
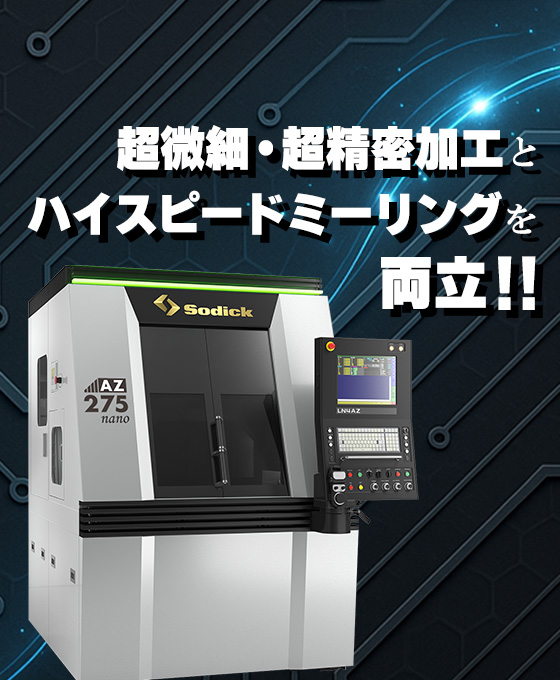
読了まで15分
こんにちは、SurVibes(さぁ!バイブス)編集部です!
今回は形彫り放電加工の作業工数を劇的に削減する3次元CAMをご紹介します。
精密な加工を実現できる特長から、金型の製造などに活用される形彫り放電加工ですが、その作業現場ではまだまだ人手による数値手入力や動作の確認が行われており、労働人口の減少が問題視されている昨今においては、作業の効率化・属人性の排除が強く求められています。
今回ご紹介するソフトウェアはこれらの課題解決に大きく寄与するものです!
形彫り放電加工の効率化・コスト削減にご興味がございましたらぜひ最後までご覧ください。
形彫り放電加工を実施する上では、段取り作業や加工動作のプログラム作成が必要になりますが、まだまだ図面から数値を読み取り、機械側へデータを手入力するといった人手による作業が多く見られるのが現状です。
そのため形彫り放電加工機は他のNC工作機械と比べて非稼働時間(人手作業により加工が止まっている時間)が長くなってしまい、生産性が上がりにくい傾向にあります。
また、手入力ミスによる不良の発生も珍しくありませんが、放電加工は精度が高いという特長から、ものづくり全体の下流工程に位置する場合が多く、そこで不良が発生してしまうと上流工程で発生したコストが全て無駄になってしまうという大きなリスクを抱えています。
そんな形彫り放電加工現場の課題を解決すべくソディックが開発したのが3次元形彫り放電CAMシステム『DiproSOLID(ダイプロソリッド)形彫り放電CAM』です!
DiproSOLIDは株式会社ソディックの登録商標です。
DiproSOLID形彫り放電CAMのご紹介に入る前に、そもそもCAMとは何なのかを簡単に解説いたします。
CAM(キャム)はComputer Aided Manufacturingの略称で、CADで作成した図面データを元に、実際に加工を行うプロセスを機械に指示するNCデータを出力するソフトウェアです。
CAD
CADはComputer Aided Designの略称で、従来は紙に手書きで製図していた図面や設計書を、コンピュータ上で作成・編集・共有するための技術やソフトウェアのことを指します。
CADの中にも、2次元の平面上で図面を製図するための2D CADと、3次元モデルを作成・編集できる3D CADがあります。
DiproSOLID形彫り放電CAMは3DソリッドモデルのCADデータを利用して加工プログラムを作成しています。
従来はNCデータを作成するソフトウェアに、図面から読み取った数値を人間が手入力する作業が必要でしたが、CAMはCADデータを読み取ることでその手間を排除し、工数削減や入力ミスによる不良の抑制に寄与しています。
ここからは、ソディックが開発した3次元形彫り放電CAMシステム『DiproSOLID形彫り放電CAM』について解説していきます。
DiproSOLID形彫り放電CAMの導入メリットは、従来の人手作業をCAMに置き換えることによる、劇的な工数削減と不良率低減にあります。
以下ではそのメリットをより具体的にご紹介していきます。
DiproSOLID形彫り放電CAMは電極とワークのアセンブリデータを読み込むことで、従来手入力していた加工位置の座標数値を自動取得することができます。
これにより人手作業を削減でき、手入力ミスの抑制にもつながります。
アセンブリデータとは
