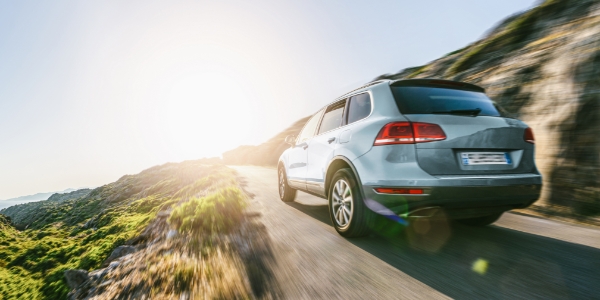
Why Metal 3D Printers in the Automotive Industry?
- Shortening the development period
- Weight reduction of parts
- Quality and Production Cycle Improvement
Now that the environment of the automotive industry is changing dramatically, such as the development of EV cars and advanced driving support systems, the advantages produced by metallic 3D printers are being utilized at various stages, including development, manufacturing, and after-sales service.
development period
Shortening the development period
Two major features of manufacturing with metal 3D printers:
(1) Aspects can be molded in an integrated structure
(2) Aspects that utilize digital tools so that processes are streamlined
Can be molded into an integrated structure
One of the major features of metallic 3D printer molding, the molding in an integrated structure, contributes greatly to process consolidation.
By utilizing metal 3D printers, you can greatly reduce the number of machining processes while having a high degree of flexibility in design. This means that secondary/post processing is minimal, leading to shorter delivery time of prototypes and molds.
Manufacturing with Digital Twin*
A metal 3D printer, which digitally executes a series of processes from modeling to production, can reproduce information from the real world (information on the modeled object) in a digital space using simulations using analysis software and other tools.
Simulation-based trial-and-error can be used to shorten the development period.
- *Digital twin: A technology that reproduces information from the real world in a digital space and builds a system that works together.
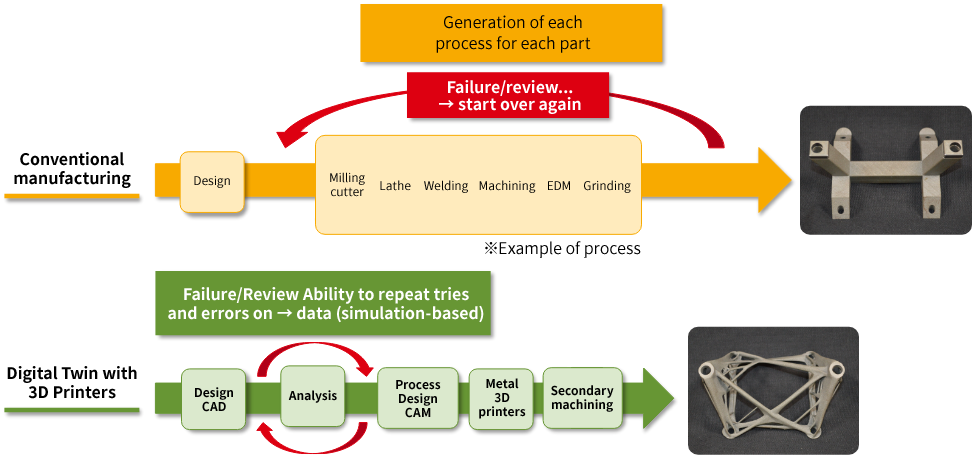
weight saving
Achievement of lightweight parts
The weight of parts plays a major role in drivability.
With the accelerated development of EVs and other vehicles, weight reduction is an important issue for automobiles, which have many parts.
Metal 3D printers have many methods that can reduce the weight of parts.
Reducing the number of parts through integrated structure modeling
Integrated structure modeling can achieve weight reduction by reducing the number of parts and bolts connecting parts.
Reduction in weight and improvement in strength through the use of design optimization
Based on the specified conditions, advanced designs with lighter weight and improved strength can be derived on a simulation basis by utilizing "topology optimization" and "generative design" that can lead to design optimization.
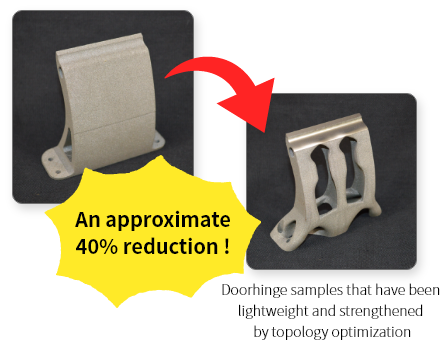
Weight reduction using lattice structure
A lattice is a complex shape that can only be produced by a metal 3D printer, consisting of a fine three-dimensional grid.
By reducing the volume with a lattice shape, weight reduction and material reduction are possible. Lattices can be used in any part shape to take advantage of the superiority of metal 3D printer modeling.
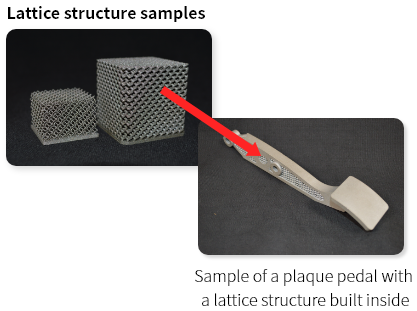
Increased productivity
Improved component productivity
with molds with built-in 3D coolant pipe
If it is molded with a metallic 3D printer,
The interior allows for complex 3D coolant pipe shapes.
In addition, automotive parts that require heat resistance are increasingly using aluminum, which is both lightweight and heat resistant, instead of resin products.
Die-casting molds made with metal 3D printers are also attracting attention for their ability to achieve stable molding quality with enhanced cooling effects by forming 3D cooling water channels internally.
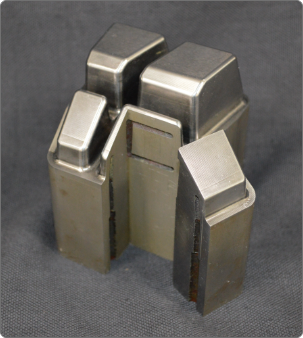
Die casting model
Built-in 3D coolant pipe inside the heat storage area
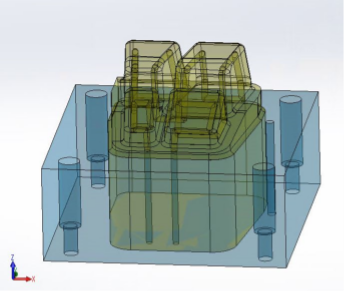
We can design finer 3D coolant pipes by shaping them in an integral form, which was not possible with conventional methods.
Reproduction
With data, reproduction is possible at any time.
As metallic 3D printers are digital manufacturing based on data, reproduction can be done at any time if data is available.
Long-term storage of repair parts and die parts is also eliminated.
sample
Automotive industry-related samples
You can check the details by clicking on the sample photo.