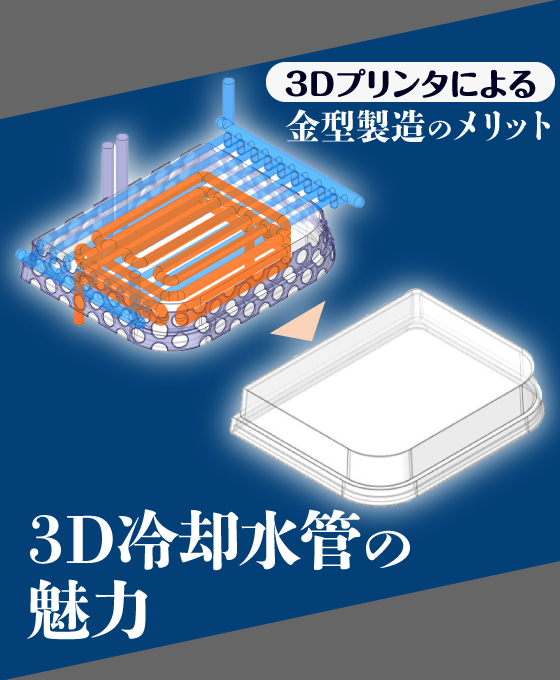
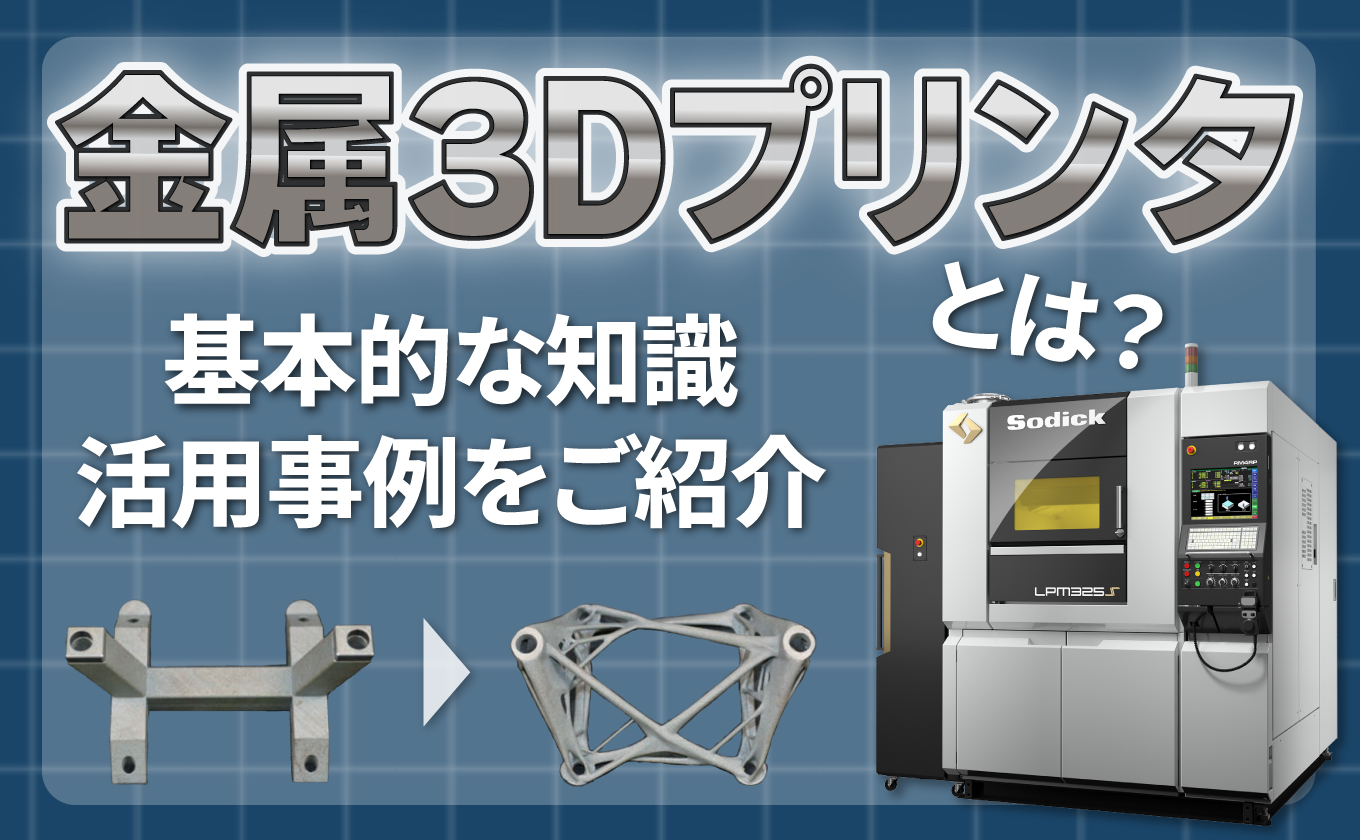

読了まで分
近年では3Dプリンタ活用の幅が広がり、金属部品や金型を製造する金属3Dプリンタも注目を集めています。
金属3Dプリンタは従来加工では難しい複雑形状や工程集約を実現することができるため、部品設計や製造プロセスに大きな変革をもたらしています。
最新の金属3Dプリンタは航空業界や自動車業界、医療業界をはじめさまざまな業界で活用されており、技術進歩に伴って今後さらに活用範囲が広がることが期待されています。
この記事では、金属3Dプリンタの基本的な知識や活用事例に解説します。
目次
金属3Dプリンタ(アディティブ・マニュファクチャリング)とは
金属3Dプリンタは材料を『積層』または『付加』することで形状を作り出す装置であり、その特徴から『付加製造』あるいは『Additive Manufacturing(アディティブ・マニュファクチャリング)』とも呼ばれます。
※頭文字を取って『AM』と呼ばれることもあります。
