Sodick's Core Technology
Features
One Step Further
Fixed Jet AWTAutomatic Wire Threading Unit
- Wire is automatically threaded into the start hole
- Supports long time continuous machining and unmanned machining
- Improves automatic wire threading performance regardless of being in the air or submerged
- Excellent straightness improves the automatic wire threading performance of very thick workpieces
- Improves the automatic wire threading performance even in workpiece shapes where the guide cannot approach the pilot hole
- Anneal length is longer than that of conventional machines, supporting machining of higher plate thickness
- Corresponds to the disconnection of wiring
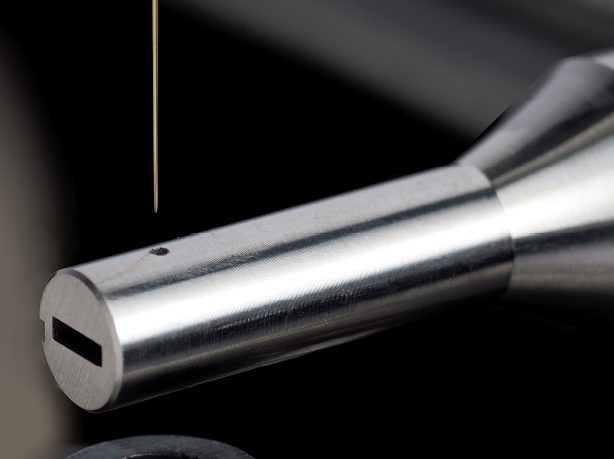
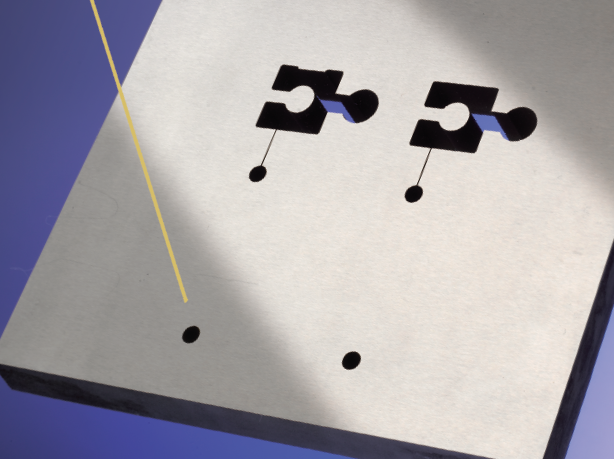
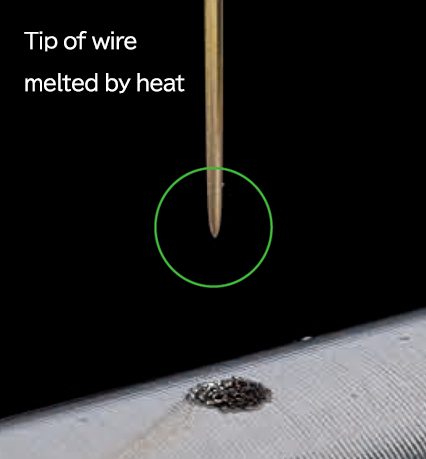
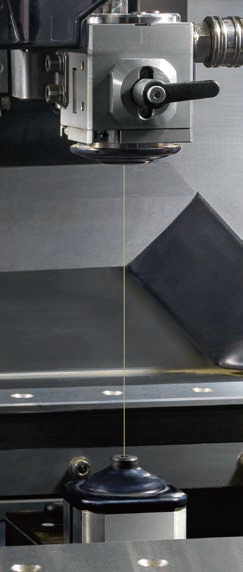
OptionFixed Jet AWT (Type VT)
Jet / Jetless automatic judgment
- Depending on the situation, the system automatically determines whether the jet assisting the automatic connection is ON or OFF.
The wiring operation is carried out using the optimal method.
