Idling Fluid Surface Function
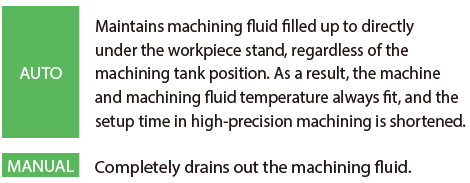
Auto and Manual can be switched by one click on a gadget screen.
For Automation
High degree of freedom allows flexible operation
The articulated robot performs workpiece transport.
To prevent workpiece corrosion, which can be an issue mainly with water machining fluids, adequate drying and spraying of anti-corrosion oils, etc., is necessary. Features of system upgrades with articulated robots include a high degree of freedom in layout for each device, a drying station (air blow process), and the ability to automate access to the anti-corrosion spraying device.
The tooling system for wire-cut EDM performs selection depending on the workpiece shape or utilization, enabling flexible setup work and continuity between models, to improve productivity in the machining process overall.
Automated workpiece replacement
Large-capacity and space-saving
Compared with an articulated robot, many of the machines have a large loading capacity and can transport various types of workpieces even in a reduced space.
In wire discharge machining, when a large number of workpieces are being processed, continuous machining is possible by setting as large a number of workpieces as possible beforehand on the machining table. However, in this case the NC program that is created becomes complicated, and the workpiece setup also requires a long work time.
Automation of workpiece transport enables optimum workpiece space utilization, a drastic shortening of setup time on the machine, and improved machine operating rate.
Flat chuck
When compared with other machine tools, wire-cut EDMs require a special setup.
Use of tooling in response to each utilization enables flexible setup operations and greatly improves productivity in wire-cut EDMs.
For Automation
Use of a scheduler enables integrated management of entire system operations including machines and robots, ensuring continuous execution.
By combining with a CAD/CAM system that creates NC programs automatically, operation is greatly simplified, making it suitable for a wide range of system configurations.
A scheduler that supports automation without cumbersome operations by collecting and managing design information (positioning, machining programs, position coordinates, workpiece information, etc.) and on-site information (measurement values by external units, information from stockers).
Can be linked to DiproWin, enabling workpiece positioning operations or performing scheduling right after creating a program.
2D CAD/CAM system
developed and manufactured by
Sodick
A CAD/CAM system for wire-cut EDM, developed to shorten lead times at mold design and manufacturing sites, and capable of providing solutions in a wide range of situations.
Collects the operating states of each machine, performs batch management and analysis from a remote location, and supports improvement in productivity.
For Automation
As it is a non-contact type that dispenses with the need for ball screws, degradation of mechanical precision traceable to wear on the ball screws and other effects does not occur throughout the machine life (10 years or more), maintaining the initial mechanical precision semi-permanently with no need for maintenance.
High reproducibility and long-term stability, two characteristics of linear motor drives, are the most important factors demanded of machine tools in automation of manufacturing.
Sodick’s wire-cut EDM is equipped with a linear motor drive on all four XYUV axes as standard.
With disconnection point wiring and automatic restart, provides powerful support for the long-time automatic operation. Boasts high connection rates, even mid-air or underwater.
Contact sensing function using a wire electrode line.
Corrects coordinates automatically by performing workpiece origin placement and measurement of workpiece tilting.
Auto and Manual can be switched by one click on a gadget screen.
Since a mechanism that the fluid surface height automatically performs tracking according to the Z-axis is adopted, there is no need to manually change the fluid surface height according to the thickness of the workpiece, enabling efficient setup. In addition, automation can easily be adopted as well.
A core processing device with a simple composition keeps the workpiece from dropping after removal from machining and automatically retrieves it. Core processing can be automated even on precision workpieces, without slipping out of position.
Machine temperature changes are continually recorded for real-time diagnosis of effects on machining. In addition, changes in wire remaining amount and machining fluid resistivity are monitored to indicate the time for replacement of consumable parts.
Maintenance functions reduce defect rates and improve traceability.
Precision thermal displacement correction system based on sensing of temperatures in each machine part.
Eliminates the need for prior collection of data, enabling long-time operation regardless of the season or environment.
For Automation
Theme I
Point 1
This system automates the machining on the ultra-precision AL400Pmodel using the large capacity ERC80. Multiple varieties of workpiece pallets are prepared in response to machining size, and dynamic machining is performed with two AL400P units.
Point 2
Centering around a single robot, multiple machines are arranged in a orientation of point symmetry. Runs the same NC program on twoAL400P units.
Point 3
Uses a simple presetter made of ceramic to set workpieces and perform precision checks, as off-line setups.
Point 4
For long-time continuous machining, stable automatic wiring is essential. The AL series “FJ-AWT” is a high performance automatic wiring device that performs stable wiring of fine wires on workpieces held on pallets that are in low floating or submerged states.
Theme II
Point 1
For machining of large-volume workpieces, even if machining per workpiece can be performed in a short period of time, setup time is required every time when replacing the workpiece. The use of robots to automate workpiece transport, mounting, and removal greatly shortens setup time, leading to labor saving and improved machine operating rates.
Point 2
After machining, the workpiece is dipped in oil to prevent rusting and then stored on a prepared work shelf.
Point 3
Machined workpieces are taken out by a robot, and machining fluid is removed in a drying station (air blow process).
Point 4
Software system constantly monitoring program execution enables real-time checking of machining progress even from a remote location.
Theme III
Point 1
The articulated robot is suitable for transport of lightweight workpieces with a high degree of freedom. These characteristics are utilized in simultaneous machining with an indexing rotation axis, to automate workpiece transport to the rotation axis, mounting and removal, and finishing.
Point 2
In oil machining, in principle there is no appearance of rust or corrosion of cemented carbide materials. In blade shapes that cannot be subjected to polishing, final finishing is enabled. Oil machining fluid itself has superior oxidation resistance and demonstrates stable machining performance even in the long-time continuous machining.
Point 3
Measurement on the machine using a touch probe dramatically shrinks machine differences that can easily arise during setup, enabling precision machining.
Point 4
The AP seriesis an ultra-precision model that demonstrates high performance in all environments. A linear motor drive system is adopted to achieve a gantry structure, an arm suspended structure, and high speed and high response, dramatically minimizing machine displacement and machine friction due to mass transfer.