By developing and manufacturing all the elemental technologies represented by a linear motor, a discharge power supply, a NC device, a motion controller, and ceramics in-house with a development concept of "Advanced Smart Pulse & Advanced Smart Linear", the AL series demonstrates the highest level of performance.
AL series products
P Type : High Precision, Full cover Best surface roughness Rz 0.34 µm (Carbon Carbite)
G Type : Full cover Included/Not included Best surface roughness Rz 0.34 µm (Carbon Carbite)
Q Type : Front manual up/down machining tank Best surface roughness Rz 1.5 µm (Steel)
About AL series
Advanced Smart Linear
Advanced Smart Linear maintains high speed and high accuracy semi-permanently.
Sodick's linear motor and control unit realized accurate positioning, high response and high tracking in wire-cut EDMs.
This highly rigid machine structure and optimal machining performance demonstrates the advantages of this drive system to the utmost.
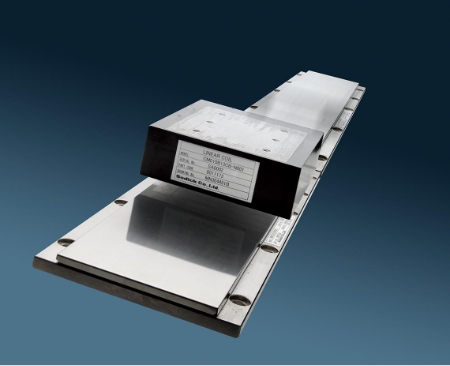
4 axes are equipped with linear motors
Sodick's linear motor with energy saving design
Eco machine contributes to waste reduction without periodic replacement
Advanced Smart Pulse
Advanced Smart Pulse integrated with Sodick's electric discharge technology gained over many years, optimally controls all electric discharge machining.
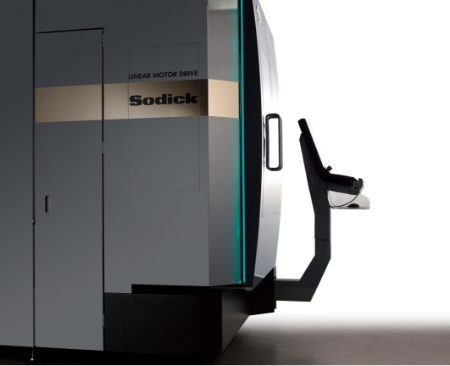
Barrel-free Effect Control II
TMP Control II
DSF (Dynamic Shape First)
Digital-PIKA-W : High frequency digital finishing circuit
P/G Type : Best surface roughness Rz 0.34 µm, Cemented Carbide
Q Type : Best surface roughness Rz 1.5 µm , Steel
SPW CNC Power Supply Unit
19 inch horizontal touch panel in pursuit of workability and operability
- Equipped with 2D automatic programming support function "Heart NC"
- Energy saving function scheduled operation
- Machining condition search function (Equipped with Easy Parameter Adjustment, EPA)
- High voltage circuit (Optional for difficult to machine material)
- Workpiece measurement function (Contact sensing)
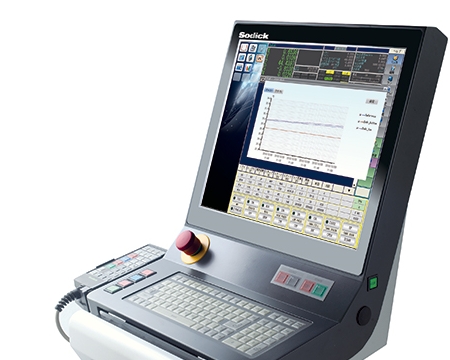
Features
Highly rigid machine structure
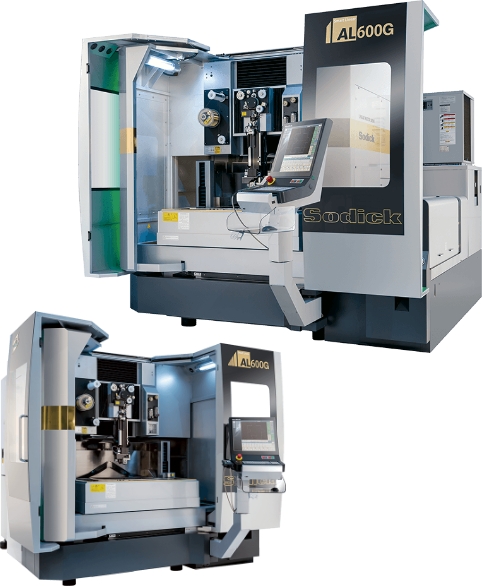
Repeats the simulation using CAE analysis to design the optimal load applied during operation
Realized weight savings and increased rigidity by optimizing the rib configuration
Flat surfaces were carefully levelled by scraping work on the key locations
Simulation analysis of the installation environment assuming the machining site of the EDM is reflected in the design.