金属3Dプリンタの造形方式には様々な種類が存在しますが、この記事では、造形精度が高いことから主流となっているLPBF(レーザパウダーベッド方式)を採用した、ソディック製金属3Dプリンタについて解説します(2025年現在)。
金属3Dプリンタによる造形の流れ
金属3Dプリンタは、3DCADデータ(※1)を基に、CAM上で作成したジョブファイル(※2)を機械に取り込むことで、積層造形を実行します。
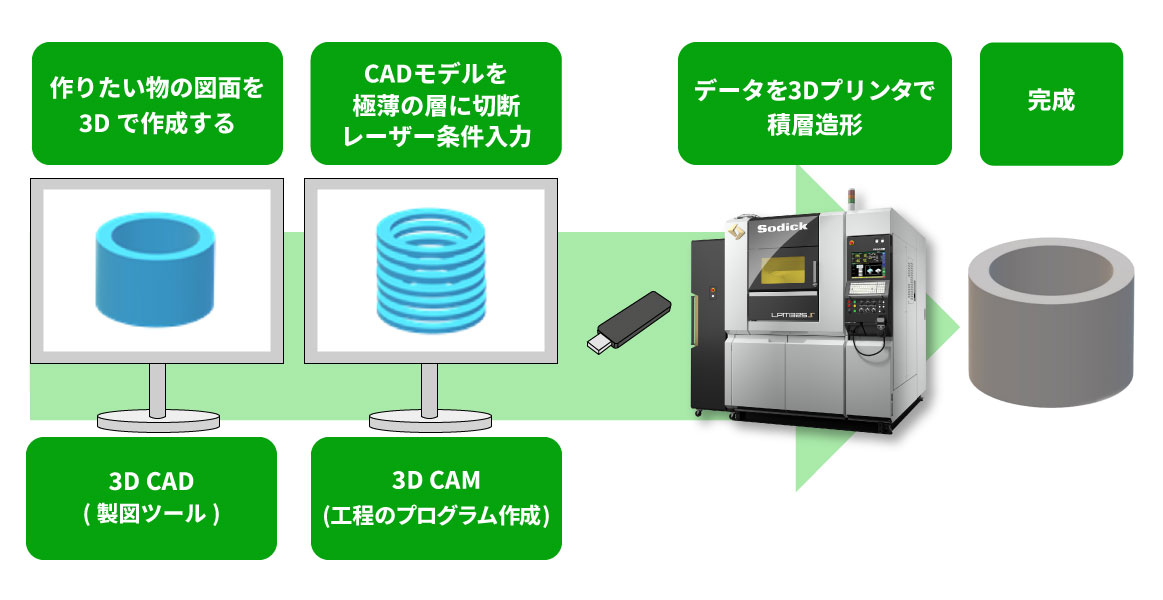
※1 コンピュータを用いて設計・作図された図面
※2 一層ごとのレーザ照射パターン・条件を定義するデータ
レーザパウダーベッド方式(LPBF:Laser Powder Bed Fusion)では、粉末状の金属を敷き詰めて、レーザで溶かし固めながら一層ずつ物体を造形していきます。
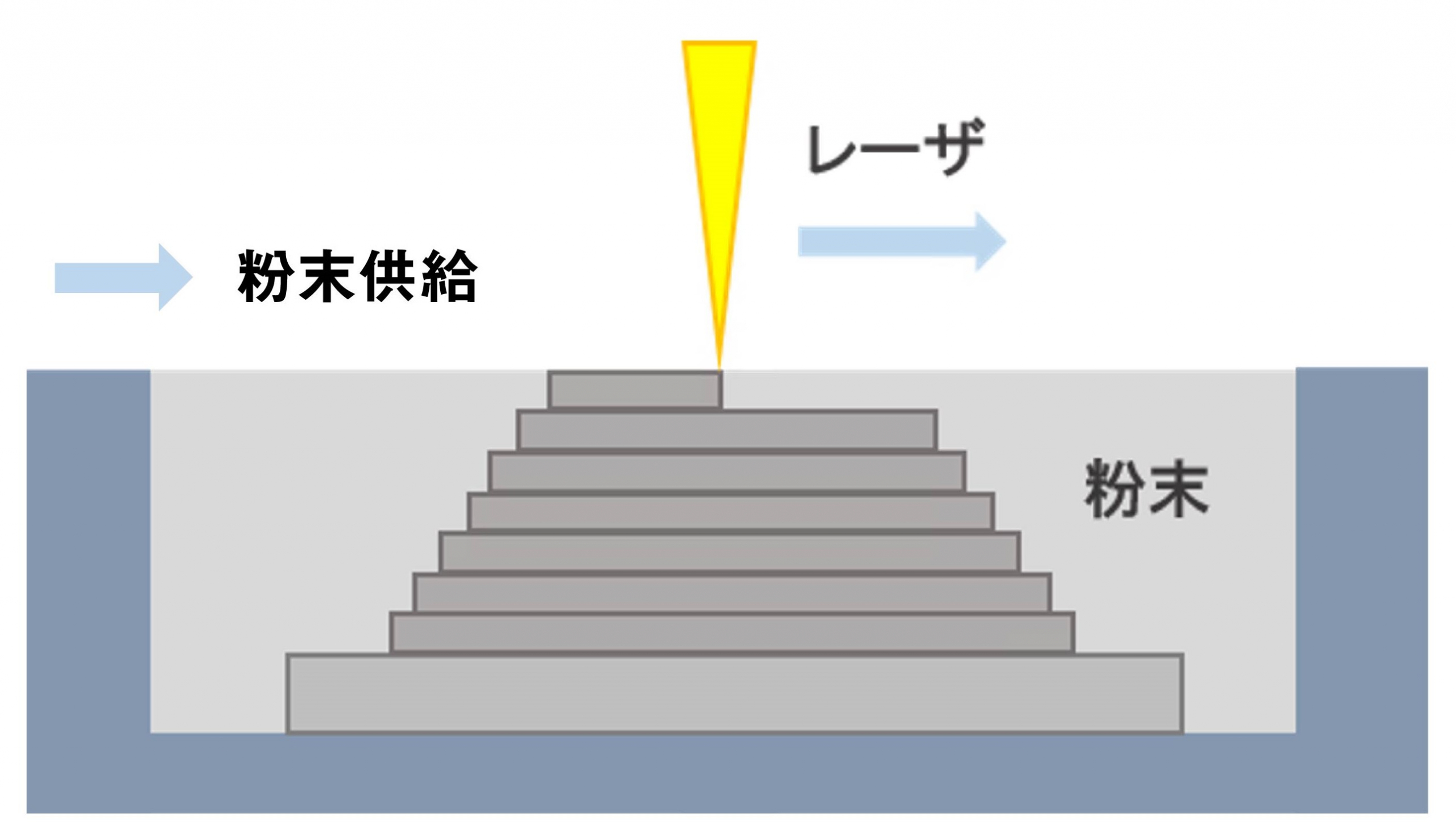
造形物は敷き詰められた金属粉末の中で造形され、完成した後に金属粉末の中から取り出されます。
このパウダーベッド方式は、精度が高く、微細形状の造形も得意としています。
金属3Dプリンタの構造
