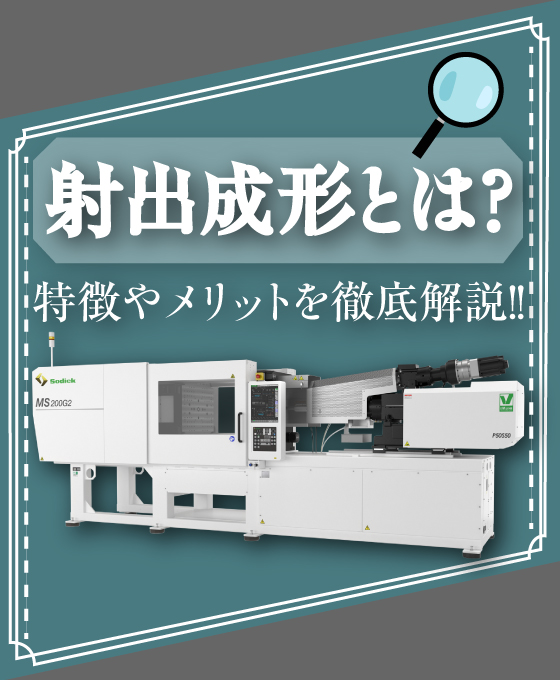
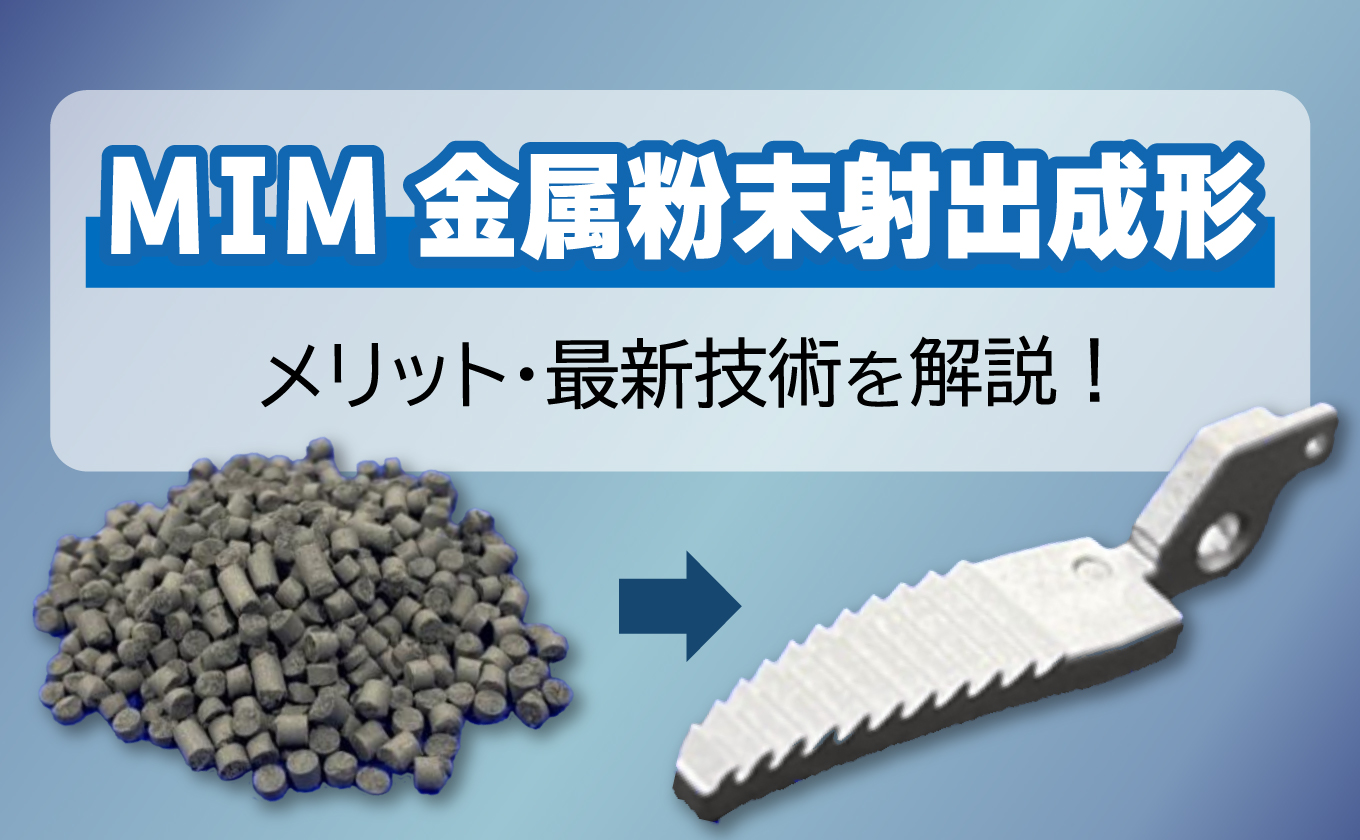

読了まで7分
こんにちは、SurVibes編集部です!