Ceramics are used abundantly in the wire running system to ensure weight savings and rigidity
Insulated structure of wire running system and workpiece fixing portion
- Ceramic upper / lower guide arm
- Ceramic surface plate
- 4 workpiece stand ceramic base
- Pulley for wire tension parts
- Wire discharge winding rollers
Full cover
The door cover suppresses effects from changes in air flow and room temperatures
that change periodically
Door cover design with secured workability
Door cover provides a quiet and clean machining environment
AL400P/AL600P : Full cover CFRP door
AL400G/AL600G/AL800P/AL800G : Full cover
Automatic wire threading unit Fixed Jet AWT (Type A)
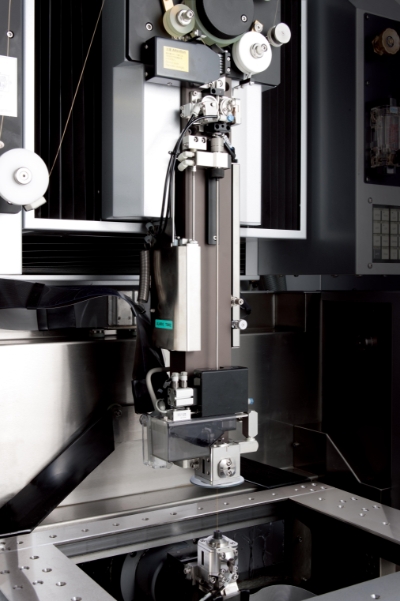
Wire annealing function
The Joule's heat in the conducting wire improves the straightness of the wire.
Excellent in straightness, and the jet-less connection is recommended even for wire threading under water.
Wire tip processing
Melts the tip of the wire by heat to a shape which makes it easier to connect.
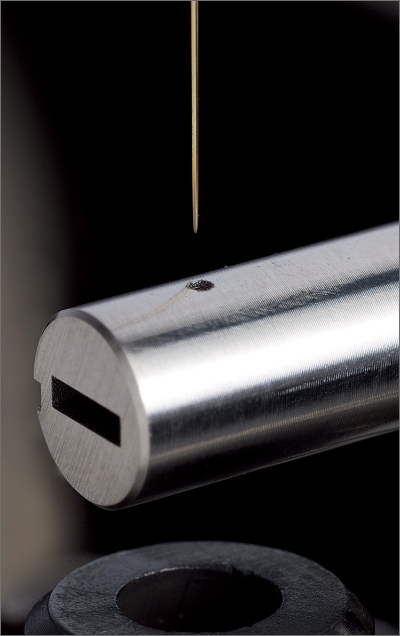
Automatic wire threading
Non-submerged threading + In-kerf threading
Dice cleaning function
The air type (AWT dice guides) and flush type (up/down wire guides) cleaning function maintains stable operation and machining accuracy.
