Interview【Sodick User Report】 Kyoto city, Kyoto
SUGAWARA SEIKI Co., Ltd.
Achieved stable supplies of molds for powder molding by promoting process-by-process quality assurance and NC
Making full use of Sodick MC and EDM
Sugawara Seiki Co., Ltd. manufactures carbide molds and rotary press machines for powder molding. Many of the products we handle are for electronic parts used in sensors and smartphones, and we specialize in molds to mass-produce minute parts of 1 mm or less stably. In recent years, we have also been focusing on production capacity ramp-up. By switching from manual or general-purpose machines to NC machines, more efficient and stable-quality operation has been realized.
Since 2000, the company has been actively introducing Sodick’s wire-cut EDM, die-sinker EDM, and machining centers (MC) to make high-precision and efficient molds. In future, the company will continue to promote NC and automation in pursuit of making molds that do not depend on “craftsmanship.”
The company was founded in 1949. The company started the business from the repair and manufacture of a movie projector used in the movie theater in Kyoto, and it began manufacturing press machines for powder molding using its technology. In the 1950s and 1960s, TV sets became popular, and the demand for electronic components incorporated into CRTs grew. In the early days of the electronic parts, they were produced by compressing and molding ceramics powders and formed using a press machine modified from a rotary molding machine (= tablet press machine) for molding tablets. The company also began modifying tablet press machines to meet its customers’ needs, and began manufacturing rotary press machines and molds.
As for the mold for a tablet press machine, the part that corresponds to a die is called a “mortar,” and the part that corresponds to a punch is called a “pestle.”' The powder material is filled into a mortar and compressed from above and below with two pestles to form tablets. In the mold of the tablet press machine, this pestle is integrated with the holder, and it was difficult to process the tip of the pestle to compress powder into a complicated shape. Therefore, the company devised a mold that divides the holder and the tip of the pestle. By using a method in which only the tip of the pestle is machined separately and brazed to the holder, it is now possible to easily manufacture molds with complex shapes needed for electronic components. It has an advantage in terms of cost because only worn-out tip of the pestle can be replaced. This innovative idea at the time led to orders from electronic component manufacturers.
“Since we handle both press machines and molds, our strength is that we can design press machines that take into account the ease of making molds. In addition, as specialized in ceramics molding, we established a technology for manufacturing molds made of cemented carbide from an early stage. 30 years ago, more than 90% of the molds we handle were made of carbide.” (President Naoya Sugawara)
Mainstay is multi-cavity molds
Currently, 60% to 70% of the company’s molds are for electronic components made from ferrite and alumina, followed by molds for throwaway chips and grinding wheels. In addition to the molds installed in our own rotary press machines, we also handle a number of molds used in single-shot powder-molding press machines. We perform various machining processes based on the mold drawings designed by the customer, and then ship after assembly, finishing, and inspection. We produce about 200 to 300 molds a month, which are a set of dies and punches.
Among them, the “ultra-small multi-cavity mold” that is capable of molding multiple locations is a representative product that we have been developing jointly with customers since the 1990s. Starting from 2 cavities, we have a track record of manufacturing 23 cavities and 49 cavities. By installing the ultra-small multi-cavity mold in a rotary press machine or single-shot press machine, it is possible to significantly increase productivity. These innovative technological developments can be said to be the company’s strength.
49-cavity mold
They are also skilled at machining carbide molds with high precision. We conduct thorough inspections in every process, including cutting, grinding, EDM, and MC machining. By passing on to the next process while guaranteeing accuracy, we meet the strict requirement of 0/+ 5 μm tolerance.
We also place importance on manufacturing long-life molds. President Sugawara says, “In addition to selecting the most suitable cemented carbide for the powder to be molded and the shape of the part, we also pay attention to equalizing the clearance so that the die and punch do not come into contact.” Clearance is adjusted at the stage of assembling and finishing the mold, but the company’s stream is to increase the degree of perfection at the stage of machining so that it can be adjusted by even anyone other than a skilled worker. By closely communicating with those in charge of each machining process, such as “This is easier to process” and “This is easier to position,” it is possible to produce molds with even clearance and high repeatability.
Close communication on site is the secret to high precision.