今回は、MIM(金属粉末射出成形)について解説します。
MIMの仕組みやメリットだけでなく、MIMが持つ技術的課題や、それを解決するために開発された新技術についても解説いたしますので、ぜひ最後までご覧ください。
目次
MIMとは
MIM(Metal Injection Molding)とは、射出成形と粉末冶金法を組み合わせた製造技術であり、金属粉末射出成形とも呼ばれます。
粉末冶金法
原料の金属粉末を金型に入れて圧縮することで成形し、焼結炉で焼き固めることで、金属部品を製造する製造技術です。
射出成形と言えば、一般的には樹脂材料を用いたプラスチック製品の成形を思い浮かべる方が多いかもしれませんが、MIMは樹脂材料の代わりに金属粉末とバインダ(結合剤)を混ぜ合わせた材料を用いた射出成形です。
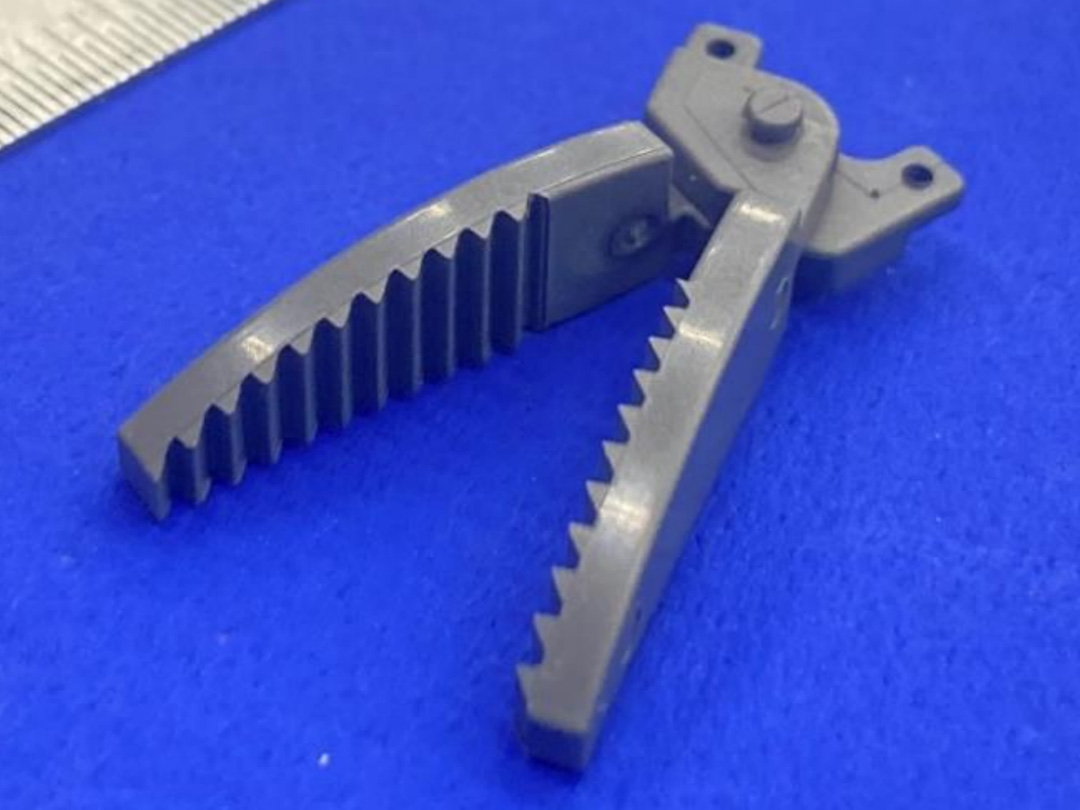
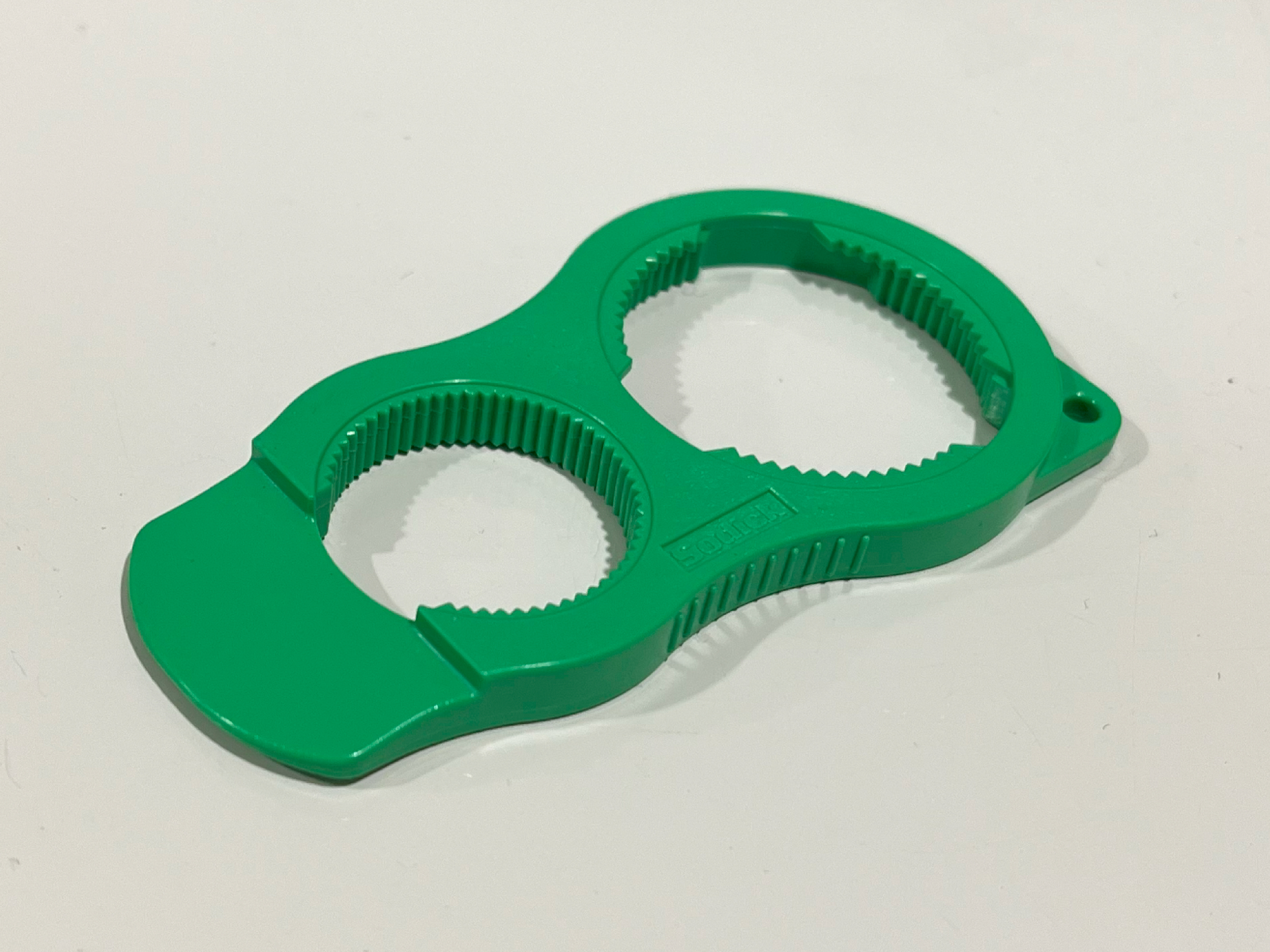
MIM自体は古くからある技術ではありますが、利用できる金属粉末の種類拡充など、技術の進歩により、さまざまな分野で活用されるようになってきており、特に大量生産が求められるような小型金属部品の製造現場で活用されています。
MIMに使用される粉末の例 | 利用用途 |