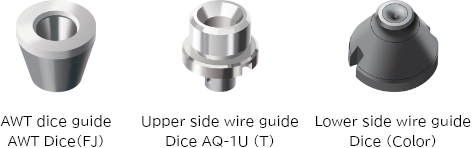
Machining Performance
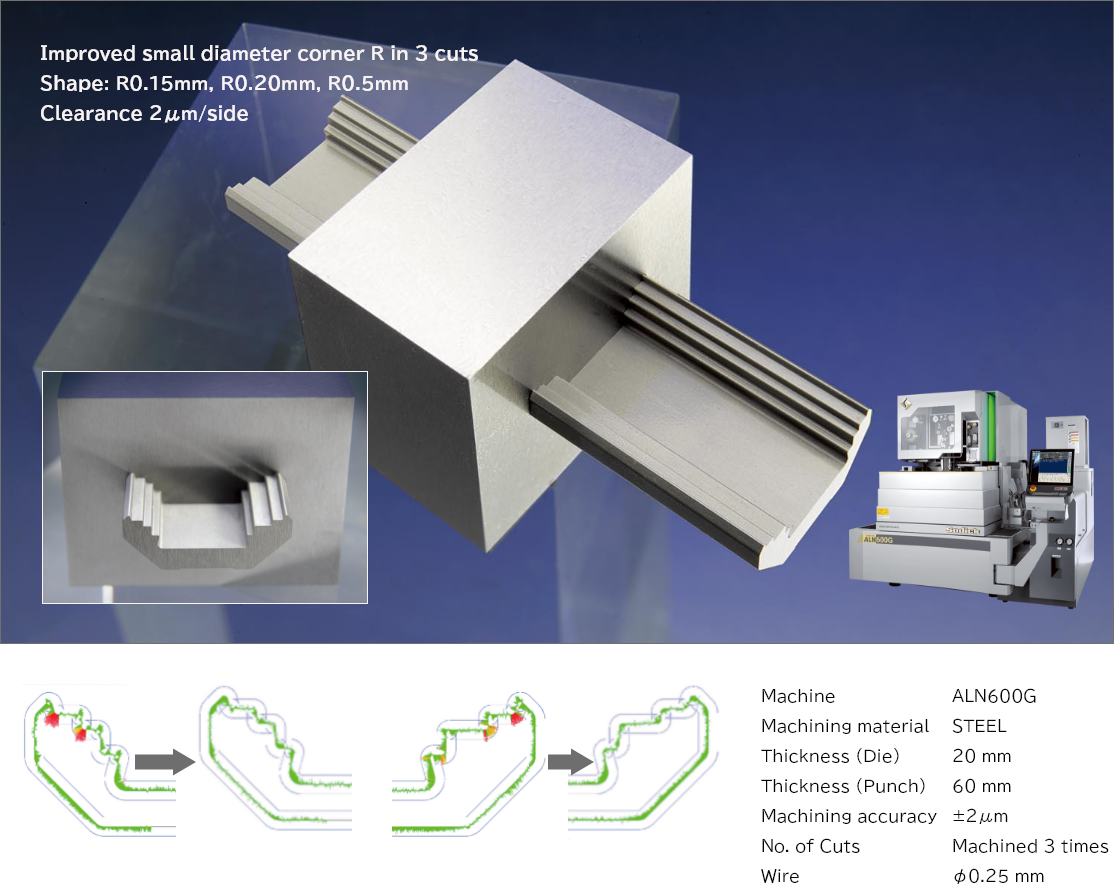
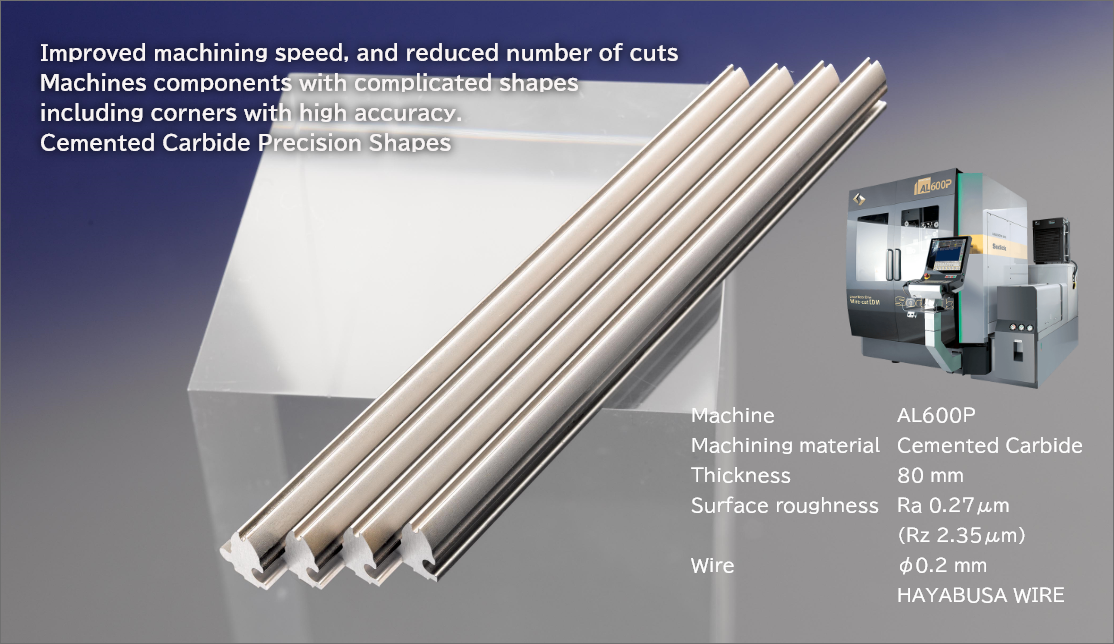

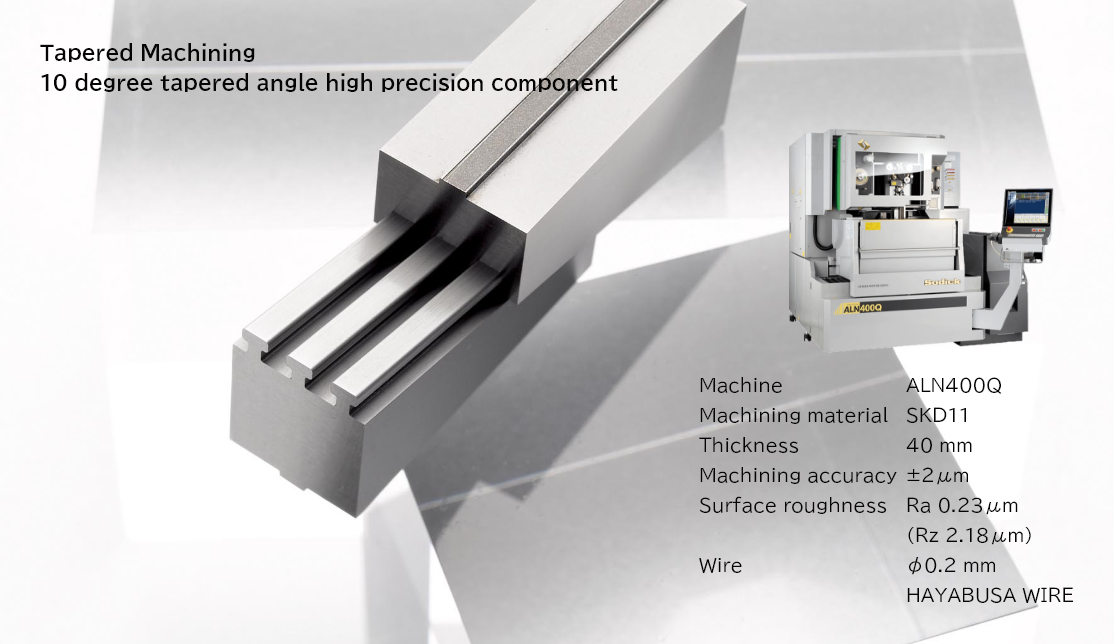
Taper Flex NEO (Option)
This is a tool and built-in software for adjusting and measuring tapered angels for high accuracy taper machining.
There are two types of tool thicknesses, 30mm/60mm.
Use the tool with the thickness closest to the workpiece.
Use "Taper Flex Neo 30t" for taper machining of 10 degrees or more.
■ Taper Flex Neo 30t
■ Taper Flex Neo 60t
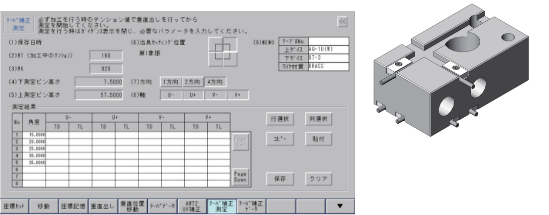
Taper Flex 45-NEO (Option)
This option comes with an upper/lower nozzle added to the Taper Flex Neo 30t as a set.
The combination of the nozzle and dice enable machining of taper angles up to 45 degrees.
* Separate R dice for wide angle tapers are required.