ここからはソディック製金属3Dプリンタの構造を解説していきます。
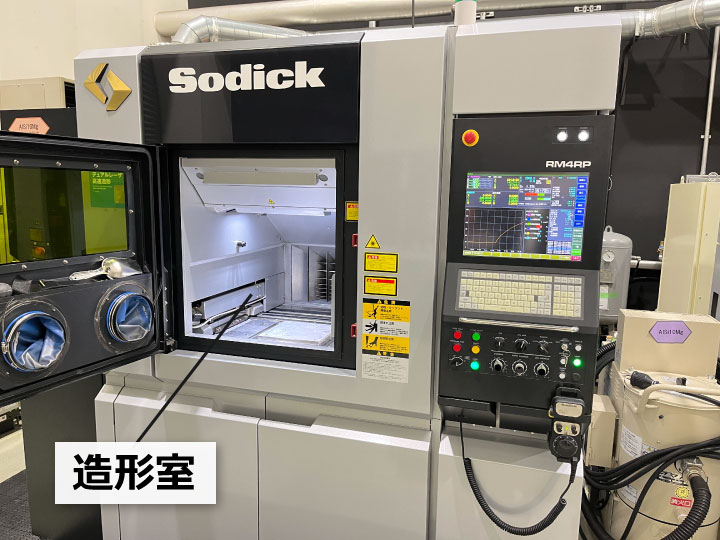
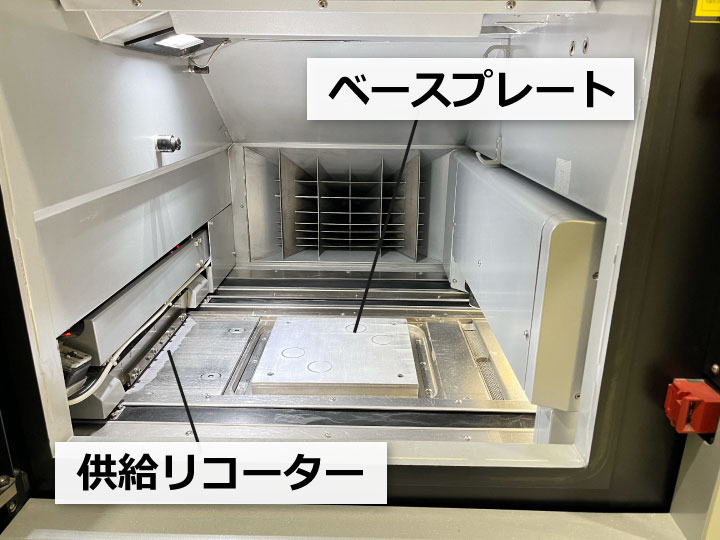
造形室
造形室は金属材料を積層して造形するためのスペースです。
高エネルギー密度のレーザを利用するため、造形室内は化学反応を起こしにくい不活性ガスで満たされています。
ベースプレート
造形物の土台となる金属の板です。
造形物はこのベースプレートの上に溶着・積層されていき、造形完了後、ワイヤカットなどで切り離します。
供給リコーター
造形室内には金属粉末を敷き詰めるための供給リコーターが備えられています。
金属粉末をレーザで溶かし固めた後に、供給リコーターが移動しながら新たな粉末を供給します。
これを繰り返すことで造形物が積層されていきます。
レーザ発振器・ガルバノユニット
造形室内には、レーザ発振器とガルバノユニットが取り付けられています。
レーザ発振器が発生させたレーザを、ガルバノユニットに搭載されたミラーが反射することで、レーザ照射位置を制御しています。