低合金: Fe-Ni-C, Fe-Cr-C, SCM415 | 一般機械、自動車部品 |
ステンレス鋼: SUS304, SUS316, SUS630, SUS440 | 耐食性部品 |
工具鋼: SKD, SKH | 高硬度、工具部品 |
耐熱鋼: Ni-Cr合金, SCH21, S-590 | エンジン部品 |
磁性材料: 純鉄, Fe-Si, パーマロイ, パーメンジュール | プリンター部品、磁気遮蔽 |
低膨張合金: コバール, アンバー | 光通信、ガラス封着部品 |
チタン合金: Ti, Ti-6Al-4V | 時計、眼鏡部品 |
その他: タングステン合金, 超硬合金 | ヒートシンク、振動子 |
MIMの工程
ここからは、MIMの工程を解説します。
フィードストックの製造
金属粉末と有機バインダ(結合剤)を均一に混ぜ合わせ、ペレタイザーでペレット状にします。
この工程で作られる材料をフィードストックと呼びます。
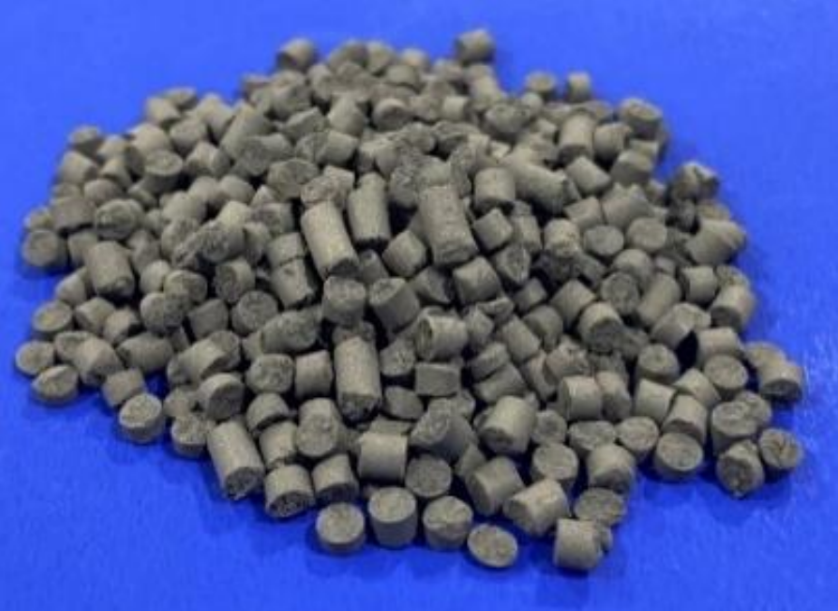
射出成形
射出成形機を使って、材料を金型内に射出し、金属と有機バインダが混ざった状態の成形体(グリーンパーツ)を成形します。
この工程は、一般的な樹脂材料の射出成形とほとんど同じです。
一般的な射出成形プロセスについては、以下の記事で解説しています。
脱脂・焼結