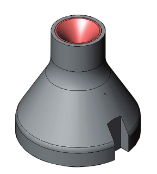
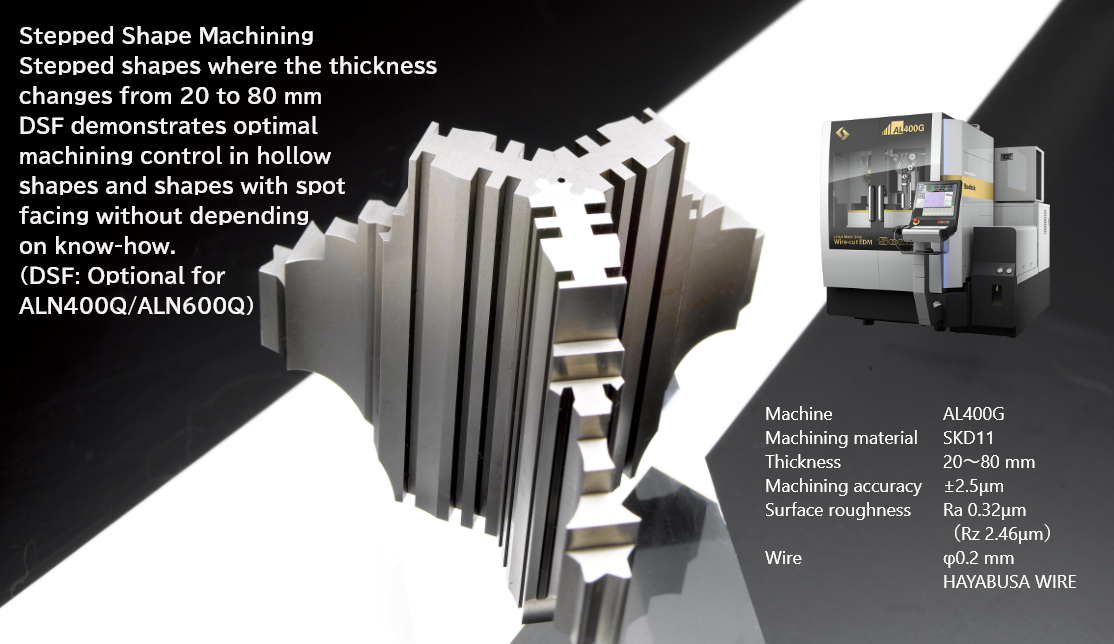
■ High precision machining in stepped shapes where the thickness changes from 20 to 80 mm
■ Monitors the flushing conditions and machining conditions in the 1st cut, and controls the machining conditions to the optimum to prevent wire breakage
Pitch Accuracy
Pitch accuracy ±1 µm
- Maximum distance
between pitches - X direction 360 mm,
Y direction 260 mm - Machine
- AL600P
- Machining material
- SKD11
- Workpiece size
- 550 x 350 x 20 mm
- Wire
- φ 0.25 mm Tsubame Plus Wire
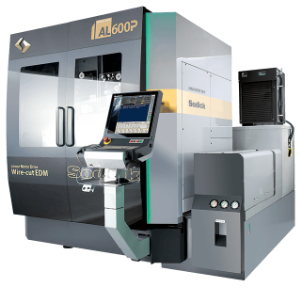
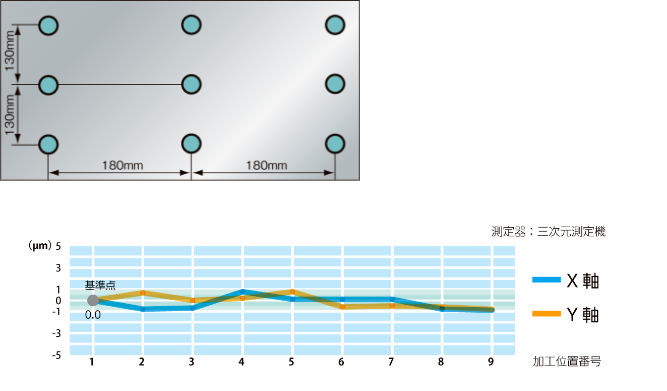
Pitch accuracy ±1.5µm
- Maximum distance
between pitches - X direction 700 mm,
Y direction 500 mm - Machine
- AL800P
- Machining material
- SLD
- Workpiece size
- 800 x 650 x 20 mm
- Wire
- φ 0.25 mm Tsubame Plus Wire
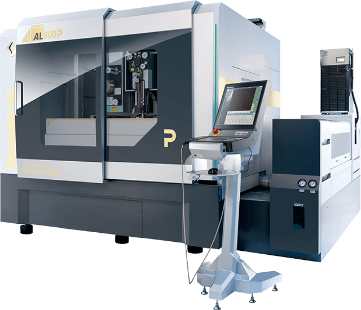
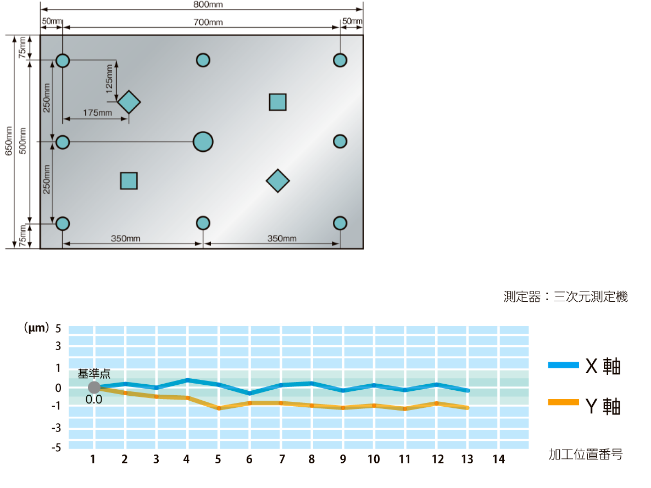
Pitch accuracy ±2.5µm
Die machining can be performed in 4 locations in each of the 2 plates.
All the punch parts can be fitted at the same time in these 2 stacked plates.