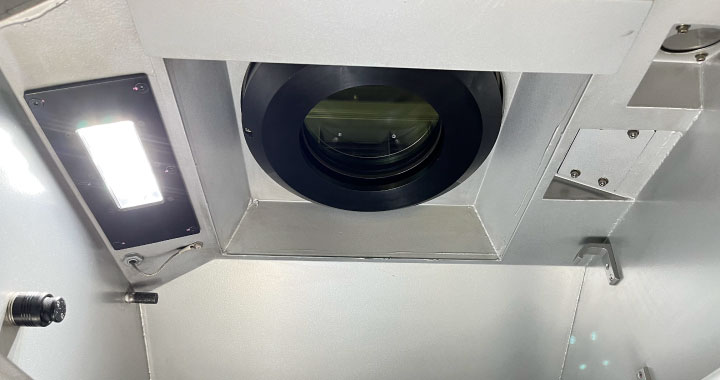
金属3Dプリンタのメリット
ここからは従来の加工方法と比較した際の、金属3Dプリンタの主なメリットを3つご紹介します。
従来加工では難しい複雑な形状や構造を造形できる
金属3Dプリンタでは従来加工法と比べて非常に自由度の高いものづくりが可能であり、従来は加工が困難であった複雑形状を実現することができます。
分かりやすい例として、近年話題となっている設計技術『ジェネレーティブデザイン』の採用が挙げられます。
ジェネレーティブデザインとは、設計の要件を指示することでAIにより生成されるデザインのことで、人間の発想を超えた付加価値の高い形状を作り出すことができます。
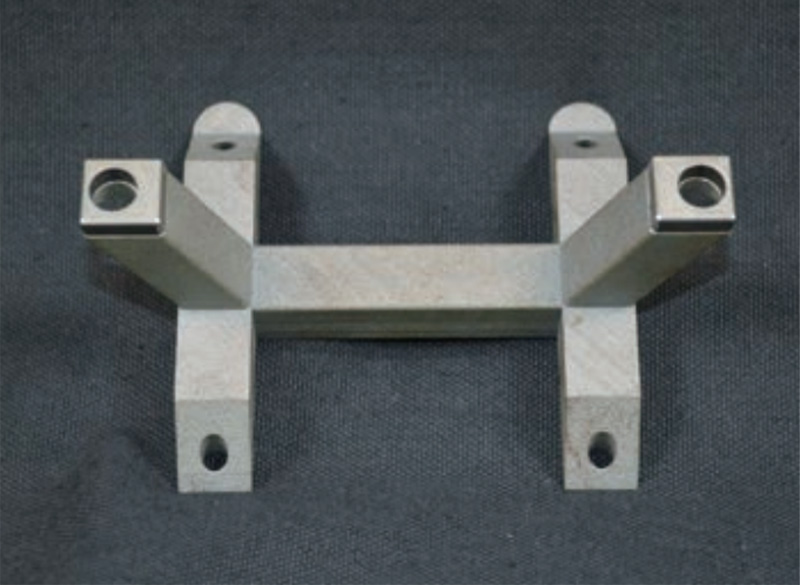
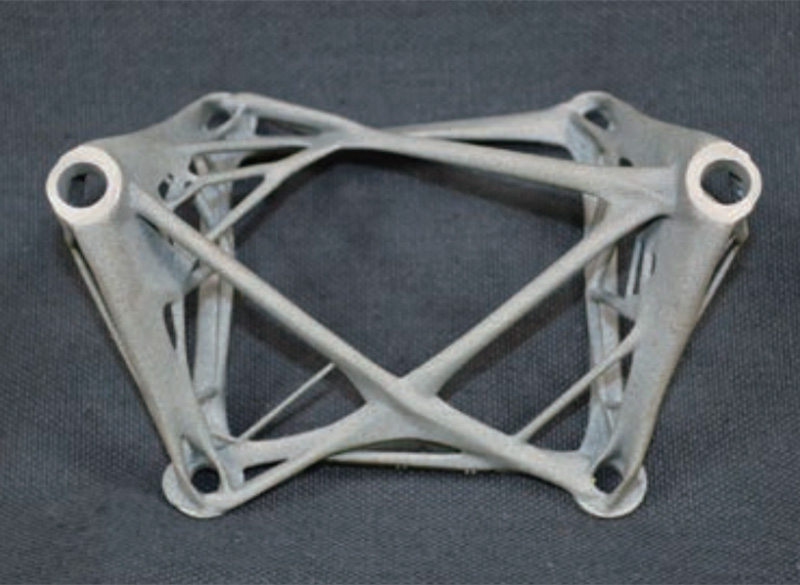
金属3Dプリンタはジェネレーティブデザインによる複雑な形状を一体化構造で造形できるため、高耐久性・軽量化といった様々な付加価値を持つ部品を製作することができます。
上の画像の例では約70%の軽量化に成功しています!