有機バインダの種類に合わせて、適切な方法で成形体からバインダを取り除きます(脱脂)。
脱脂方法には加熱脱脂・溶媒脱脂・触媒脱脂などいくつかの種類があります。
その後、1000℃以上の高温化で焼き固めることで、最終的な金属製品を得ることができます。
この際、バインダが抜けた分の隙間が埋まることで製品が収縮しますので、収縮率を考慮した金型設計が求められます。
収縮率はバインダの組成や添加量等によっても異なりますが、10%以上収縮することが一般的です。
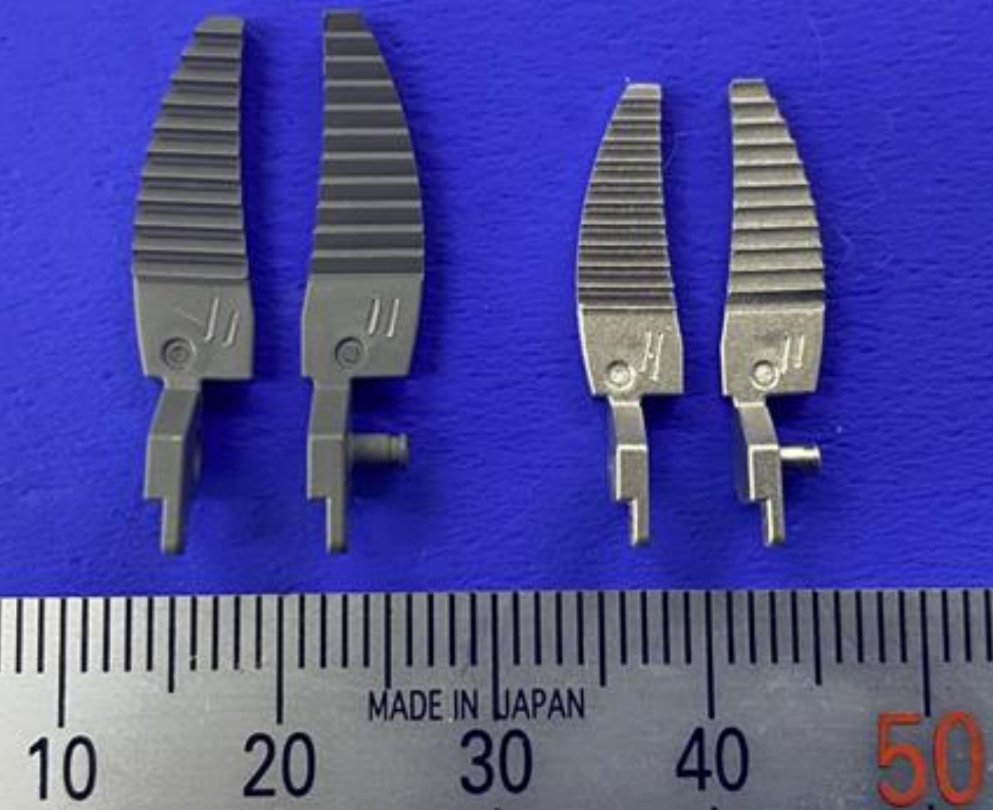
MIMのメリット
ここからは、MIMのメリットについて解説します。
大量生産に適している
一般的な樹脂材料の射出成形と同じく、金型を用いた製造方法となるため、同形状・同品質の製品を量産することが可能です。
また、多数個取りも可能であるため、高い生産性を実現できます。
高い製品強度が得られる
MIMにより作られる製品は、焼結工程で密度の高い構造を形成するため、溶性材に近い強度を得ることができます。
難削材の複雑形状部品を製造できる
微細な粉末は、複雑な形状でも均一に充填できるため、切削加工では難しいような複雑形状の部品も製造可能です。
また、粒径が小さい粉末を用いることで、良質な表面粗さを得ることもできます。