Trust born from a crisis
While increasing the added value of molds, the company also focuses on improving the efficiency of mold making and increasing capacity. The key is to reduce manual labor and eliminate waste, and we have been promoting NC and automation. In the process, Sodick’s machine tools have been highly evaluated. Currently, about 30 machines including EDM and MC are in operation.
It was after 2000 that the company, a long-standing Sodick user, began to highly appreciate Sodick’s machine tools. The trigger was the introduction of the wire-cut EDM “AP200.”
At the time, the company was working to realize automatic threading of wire electrodes with a diameter of 0.05 mm. Automatic wire threading is an essential function when unmanned machining of molds with multiple holes, such as ultra-small multi-cavity molds, but in order to perform the process using ultra-fine wire electrodes with a diameter of 0.05 mm, it requires not only the accuracy of the machine itself but also the operator’s know-how to manage flushing holes and adjust jet water pressure. On the other hand, the automatic wire threading at night was not successful in the existing water specification machine, and the machine was stopped every morning. “It was so bad that the operator in charge didn’t want to come to work,” President Sugawara recalls.
While automatic threading of ultra-fine wire electrodes was having difficulties, we introduced the oil-specification AP200 as proposed by Sodick. When we tried automatic wire threading of φ0.05 mm using the same machine, we succeeded after much trial and error. It was a concern that the machining time was longer than that of the water-specification machine, but the company found that there was no difference in machining time with the small-diameter molds that the company handles. Moreover, the surface roughness was also improved by setting the machining conditions finely. “Introducing the oil-specification AP200, which has excellent automatic wire threading, resulted in a by-product of improved surface roughness. This has also led to significant progress in terms of the quality of the finished surface, which is the most valued aspect of our molds by our customers.”' (President Sugawara)
The relationship of trust between the company and Sodick was strengthened due to Sodick’s quick response and careful after-sales follow-up leading up to the introduction of the oil-specification AP200. “The most troublesome situation for our company is when our machines stop working. Sodick visited us on the same day or the next day at the latest to help us, and they explained in detail the cause of the failure which was really helpful.” (President Sugawara) Until then, wire-cut EDM was mostly made by other companies, but Sodick’s became the main product.
Significant reduction in hand polishing
Sodick products continued to be introduced after 2000. The ultra-precision die-sinker EDM “AP1L” released in 2004 is equipped with an SVC circuit for high-speed, high-quality finishing as standard, and can achieve both increased machining speed in the finishing area and excellent surface roughness. The company is using multiple units of this AP1L. With conventional machines, a thick polishing allowance was left and the polishing was done by hand which took a lot of time, but the AP1L’s improved surface roughness significantly reduced the time required for hand polishing.
“The method of finishing by hand which leaves a thick polishing allowance takes time and has poor reproducibility, and there will be some leftover materials. By introducing AP1L, productivity has increased dramatically.” (President Sugawara)
AP1L, an ultra-precision die-sinker EDM
In 2017, an all-axis linear motor-driven fine precision machining MC “UH430L” was introduced in order to replace stepped machining of carbide molds with NC machines from machining with general-purpose machines and hand polishing. Sodick’s proprietary UH430L spindles reduce vibration and core runout to achieve both balanced rotation/torque characteristics and high rigidity. In addition, high-quality finishing in the fine precision range is realized by speeding up control cycles of individual axis and controlling characteristics of resolution 1 nm.
The company combines UH430L and diamond-coated small-diameter tools to process the stepped shapes of carbide molds with Ra 0.001 to 0.009 mm. Conventionally, it is necessary to finish the mirror surface by hand polishing after machining with a die-sinker EDM or a general-purpose profile grinder, and the time in which the person is engaged was very long. By replacing this machining part with UH430L, we have succeeded in finishing to a surface roughness close to a mirror surface. We achieved a significant reduction in personnel costs.
There is no big difference between the cost of introducing MC and the labor cost that could be reduced, but the President Sugawara says, “It's big for operators to be able to do other tasks.” With the collaboration of not only Sodick but also tool manufacturers and CAD/CAM manufacturers, the company will ultimately aim for polishing-less products.