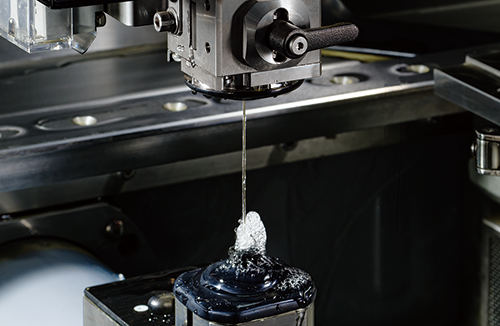
One-touch removable nozzle base
- The upper and lower guides and nozzles can be attached and detached with a special tool in one touch.
This eliminates the need for troublesome screw removal and facilitates maintenance.
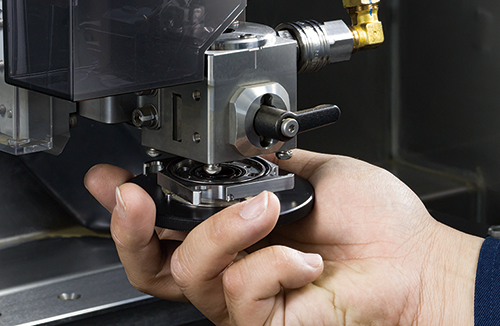
Optimum control of machining fluidEnergy-saving Pump System
Approximately 70% of the electric energy used in wire-cut EDM is consumed in the dielectric treatment system. With this in mind, a machining fluid control circuit has been installed as standard equipment to reduce the pump drive energy required for processing dielectric by inverter-controlling the flushing flow rate during machining.
This enables approximately 20% reduction of power consumption, including during standby, compared to the conventional models. (* Compared to our model case)
Comparison of power consumption
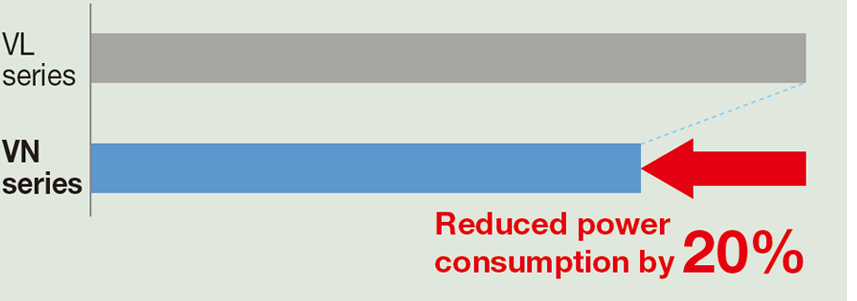
Example of model case machining
Octagonal punch shape width across flats 15 mm
- Machine
- VN400Q / VL400Q
- Workpiece material