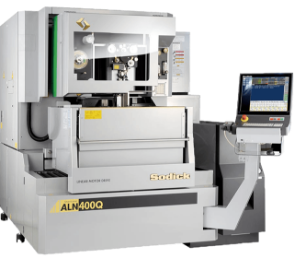
- Machine
- ALN400Q
- Machining material
- STEEL
- Thickness
- 40 mm
- Machining accuracy
- ± 2 µm
- Pitch Accuracy
- ± 2.5 µm
- Surface roughness (Die)
- Ra 0.21µm (Rz 2.12 µm)
- Surface roughness (Punch)
- Ra 0.32 µm (Rz 2.68 µm)
- Wire
- φ 0.2 mm HAYABUSA WIRE
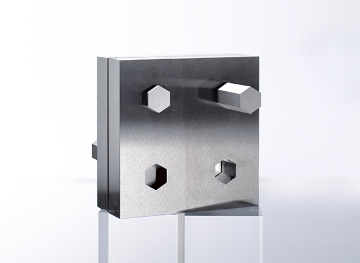
Roundness
Roundness accuracy 0.76µm
- Machine
- AL600P
- Machining material
- PD613 hardened
- Thickness
- 30 mm
- Wire
- φ 0.2 mm Tsubame Plus Wire
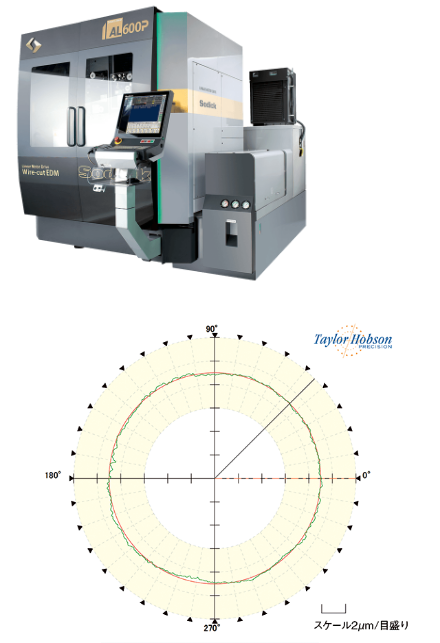
Roundness accuracy 1.86µm
- Machine
- ALN400Q
- Machining material
- STEEL
- Thickness
- 40 mm
- Wire
- φ 0.2 mm HAYABUSA WIRE
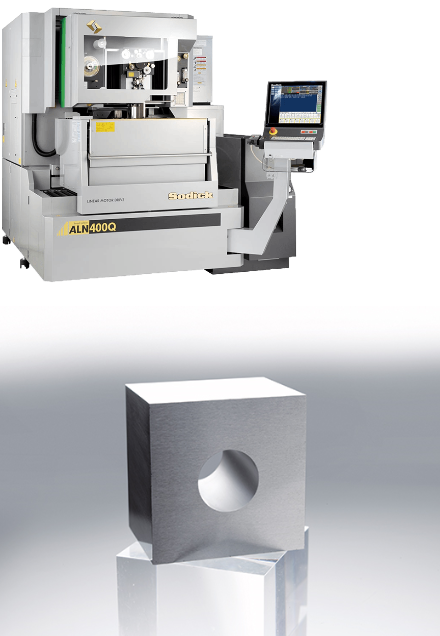
AL800P promotion movie
Operability
2D Automatic Programming Support Function
Heart NC
2D automatic programming support function which can create machining shapes
Programs for different T/B shapes, involute gears, coreless, shapes, and free form curves can be created
■ Example of Heart NC operation screen
Gear shapes can be created easily just by entering the number of teeth and modules.