工程集約による省人化・省スペース化・コスト削減
従来であれば、マシニングセンタ・形彫り放電加工機・ワイヤ放電加工機といった複数台の工作機械で製造していた製品・形状も、金属3Dプリンタによって1つの工程に集約できる場合があります。
これによりオペレータの作業工数を抑えることができ、設備の省スペース化やリードタイム短縮にも効果を発揮したという事例があります。
以下の金型製作を例に、従来工法と金属3Dプリンタによる製作プロセスを比較してみます。

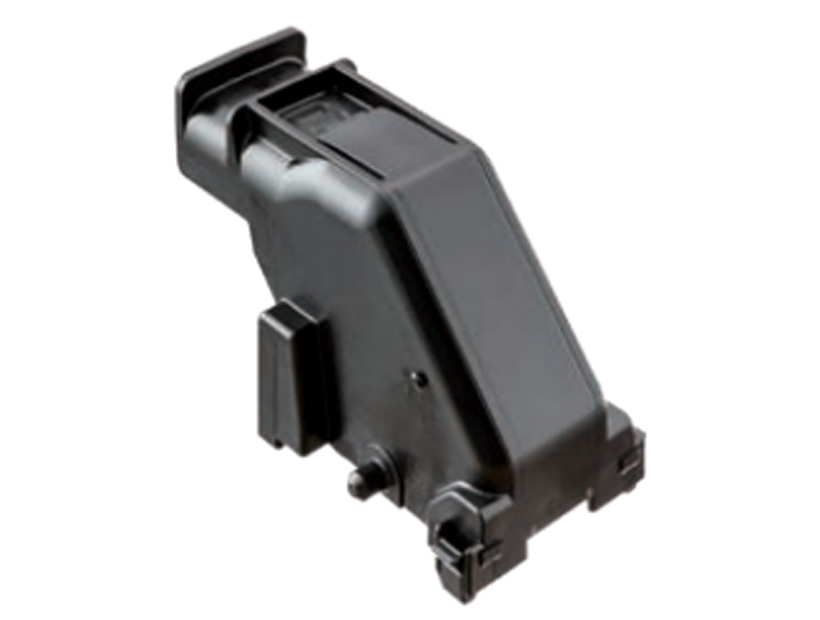
従来工法では、50点以上の部品数に分かれており、複数台の工作機械による加工が必要でした。
この工程に金属3Dプリンタを導入したことで、部品数はキャビティ1点、コア2点の計3点に抑えることができ、加工プロセスもソディック製金属3Dプリンタ(OPM)のみで完結させることができました。
※ソディック調べ
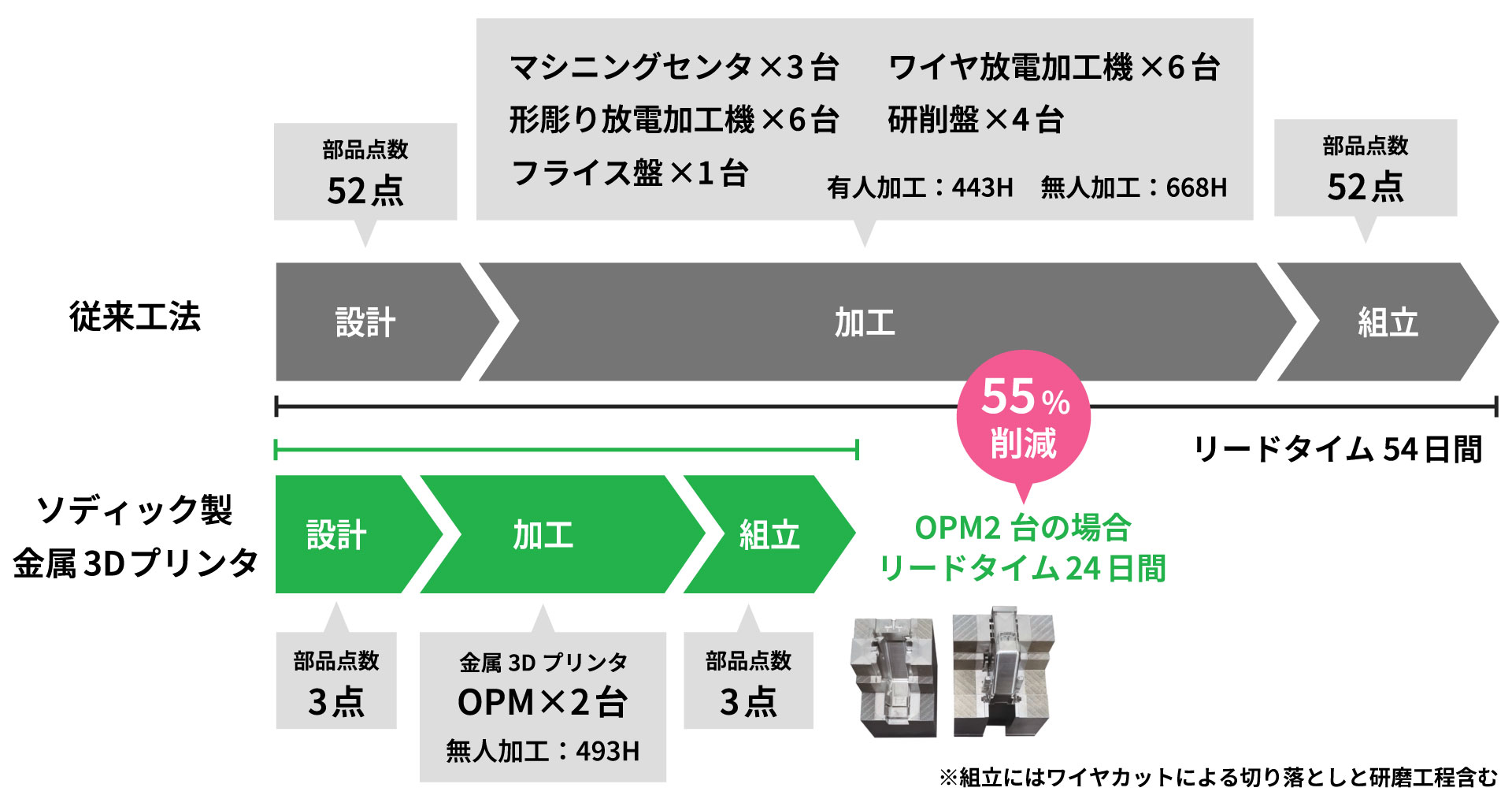
また、材料から不要な部分を削り出す切削加工と比較すると、必要な部分だけを造形できる金属3Dプリンタは、材料費を抑えられるうえに、環境にもやさしいというメリットがあります。
複雑な内部構造の造形
例えば金型製作を例に考えてみます。
以下のような丸物形状の金型内部に冷却水管を設ける場合、ドリルで切削する従来工法では、どうしても直線的な形状の水管になってしまいます。
しかしそれでは、水管とキャビティ空間の距離が場所によってばらつき、冷却にムラが生じてしまいますので、下図の3Dモデルのように、金型の形状に沿った曲線的な水管形状が理想的です。
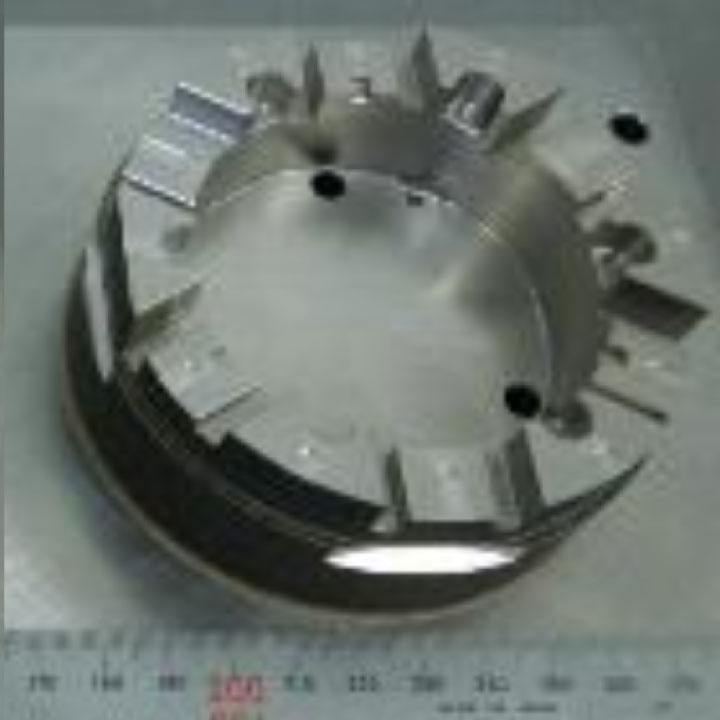
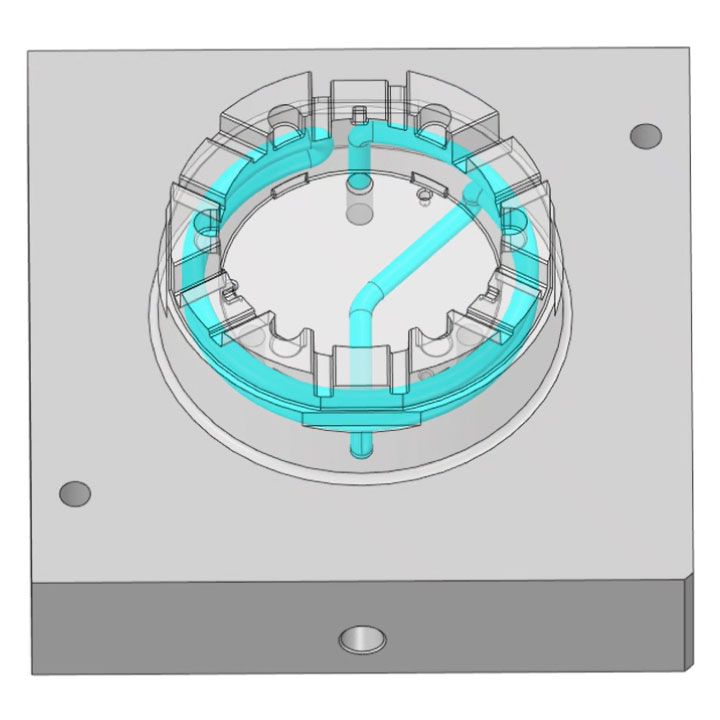
金属3Dプリンタであれば、このような複雑な内部構造を持つ形状も造形することが可能です。