- SKD11
- Plate thickness
- 40 mm
- Wire
- φ 0.25 mm
(TSUBAME PLUS WIRE)
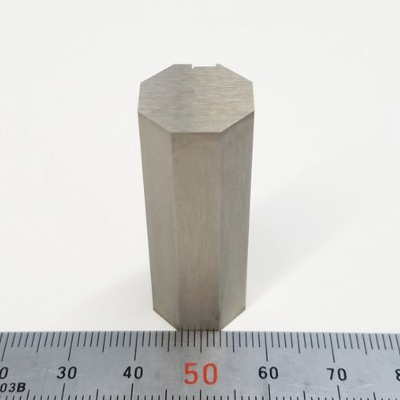
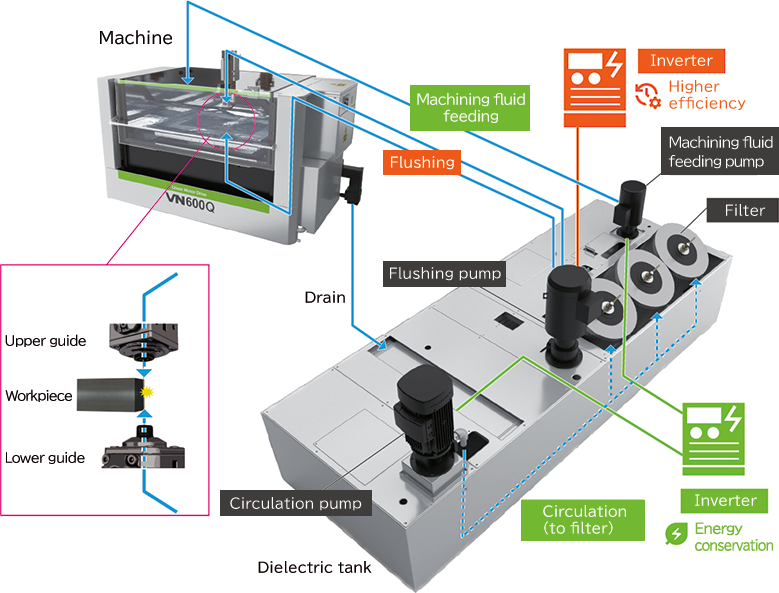
OptionPrecise Thermal Displacement Correction (TH COM)
Versatile from high-precision environments to rough temperature environments.
Accuracy changes due to disturbances, such as seasonal fluctuations and room temperature fluctuations by factory air conditioning ON/OFF, are reduced without data collection to minimize downtime.
Long-time stable machining is realized.
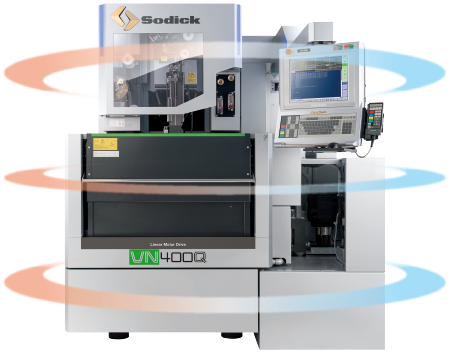
Improved accessibility to the machining area
- X-axis table movement and Y-axis column movement improve workability, such as parallel positioning of the workpiece in front of the machining tank
- The bobbin is easily replaced, and the position of the operation panel is optimized
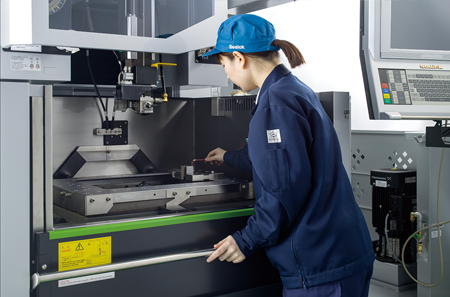
- Since the upper surface of the machining tank door is lowered by approximately 60 mm from the upper surface of the work stand, close proximity to the work stand is possible when moving in and out of the workpiece using a hand lift
