materials and other materials that are even harder still are one of the examples.
Cemented carbide is a type of metal known as having the greatest hardness of any material next to diamond. It is often used in molds and dies due to the hardness and robust character.
Electrical discharge machine is the machine capable to process these hard metal materials using controlled movements in increments of one micrometer.
For comparison,
1 μm is equal to
1/1000 mm
Electrical discharge machining technology is used to make molds and dies using a very strong cemented carbide material
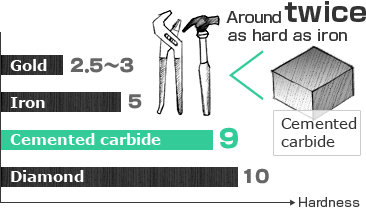
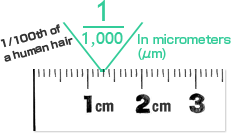

What is Electrical Discharge Machining Technology?
It is the technology used to machine extremely! hard metal materials with soft metal materials just as sharp cutting blades using electrical energy.
Electrical discharge machining involves two metal objects positioned opposite each other that are submerged in a liquid such as water or oil. An electrical spark is ignited between the objects to generate the heat used to melt and shape the metal. When a spark is ignited in the liquid, the metal struck by the spark is melted. The melted portion is then cooled by the liquid at rapid speed and dispersed. The melted part is whisked away, leaving behind dimpled pockets on the surface of the metal, resembling the craters on moon! This process of machining metals by melting, cooling, and scattering metal particles repeatedly using intermittent bursts of electrical discharges is known as electrical discharge machining.
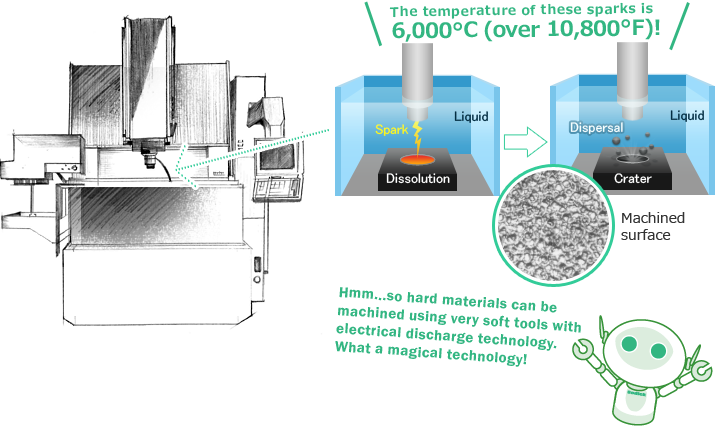
Electrical Discharge Machines are sometimes called as EDMs.
(Abbreviated to "EDM.")
About Electrical Discharge Machining Technology and
Non-Wearable Electrode Circuits
In this section, we will introduce you on how electrical discharge machine technology processes. And we will explain about non-wearable electrode circuits that worked to advance this technology dramatically.
When and what kind of products need electrical discharge machining?
Let's take "bear plates", plates shaped like a bear for instance. First, we need to create a mold for the plate.
The metal we need to use for a mold is a hard metal. So it is very hard to process complex shape using standard techniques. Now electrical discharge machining is up to solve this problem.
To get started, first we make an electrode that is shaped as a bear. Then we apply a voltage between the bear-shaped electrode and the electrode formed from the hard metal. A spark is ignited from this discharge of electricity, which strikes the metal and these sparks are used to accurately shape the bear electrode into the desired pattern.
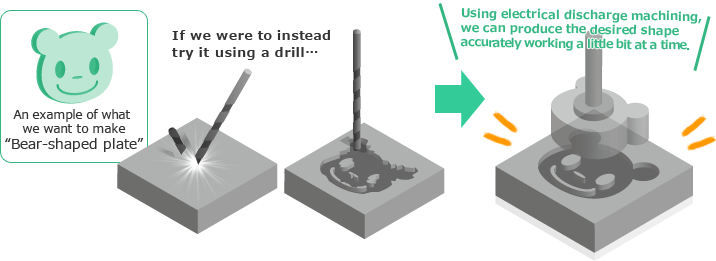
Trying it with a drill pressed directly against the metal just causes the drill bit to snap off as the metal is just too hard.
Even if we were able to get the drill bit to punch out a shape, it would not be accurate enough to use as a die.
Now, just the right shape with smooth, clean edges is ready! This die will let efficiently produce a great number of "bear plates" shaped just like this die.
How can we machine the material into the shape we want?
We use 2 main methods: die sinker electrical discharge machining and wire electrical discharge machining.
With die sinker electrical discharge machining:
Anywhere from 1,000 to 100,000 sparks are generated on and off between the electrode and the metal per second. These sparks strike the surface of the metal, carving out the shape of the electrode. Note that the electrode does not make any contact with the metal block being machined during this process. This type of process is known as a contactless machining process.