この特長により、金型設計の自由度が増し、冷却効率を追求した水管設計が可能となります。
こういった複雑な形状の冷却水管は3D冷却水管と呼ばれ、プラスチック金型においては成形サイクルアップや製品形状の精度改善、ダイカスト金型においては金型パーツの寿命延長といった効果を発揮します。
詳しくは以下の記事で解説しておりますので、ぜひ併せてご覧ください。
ソディック製品の特長
一言に金属3Dプリンタと言っても、様々なメーカーが多種多様な製品を開発・製造しています。
その中でもソディックの金属3Dプリンタは、以下のような強みを持っています。
造形だけでなく、切削加工まで1台で対応可能
ソディックは金属3Dプリンタだけでなく、放電加工機やマシニングセンタといった工作機械の開発・製造ノウハウも有しています。
それ故に、ソディック製金属3Dプリンタ『LPMシリーズ』には基本的な造形機能だけでなく、造形後の二次加工で必要となる基準面を切削加工する機能も搭載されています。
この機能により、造形時の取り代を最小限に抑えることができ、造形コスト(造形時間)・切削加工コスト(切削加工時間)の両方を削減することが可能です。
造形物の二次加工と基準面について
金属3Dプリンタの焼結面は粗いため、造形物は機械から取り出した後に、切削加工機で表面を仕上げるのが一般的です(二次加工)。
しかしその際、粗くなっている焼結面をそのまま二次加工の基準面にしてしまうと、測定のばらつきが生じてしまいます。
そのため本来は、二次加工で取り残しがないように、加工の取り代を多目に設ける必要があるのですが、ソディックの金属3Dプリンタは切削機能によって滑らかな基準面を設けることができるため、必要な取り代を最小限に抑えることができます。
また、高速ミーリング加工機能付金属3Dプリンタ『OPMシリーズ』は、造形物の表面を滑らかに仕上げる二次加工まで一台で対応可能です!