MIMの課題
多くのメリットを持つMIMですが、その一方でいくつかの技術的な課題も抱えています。
成形条件の設定が難しい
MIMで用いられる材料は、一般的な射出成形で用いられる樹脂材料と比べて、流動性は高いが固まりやすい(熱伝導率が高い)という特徴があります。
その影響で、バリやショートといった成形不良が起きやすく、一般的な樹脂材料と比較すると、安定した成形を行える条件の範囲が狭いため、条件決めが難しいという課題があります。
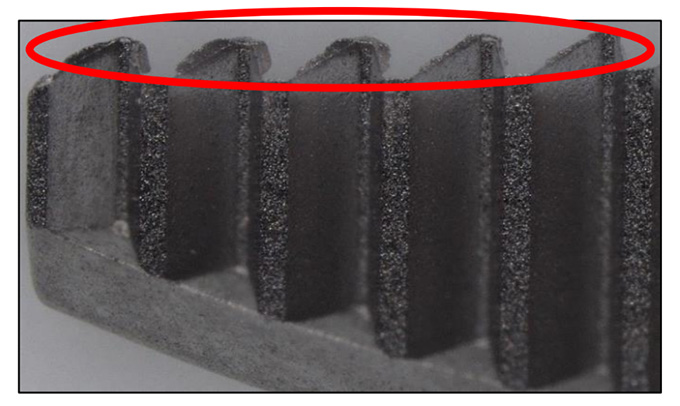
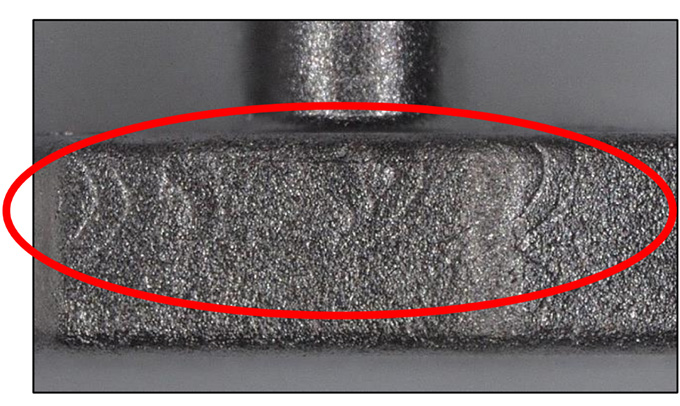
2次加工の必要性
上述の通り、MIMは成形品の品質を安定させることが難しいため、多くの場合、ある程度のバリや外観不良を許容し、機械加工などによる二次加工を行うことが一般的です。
一般的な樹脂材料の射出成形と比較すると、成形後の加工にもコストが発生するため、生産性に課題があるとも言えます。
金属粉末による齧り(かじり)・動作不良の問題
MIMの材料は、樹脂材料と比較すると流動性が高いため、充填時に高い圧力がかかる際、スクリュやシリンダとチェックリングの隙間に入り込みやすくなっています。
こういった隙間に金属粉末が入り込んでしまうと、成形機部品を傷つけてしまったり(齧り)、固着して機械が動かなくなったりといった問題が発生します。