3D CADのソリッドモデルにおいて、いくつかの部品が一体となったデータをアセンブリデータと呼びます。
形彫り放電加工においては、1つのワークと複数の電極が組み合わさった状態のアセンブリデータが、設計のアウトプットとして仕上がりますので、それをそのままCAMに読み込むことで、簡単に加工位置座標をNCデータに反映させることができます。
形彫り放電加工段取り作業の1つに、電極やワークの位置を測定して機械座標に取り込む『芯出し(位置決め)』がありますが、この芯出し作業に関しても、加工動作と同じく機械に指示する必要があります。
従来は、基準球と電極・ワークの接触点情報を機械に手入力するか、手元操作盤を使って手動で測定作業を行っていました。
電極やワークの形状がシンプルであればまだ良いのですが、形状が複雑な場合、どの向きからどの位置に接触させるといった情報が煩雑になり、作業工数・ミスのリスク共に増加します。
しかしながら、DiproSOLID形彫り放電CAMを利用すれば、シンプルなインターフェースでグラフィカルに確認しながら機械動作を指示できますので、芯出し定義の効率が劇的に改善します!
DiproSOLID形彫り放電CAMのメリットは芯出しの動作定義をスムーズにするだけに留まりません!
動作定義後、実際に芯出し作業を行う際には、「電極やワークの測定箇所に異物が付着していて正確な芯出しが行えなかった」「3Dモデルと実物の寸法に差異があった」「荒電極と仕上げ電極を間違えてセットしてしまった」といったことが原因で、不良が発生してしまうリスクがあります。
それを防ぐため、芯出し作業時、特に精度が厳しい場合は、作業者は事前に確認を行ってから、本作業に入っています。
それでも、荒電極と仕上げ電極の寸法差など、目視で識別できないレベルのミスを防ぐことはできず、必ずしも労力に見合った結果が得られるとは限りません。
一方で、DiproSOLID形彫り放電CAMには以下の機能が搭載されており、目視による確認を必要とせず、上記のリスクを排除することができます!
形彫り放電加工には、加工したい形状や電極に応じて複数の加工パターンがあり、正しく加工を行うためには、NCデータ作成時に適切な加工パターンを設定しておく必要があります。
しかし加工パターンは15種類以上存在しますので、慣れていない作業者であれば加工パターンの設定ミスによる不良を起こしてしまうことも珍しくありません。
そこでDiproSOLID形彫り放電CAMには、読み込んだ3Dソリッドモデルから電極形状の特徴を認識し、最適な加工パターンを自動で絞り込んでくれます!
この機能により加工パターンの設定ミスを防ぎ、不良率の低減に寄与します。
形彫り放電加工の加工効率とはすなわち、放電現象をどれだけ効率的に起こせるか、言い換えると加工面積に応じた最適なエネルギーを常に供給できるかであると言えます。
加工面積に応じた最適なエネルギーを与えなければ放電現象は起きにくくなり、加工の進みが遅くなってしまいます。
しかしながらこの加工面積は、電極が加工物を彫り進んでいくごとに絶えず変化するため、それに伴い最適なエネルギー量も変化していきます。
特に加工深さごとに大きく加工面積が変わってしまうような形状であれば、エネルギー量の調整は非常に難しくなります。
そのため従来では、作業者が加工深さに応じて最適条件を確認しながら手動で調整する、といった職人的技量が必要な加工もありました。
しかしDiproSOLID形彫り放電CAMはこの課題を解決することができます!