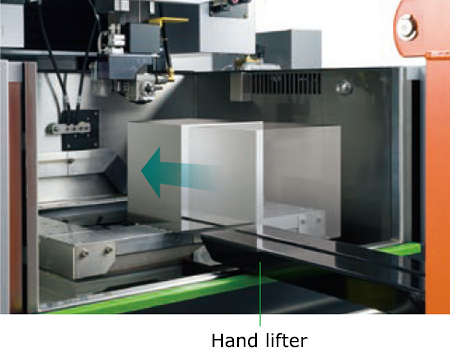
Slide plate cleaning
- Prevents adhesion of sludge on slide plate
- Maintains stable high precision machining
- Contributes to reduction of maintenance time
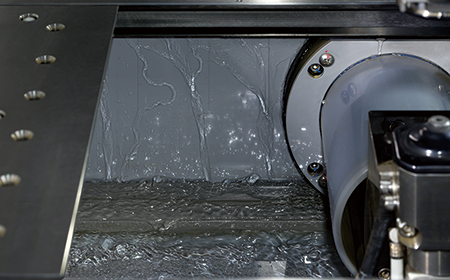
Triple filter
- Filters which filter the machining fluid and collect sludge
- The frequency of replacement is reduced by increasing the number of filters to three, enabling long-term continuous machining
- Maintains the freshwater tank clean by improving the filtration capacity
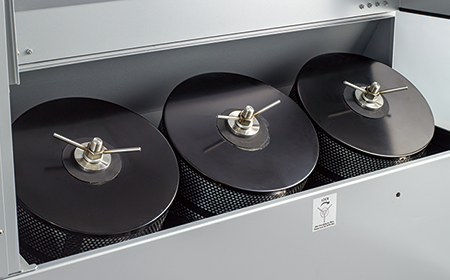
2D Automatic Programming Support Function “Heart NC”
- Equipped with two-dimensional automatic program creation function to create machining shapes as standard
- Programs, such as varying top and bottom shapes, involute gears, coreless shapes, and free form curves can be created
- Data can be read in DXF format
- Reads data created by other CAD/CAM in DXF format, and outputs a machining program
Example of program production