それを防ぐため、従来のMIM用射出成形機は摺動部(しゅうどうぶ)の隙間を広めに設計したり、チェックリングを外してしまったりといった対策が一般的でした。
ただ、そうしてしまうと材料を金型に射出する際の圧力が逃げてしまう(保圧を高くできない)ため、ただでさえ狭くなっているMIMの成形条件幅をさらに狭めてしまうことになります。
精密MIM用射出成形機 m:MIM
上記の課題を解決するためソディックが開発したのが、精密MIM用射出成形機『m:MIM』です。
m:MIM仕様の射出成形機は、プランジャ部分の構造が新設計されており、MIMにおいてもソディック機の特徴であるV-LINE®方式のメリットを最大限享受することができます。
V-LINE®方式
V-LINE®方式は、材料を混錬・溶融する可塑化部と、材料を計量・射出する射出部を別個にしたソディック製射出成形機の独自構造です。
両者が一体となっている一般的な射出成形機と比べて、充填量のばらつきが少なく、成形不良を抑制できるメリットがあります。
詳細はこちら
ここからは、m:MIM仕様射出成形機がどのようにMIMの課題を解決しているのかを解説いたします。
高い射出保圧力による成形不良の抑制
m:MIM仕様射出成形機最大のポイントは、MIM専用に新設計された射出部の構造にあります。