DiproSOLID形彫り放電CAMは読み込んだ電極の3Dソリッドモデルから深さごとの加工面積を自動で算出し、最適な加工条件を抽出することができます。
DiproSOLID形彫り放電CAMにより、加工時間を約40%短縮できたというデータも出ています(ソディック調べ)。
形彫り放電加工では、複雑な形状を加工するため、複数の電極を用いることが一般的ですが、電極が多くなってしまうと段取り替えが発生し、その分加工が止まってしまいます。
そこで、電極の本数を抑えるために、1つの電極に荒加工用と仕上げ加工用の2つの形状を搭載するトンボ加工や、1つの電極に複数の形状を並べて電極をスライドさせながら加工していくピッチ加工といった多彩な加工方法が存在します。
DiproSOLID形彫り放電CAMは上記のような多彩な加工方法にも対応しており、複雑な段取りも簡単に定義することができます。
形彫り放電加工は電極の形状を加工物に転写する加工法ですので、電極製作時に寸法誤差が生じてしまうと、加工物寸法にも影響を与えてしまいます。
しかしDiproSOLID形彫り放電CAMは、読み込んだ3Dソリッドモデルと段取り時の測定結果から、電極製作時に生じた誤差を自動で検出し、加工深さとステップ量へ反映することで、加工物寸法への影響を最小限に抑えることができます。
形彫り放電加工では、NCデータでプログラムした測定動作・加工動作が、物理的な干渉を起こさず進行するかを確認するために、加工物はセットせずに動作だけをチェックする『ドライラン』という確認プロセスがよく行われます。
しかしながら、このドライランにもけっこうな時間がかかってしまい、機械稼働率を低下させてしまう要因となっています。
ですがDiproSOLID形彫り放電CAMは、芯出し測定から加工までの動作をコンピュータ上でシミュレーションすることができるため、ドライランによる確認を省略することができ、加工前の確認作業を大幅に削減することができます。
形彫り放電加工では、加工完了後に加工物の寸法を計測し、狙いの寸法に達していない場合必要量追加で加工を行う『追い込み加工』がよく行われます。
従来であれば、計測結果に応じて加工プログラムを再編集しなければならないところ、DiproSOLID形彫り放電CAMでは、加工位置ごとに追い込み量を指定するだけで簡単に追い込み加工用プログラムを生成することができます。
高精度が売りの形彫り放電加工ですが、精度は多少犠牲にしても稼働時間を増やして生産性を上げたいという需要も一定数存在します。
そういった際によく利用されるのが『外段取り』です。
外段取り
本来は機上で行う段取り作業ですが、3次元測定機等を用いて芯ずれ量の測定を行うことを外段取りと言います(放電加工機本体の外で測定するため外段取りと呼ばれます)。
機上で測定する場合と比べて正確性は劣りますが、測定作業を別工程で行うため、機械稼働率の向上に寄与します。
DiproSOLID形彫り放電CAMは、3次元測定機による測定結果をCSVファイルとして読み込むことで、NCデータへ自動反映することができます(手入力不要)。
単体で利用しても大きな効果を発揮するDiproSOLID形彫り放電CAMですが、ATC(オートツールチェンジャ)・APC(オートパレットチェンジャ)・パレットスケジューラとの組み合わせにより、自動化システムを構築することも可能です。
形彫り放電加工の自動化は大規模な投資ですが、労働人口の減少が問題視されている昨今においては、自動化の必要性は年々高まっています。
将来の自動化を見据えて、まずはCAMによる部分的な自動化から導入してみるのはいかがでしょうか。
一般的な形彫り放電加工を想定し、DiproSOLID形彫り放電CAMの導入効果を表にまとめました(ソディック調べ)。
CAMの導入により、約87%の大幅な人的作業時間削減を実現できています!
作業項目 | 従来の人的作業時間 | 放電CAM使用時の人的作業時間 |
放電加工レイアウト図作成 | 2H | 0H |
加工NCプログラム作成 | 1H | 0.5H |
段取り | 0.5H | 0.5H |
芯出し | 3.5H | 0.05H |
ドライランによる動作確認 | 1H | 0H |
合計 | 8H | 1.05H |
ワーク2個・電極16本(荒・仕上げ2工程)の想定
段取り時間とは、ワークのセットおよび通り出しと、電極のATCセット時間の合計
放電CAM使用時の芯出し作業時間は、基準球と加工物のティーチング作業時間のみ(無人での自動芯出し測定時間は人的工数には含んでおりません)
DiproSOLID形彫り放電CAMは、人手による作業時間を削減し、現場の生産性向上・人員不足の改善に大きく貢献します。
CAMシステム単体としても優秀なDiproSOLID形彫り放電CAMですが、周辺機器やスケジューラと組み合わせることで、さらにハイレベルな自動化へとステップアップすることも可能です。
DiproSOLID形彫り放電CAMにご興味がございましたら、ぜひ一度以下のフォームからお問い合わせください。