MC “UH430L” for fine precision machining of all-axis linear motor drive
Focusing on improving efficiency at machining sites
The company which is reducing hand polishing and converting from general-purpose machines to NC machines will continue to make increasing efficiency at the machining site its primary goal.
“Because we handle a wide variety of products in small quantities and small items, our company has established a practice of machining using general-purpose machines. However, given the recent work style reform, the development of next-generation human resources, and the succession of skills, it is questionable whether the current situation is okay. I think we should shift from general-purpose machines to NC machines and automate them.” (President Sugawara). Recently, the company considers introducing a multi-tasking machine that combines grinding and cutting into one machine, with the aim of reducing setup changes and improving machining accuracy in one-chucking machining.
In the progress of NC and automation, the directivity of human resource development is also required to be reexamined. In the first place, the number of young people who want to become craftsmen is decreasing, and young people are no longer attracted to the way of working, where it takes five or ten year’s to acquire skills.
President Sugawara says, “It is true that making molds is a craftsman’s job, but in an age where it is common for people to change jobs after three years, it is difficult to convey the appeal of craftsmen to young people and build a system to nurture them as craftsmen. The company currently limits the types of machines that operators are responsible for, but it is also working on building a new training system to prevent from becoming dependent on a particular employee. Instead of fostering specialists for one model, the company’s policy is to raise the level of technology throughout the company.
Study automatic preparation of machining data
On the other hand, “We must deliver products of a certain quality to our customers. When we think about how to realize it, we need a certain degree of NC and automation.” (President Sugawara).
If machining by manual or general-purpose machine is changed to NC machine, the qualities are stabilized. However, machining with an NC machine requires the creation of an NC program using CAD/CAM. If the man-hour of NC programming increases, the burden of workers must be increased. Currently, the company has one operator in charge of everything from creating NC programs to setting workpieces, machining, and measuring, but President Sugawara thinks, “We need to determine what work an operator really needs to do.”
One idea we are considering is separating the creation of NC programs from the operator’s work. For this purpose, we are exploring automated programming using 3DA (three-dimensional annotation data: three-dimensional models with notes, such as dimensions and symbols, are added). Since the company basically uses 2D diagrams, the challenge is how to use 3DA in an environment where 2D diagrams are used.
The new building, built in response to strong orders for the ultra-precision die-sinker EDM “AP1L,” is lined with Sodick wire-cut EDM.
Expectations for dynamic conveyance between machines
The company makes effective use of Sodick products for efficient mold making. What we expect from users is a feature that helps further automation. “We are interested in the transfer of workpieces between the fine-hole EDM and the wire-cut EDM, and the transfer of electrodes between MC and the die-sinker EDM,” says President Sugawara. In addition to the functions of AWC (automatic workpiece exchanger) and ATC (automatic electrode exchanger), the company demands a solution to automate the transfer between processing machines.
The company, which continues to receive strong orders for carbide molds, will strive to further increase production capacity by executing DX (digital transformation) in addition to NC and automation. By replacing the know-how gained over 30 years in carbide machining with digital data, we will pursue the creation of molds that do not depend on the craftsmanship of skilled workers.
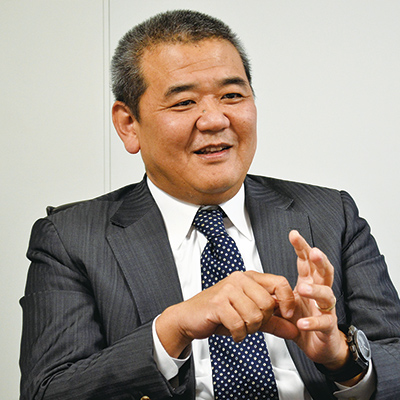
President Naoya Sugawara
SUGAWARA SEIKI Co., Ltd.
- Head office address
- 14 Nagitsujinishiuracho, Yamashina-ku, Kyoto City, Kyoto Prefecture 607-8164 JAPAN
Telephone No.:075-581-7121
- Representative
- President Naoya Sugawara
- Established
- 1966
- Sales item
- Manufacturing of carbide molds (precision molds for powder molding)
Production of rotary press machine for powder molding
- URL
- http://www.k-sugawara.co.jp
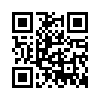