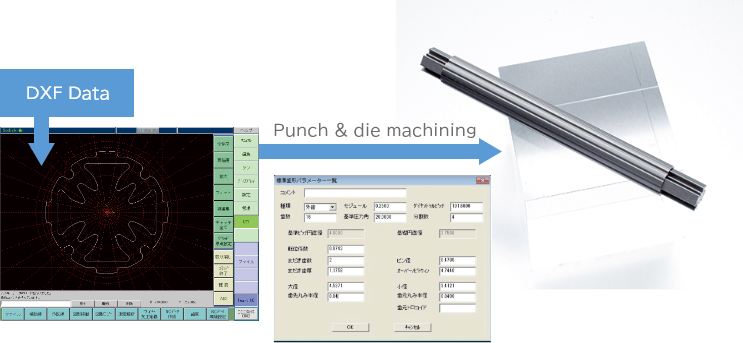
Machining Conditions Search Function
The number of cuts can be specified, balance adjustment and offset adjustment of machining accuracy and speed are possible
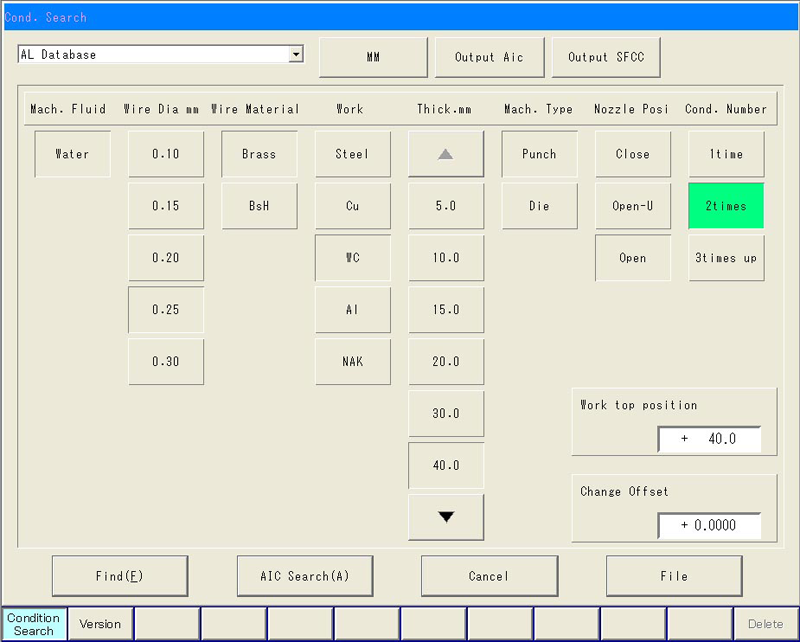
Approach mark reduction
Reduces approach mark reduction
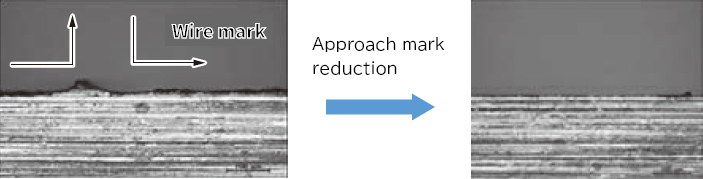
Reduces Setup Time
Idling Liquid Level Function
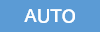
Regardless of the position of the machining liquid tank, the liquid level is maintained in a state reaching directly below the work stand. This allows the machining fluid temperature to be constantly matched with the machine, shortening the setup time in high-precision machining.
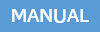
Complete drainage of working fluid
Can be switched with one click on the gadget screen.