従来複数台の工作機械で製作していた製造プロセスを工程集約し、作業者の教育コスト削減や省人化、作業場の省スペース化を実現したいというお客様にとって最適なソリューションとなりえます。
正確な位置決め機能によるハイブリッド造形
上記の切削機能が搭載されていることにより、ソディック製金属3Dプリンタには、放電加工機やマシニングセンタでは当たり前となっている、位置決め機能を有しています。
このことが、他の工作機械で製作した加工物に継ぎ足す形で造形を行う『ハイブリッド造形』において優位に働き、ズレのない精密な造形を可能にします。
詳しくは以下の記事で解説していますので、そちらも併せてご覧ください。
大型の造形を可能にする特許技術と自社開発粉末
金属3Dプリンタによる造形の大きな課題の1つに『残留応力による反りの発生』があります。
しかしながら、ソディックが独自開発した特許技術『SRT工法』はこの問題を解決し、さらに、自社開発の金属粉末材料『SVM(SKD61改良材)』と組み合わせることで、金属3Dプリンタによるダイカスト金型製作の可能性を大きく広げました。
SRT工法の開発秘話については以下の記事で解説しておりますので、ぜひ併せてご覧ください。
金属3Dプリンタ活用事例
金属3Dプリンタはさまざまな業界の課題解決に活用されています。
この章では、航空業界や自動車業界、医療業界における金属3Dプリンタ活用事例をご紹介します。
航空業界
部品の強度を確保しつつ、いかに軽量化するかが航空業界における普遍的な課題ですが、金属3Dプリンタであれば従来の切削加工では難しい複雑形状を実現できるため、ジェネレーティブデザインを採用することができます。
すでに実機にも金属3Dプリンタ製の部品が搭載され、実用化されているものもあります。
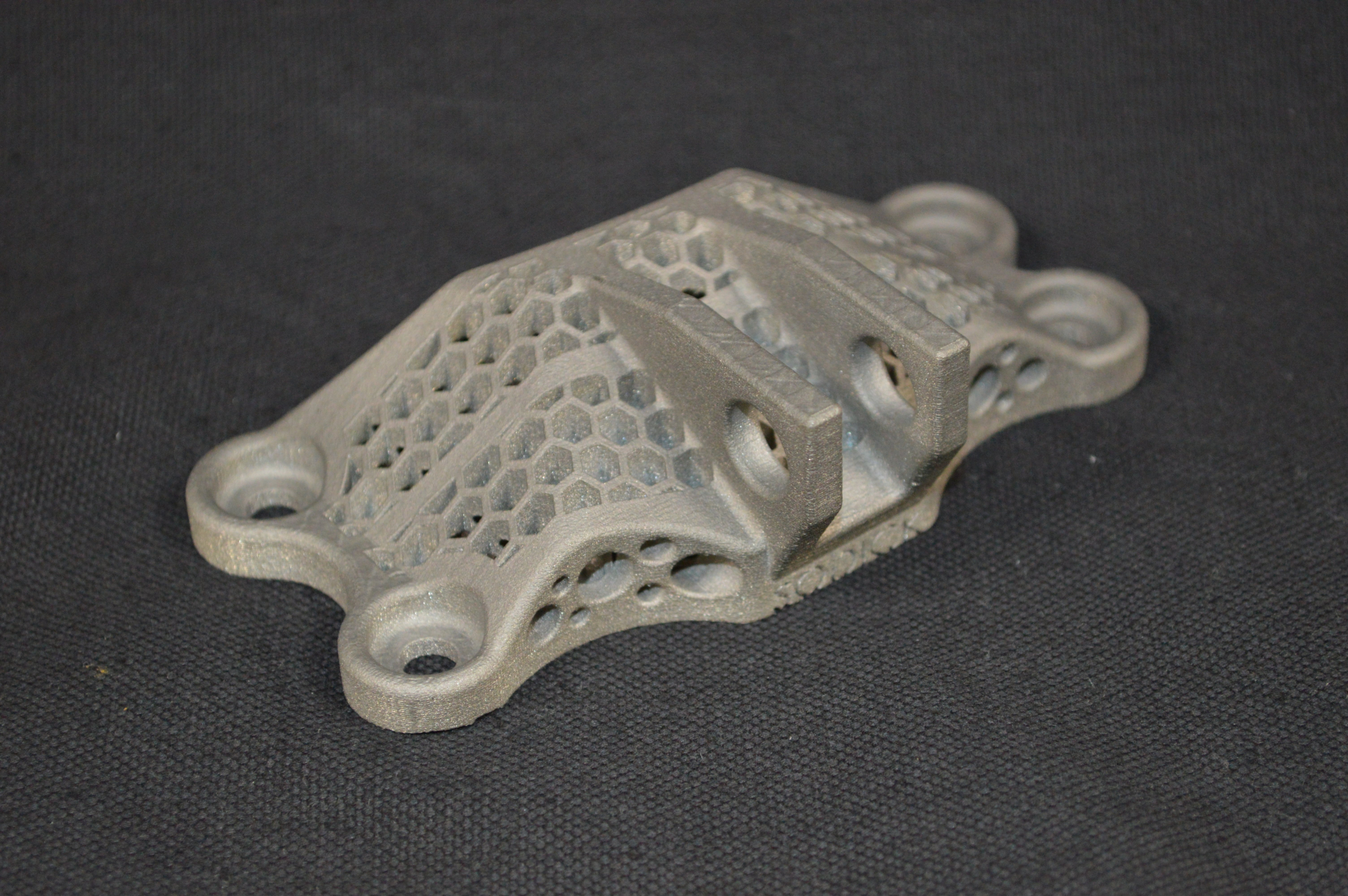
自動車業界
部品点数の多い自動車の製造プロセスにおいては、金属3Dプリンタの特長である一体化構造での造形が、工程集約・軽量化・試作期間の短縮などに大きく寄与しています。