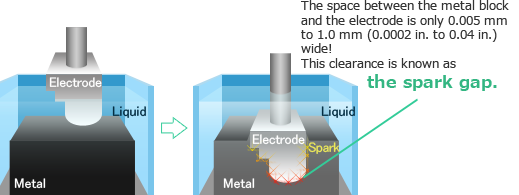
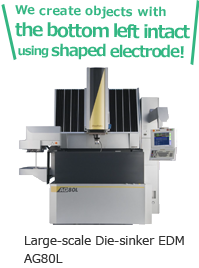
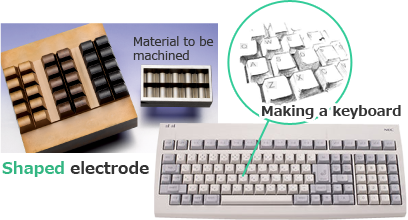
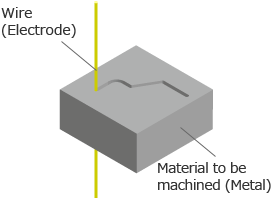

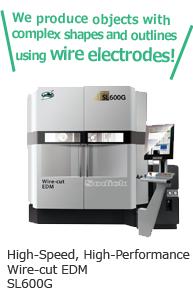
What is an electrode used for
die-sinker EDMs?
The electrodes used have a shape that is the mirror image of the object to be made. Usually, materials that can easily conduct electricity such as copper or graphite (the material used for graphite drawing sticks and lead pencils) are used. This material is a soft metal that can easily be processed into shapes using a standard drill.
In wire electrical discharge machining:
an extremely thin electrical wire is used as an electrode to cut through the metal material by melting the metal using the heat from the generated sparks.
As if by magic, it doesn't melt the electrode but the metal block is formed into the desired shape!
Won't the electrode also melt if you use sparks from electrical discharge to melt the metal?
Yes, the heat from the sparks will also cause the electrode to melt.
The electrodes used in die sinker electrical discharge machining are subject to damage caused by the sparks used in machining, which causes them to melt.
This damage is referred to as "wear."
Up until around 1964, there was only one major machining technique, which used punches. The machined object was completely punched out from the material all the way through the bottom, and the electrodes used experienced a lot of wear.
A number of researchers used trial and error using different electrode materials and a variety of circuit designs, working to try to figure out ways to reduce the amount of wear on the electrodes.
And then, they discovered something…
Revolutionary breakthrough in electrical
discharge machining technology
Invention of Non-Wearable
Electrode Circuitsin 1965
Finally! Mr. Toshihiko Furukawa, the founder of Sodick, invented a non-wearable electrode circuit that experiences no wear even during electrical discharge machining processes!!
This invention actually came about from a mistake.
One day, Mr. Furukawa accidentally mixed up the plus and minus for the electrode and object to be machined while working on his research. By connecting the plus and minus terminals in reverse, he discovered a rather unexpected phenomena in which holes were punched into the surface of the object being machined without any resulting damage to the electrode.
This invention was actually quite a rather unexpected discovery produced by a miracle. Development of the non-wearable electrode circuit advanced based on this advancement sparked a dramatic period of innovation in electrical discharge machining technology.
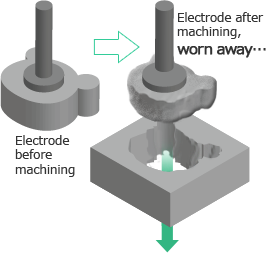
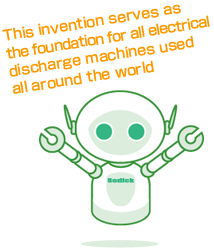
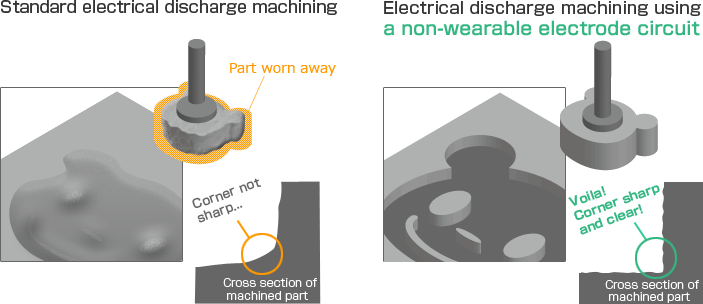
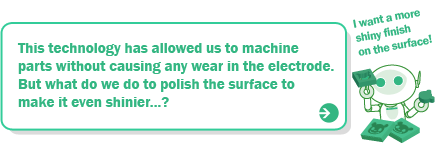
With no loss of electrode material,
sharp corners and an even more accurate shape closer to what we want to create can be produced.