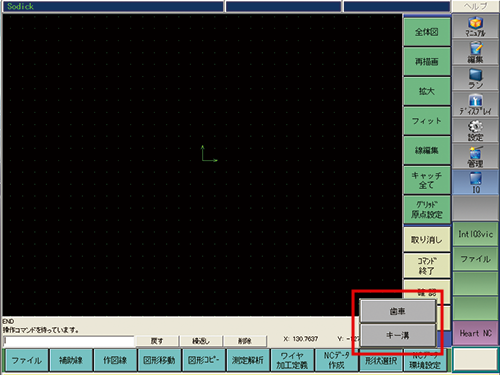
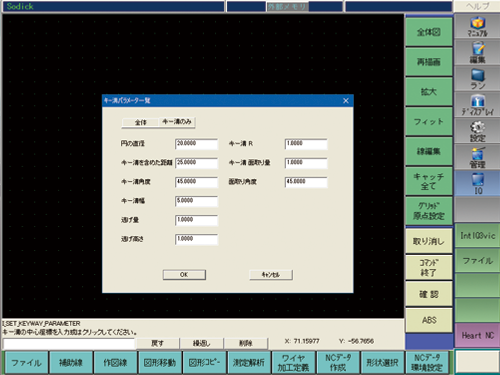
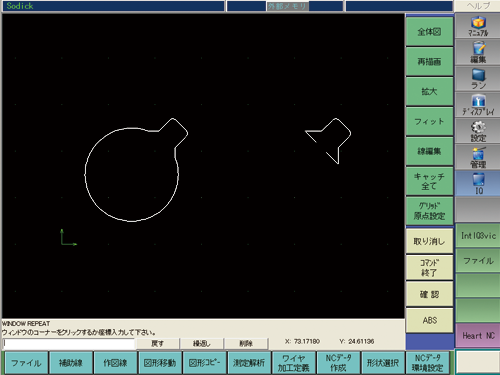
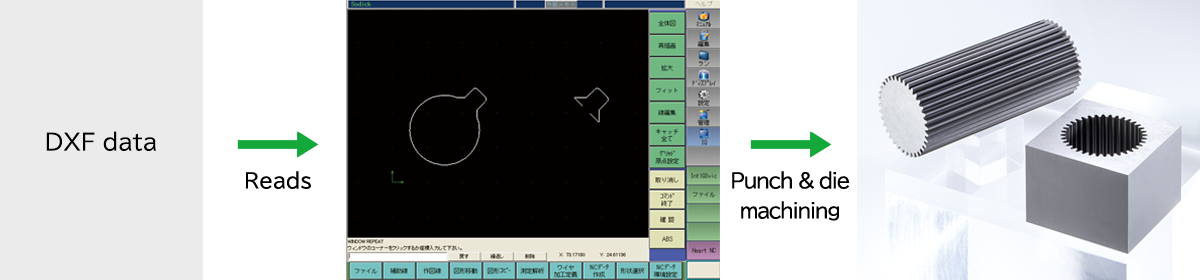
Samples
Higher-grade standard performance
Two times machining operation 2-sheet lamination
Key grooving
- Machine
- VN400Q
- Workpiece material
- SUS304
- Plate thickness
- 35mm × 2枚
- Surface roughness
- Ra 1.264μm (Rz 8.335μm)
- Wire
- φ 0.20mm (TSUBAME HQ WIRE)
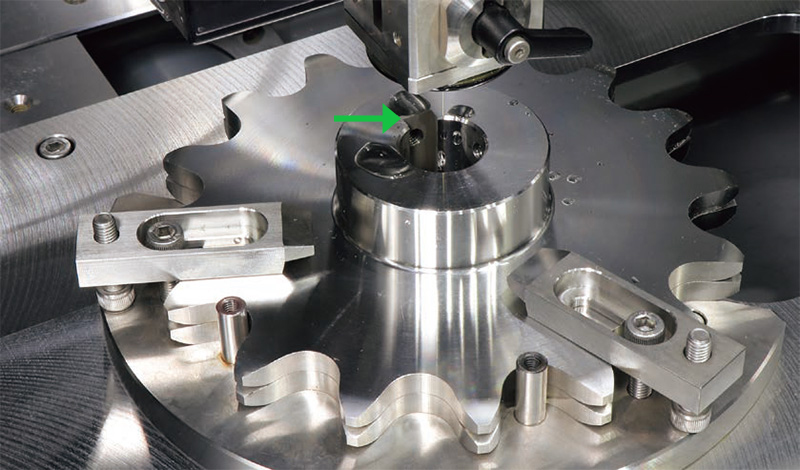
Taper 3° 4-axis machining (Top and bottom are different shapes)
High-grade open shape taper machining
- Machine
- VN600Q
- Workpiece material
- SKD11
- Plate thickness
- 100mm
- Surface roughness
- Ra 0.39μm (Rz 3.58μm)
- Wire
- φ 0.20mm (TSUBAME PLUS WIRE)
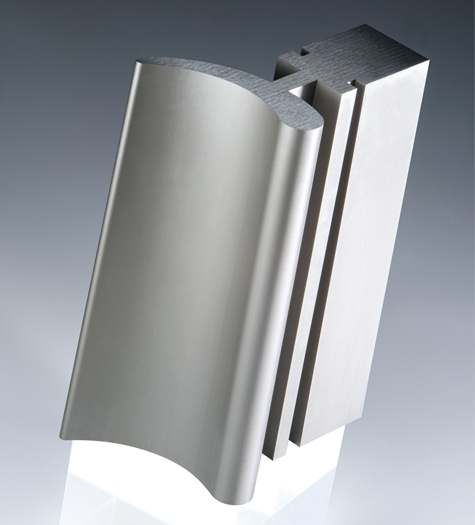
Machining accuracy ±5μm
Gear shape punch & die machining
- Machine
- VN600Q
- Workpiece material
- SKD11
- Plate thickness
- 70mm (Punch)
30 mm (Die) - Surface roughness
- Ra 0.38μm (Rz 3.02μm) (Punch)
Ra 0.34μm (Rz 2.13μm) (Die) - Wire
- φ 0.20mm (TSUBAME PLUS WIRE)
