Now able to machine parts without subjecting
the electrode to any wear.
The next improvement is
finding a way to easily polish side surfaces
to a smooth finish.
Electrodes of different sizes were used for each step to produce a glossy finish on the side surfaces
Electrical discharge machines at that time (around 1970) consisted of a positioning table operated manually that worked to position the workpiece and a machine head used to move the electrode from the top to the bottom to advance the electrical discharge process.
Because of this, we needed to prepare two additional electrodes other than the first and each electrode had to be slightly larger than the electrode before it in order to apply a smooth finish in the side directions using such machines. Electrodes would have been used for the second and third machining processes, respectively. The only way at the time to produce a clean, smooth finish on bottom and side surfaces was to use these electrodes, whereby you would use increasingly larger electrodes with gradually decreasing amounts of electrical discharge energy used in order of electrode size starting with the initial electrode.
It took a lot of work to produce these shaped electrodes that varied in size slightly. What's more, it was also extremely difficult to increase machining accuracy due to the need to switch out electrodes during each subsequent machining step after the first one.
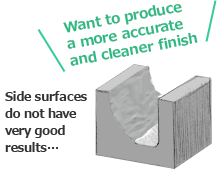

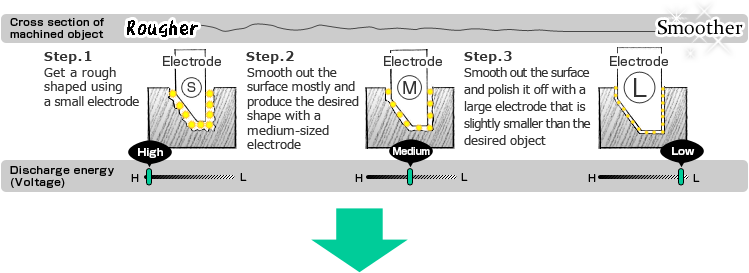
This method would eat up a lot of costs and money...
Isn't there a better way to complete
the finishing process using fewer electrodes?
We have developed
Loran technology
just for this purpose!
The Loran technology enabled to better polish the surfaces of machined parts to more accurately smooth out the roughness that caused so many problems previously.
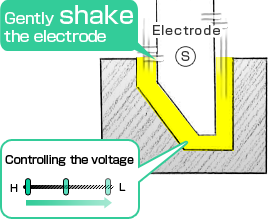
What is the Loran Technology?
The Loran technology is a type of method used for electrical discharge finishing that involves gently shaking the electrode.
Here, we will describe the Loran technology in details.
What changed with use of the Loran technology compared to traditional techniques?
With electrical discharge machining performed using sparks, the machined part is made to be slightly larger than the outline of the electrode. This size changes with the intensity of the spark. Also the machining speed increases as the strength of the spark increases. However, the amount of roughness on the surface of the machined part also increases. To fix this issue, we needed to gradually increase the size of the electrode used to match the size of the desired part. Then we applied finishing to the machined surfaces and then use a smaller spark in contrast.
With that method, unfortunately, we needed to use several different electrodes... The costs and amount of time it took went up the smoother and cleaner we wanted the finish to be.
We sat thinking about whether we could produce a nicer, cleaner finish on the surfaces of machined parts using fewer electrodes. It was then we realized that to produce a nicer finish on side surfaces, we could simply make the dimensions on the shaped electrode along the side surface directions bigger. W noticed it should be able to produce the same smooth surface by merely moving the initial electrode back and forth in the horizontal direction without needing to increase the width along the side direction.
This idea led us to development of a device that could shake the electrode located below the head in the EDM in the horizontal direction (oscillation machine) .
Loran machining is a production technique that allows us to control the direction of movement and intensity of the oscillation to the desired values using numerical control. The technique can be used to produce a clean, smooth finish more accurately in all directions using fewer electrodes.
With the Loran movement, we can machine the side surfaces of the part accurately and smoothly using smaller electrodes by gradually decreasing the width of the clearance between the electrode and part being machined and gradually lowering the intensity of the electrical discharge energy used.
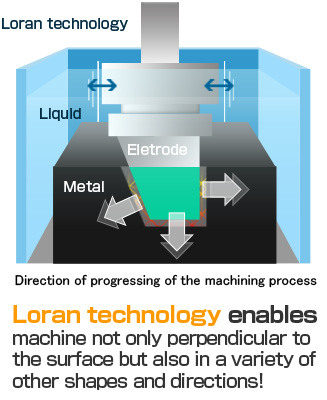
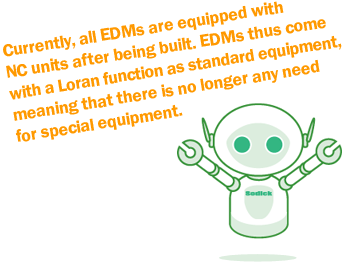
What kind of shapes can you create using the Loran technology?
Until the Loran technology was formed, EDMs weren't very practical machines at all. Since non-wearable electrode circuits and the Loran technology have been developed, we can now machine parts in a wide variety of shapes.
Synchronized Loran technology
A rich array of various detailed settings can be used for the Loran pattern that is used as the basic pattern designed to enable handling of electrodes with different shapes.
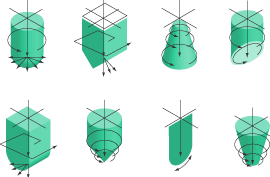
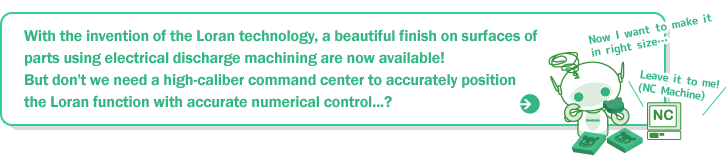