Z-axis Linked Liquid Level Control
Since a mechanism to automatically track the liquid level according to the Z-axis has been adopted, setup can be implemented efficiently without manually changing the liquid level depending on the thickness of the workpiece. This function can also support automation easily.
Automatic Workpiece Inclination Correction
Measures the inclination by contact sensing on the plane in the X and Y axis directions.
Automatically measures the inclination of the workpiece, which enables the setting of the coordinates according to the inclination.
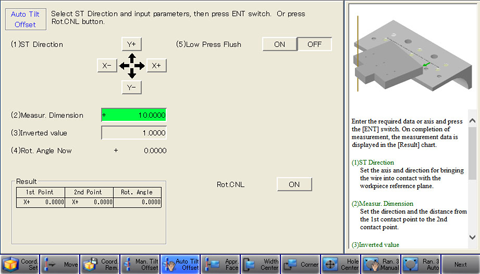
Workpiece Plane Correction
This function is for correcting the workpiece plane so that the upper surface of the workpiece is perpendicular to the wire.
A reference probe is attached, and automatically measures the inclination at any 3 points on the upper surface of the workpiece to correct the plane.
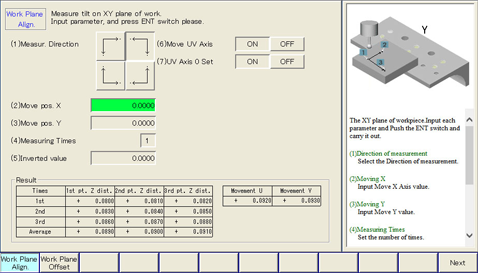
Workpiece sensing with probe
Workpiece sensing with image processing measurement
LED Signal Function
Displays the operating condition of the machine in color.
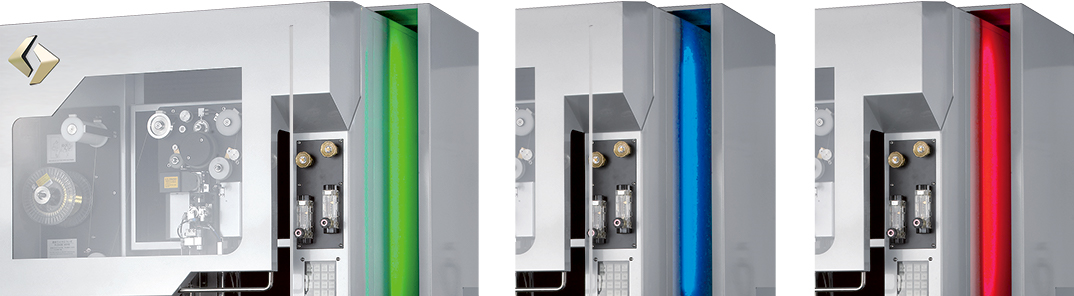
Option
Rust-less
This system suppresses rust, corrosion, and staining of workpieces during machining.
The combined use of the electrical interaction and chemical interaction demonstrates effectiveness on both steel and cemented carbide materials.
The photo shows a comparison when Rust-less is used / Rust-less is not used in each material.
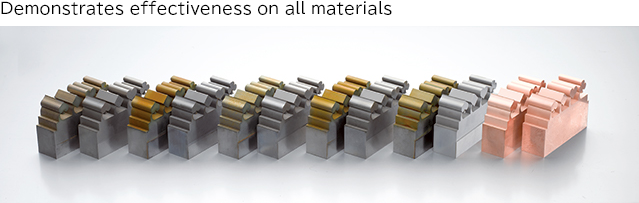
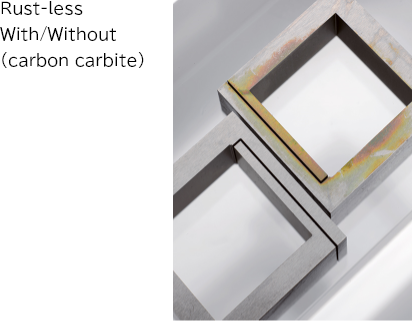
Core processing equipment S3CORE (Score)
Device that collects cores automatically.
Machining material: Corresponds to ferromagnetic workpiece material such as steel material.
Machining form: Machining with upper and lower guide in close contact
Equipment parts : Equipment installation to upper guide, core receiving pad, collecting box