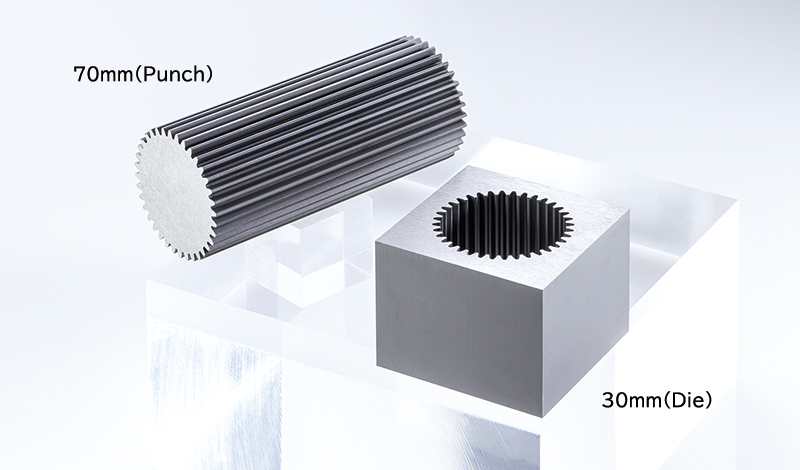
High plate thickness taper 10°
High-grade fitting slide machining
- Machine
- VN600Q
- Workpiece material
- SKD11
- Plate thickness
- 100mm
- Surface roughness
- Ra 0.38μm (Rz 2.95μm)
- Wire
- φ 0.25mm (TSUBAME PLUS WIRE)
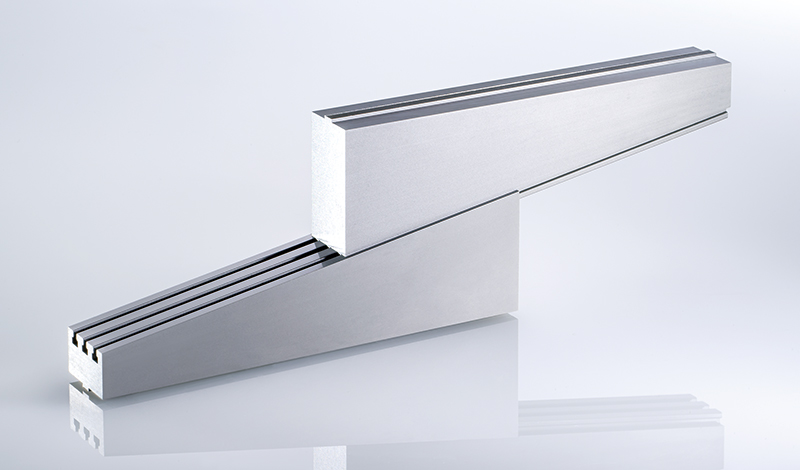
Open machining gear shape
Double floating gear shape machining
- Machine
- VN400Q
- Workpiece material
- NAK80
- Plate thickness
- 50mm (Counterbore Top: 5 mm, Bottom: 10 mm)
- Surface roughness
- Ra 0.40μm (Rz 3.15μm)
- Wire
- φ 0.25mm (TSUBAME PLUS WIRE)
Improvement of open machining
Upgraded liquid processing performance of the machining dielectric nozzle improves floating machining speed by 5% to 15% *
*Comparison with VL Series-based on our designated environment
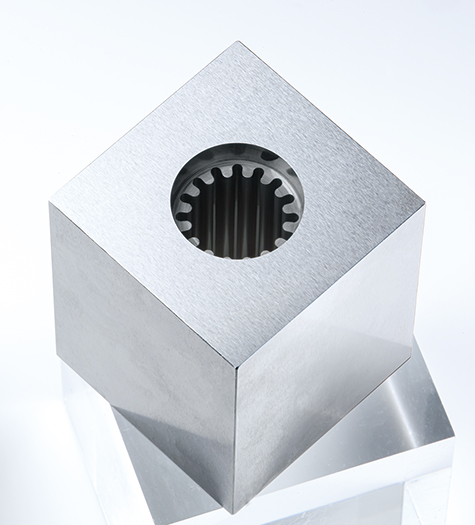
* The machining data in this catalogue is based on machining environment and measurement standards that have been specified by Sodick.
* The surface roughness unit Rz is used based on JIS B0601:2001 and ISO4287:1997/ISO1302:2002.