従来の方法で複雑な形状を加工する場合、いくつかのパーツに分けて、加工した後に組み立てるなど、多くの工程が必要であったのに対し、金属3Dプリンタを活用することで、複数部品の一体化による工程削減・リードタイム改善を実現することができます。
例えば、複雑形状配管部品の1つとして、エンジンなどの排気経路に使用されるマニホールドがあります。
一般的な製作方法では、加工しやすい形状に分割された部品を溶接でつなぎ合わせた後、仕上げ加工を行いますが、金属3Dプリンタを用いることで、溶接レスの一体構造を実現できます。
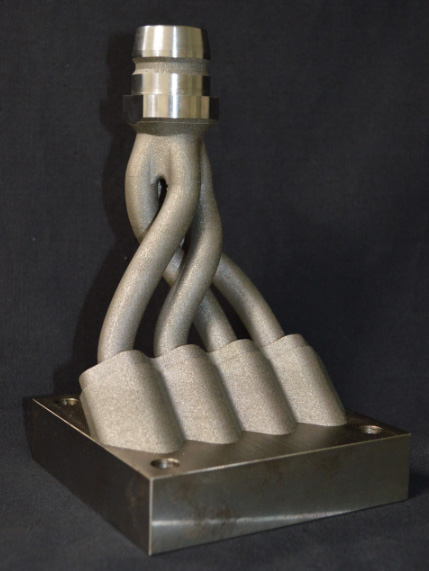
医療業界
データを基に造形を行うという金属3Dプリンタの特徴から、人体のスキャンデータを用いることで個々人の身体に合わせたインプラントの製作が可能となり、身体への負担軽減・QOL向上に効果があるとされています。
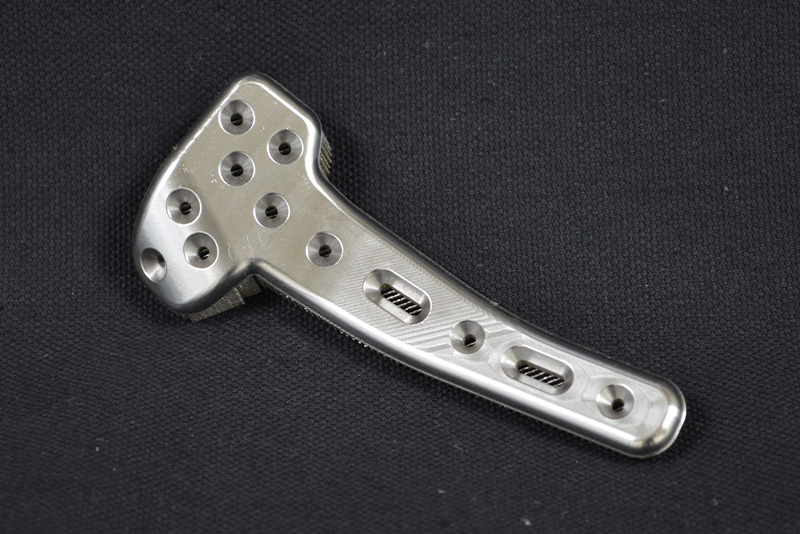
また多孔質構造やメッシュ構造のような複雑形状を実現できることや、チタン・コバルトクロムといった生体適合性に優れるも切削しづらい素材を造形できることも、金属3Dプリンタが医療業界で活用される要因と言われています。
ソディック製金属3Dプリンタはチタン・コバルトクロムの造形に対応しています。
ご要望の粉末材料に合わせて機械仕様の検討も可能ですので、ぜひ記事末尾のフォームからお問い合わせください。
まとめ
金属3Dプリンタは、従来加工では難しかった複雑な形状や構造を実現し、複数部品構成の製品を一体化構造で造形できることから、コストや機能面で革新的なものづくりを可能にします。
金属3Dプリンタの技術は将来的にさらなる成長が見込まれ、今後も様々な業界に革新をもたらすことが期待されています。
金属3Dプリンタの導入にご興味がございましたら、ぜひ以下のフォームからお問い合わせください。