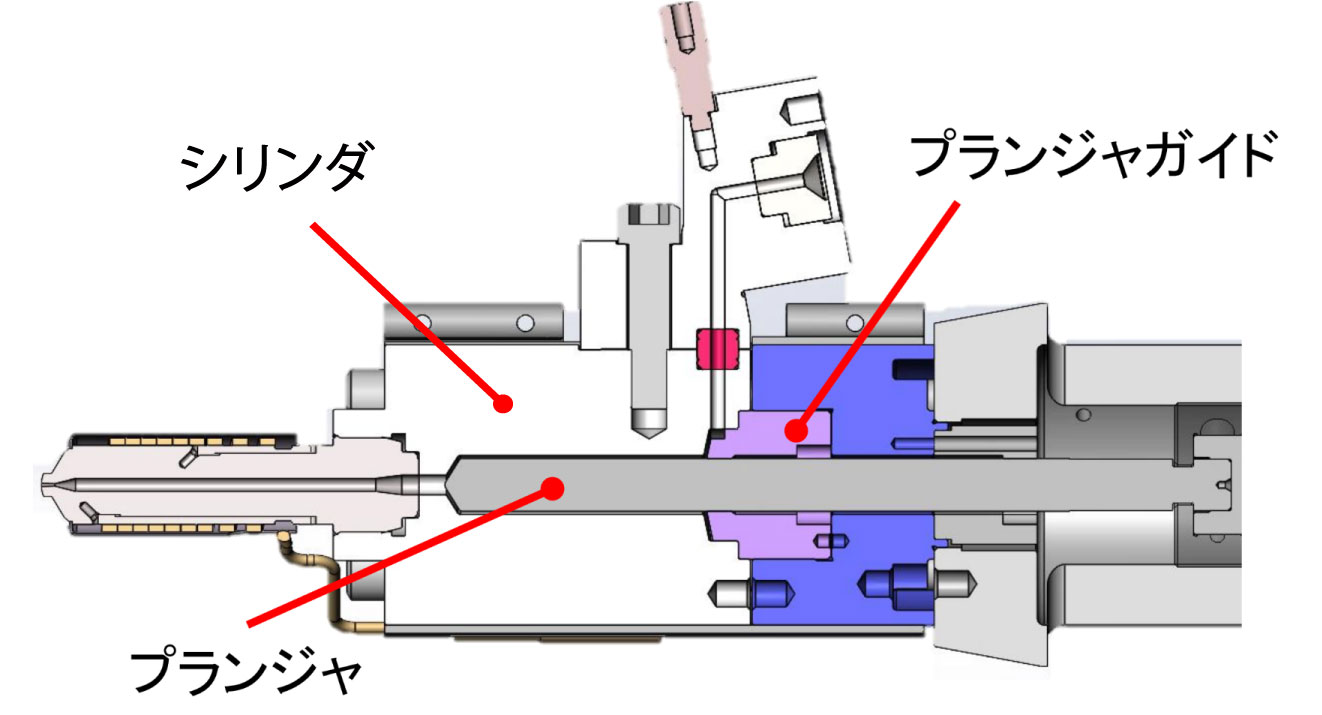
プランジャとシリンダの隙間は齧りを防ぐために広めに設計されていますが、射出時は圧力によってプランジャガイドが僅かに閉じることで、材料が漏れだすのを防ぐことができます。
これにより、齧りを抑制しつつ保圧を高めることができるため、バリを抑制する正確な充填量制御・高い停止精度と、成形材料が固化する前に充填可能な高い立ち上がり応答性というV-LINE®方式の特長を最大限発揮することが可能です。
ソディックのm:MIMであれば、バリの除去といった二次加工が不要なネットシェイプ成形(※)の可能性を追求できます!
また、m:MIM仕様射出成形機は、一般的に難しいとされているチタン材の成形も可能です。
ネットシェイプ:製品の最終形状
まとめ
今回は、MIM(金属粉末射出成形)とはどういうものか、MIMが持つメリットと課題について解説しました。
ソディックが開発した精密MIM用射出成形機『m:MIM』は、ソディック独自技術であるV-LINE®構造のメリットをMIMにおいても100%発揮することができ、MIMが持つ課題の解決に大きく貢献します。
ソディック製射出成形機にご興味がございましたら、ぜひ以下のフォームよりお問い合わせください。