Interview【Sodick User Report】 Ichinoseki-shi, Iwate
SANKO KASEI Co., Ltd.
Supporting Stable Mass Production of
Plastic Parts by "Combination" of
Mold Technology and Molding Technology
Sodick's metal 3D printer also improves the functionality of molds
Sanko Kasei manufactures a wide variety of plastic parts, including interior and exterior automotive parts, housing equipment, electrical and electronic parts, and machine tool parts. Sanko Kasei has long been pursuing manufacturing that utilizes 3D models and has been a pioneer in product design and mold design using 3D CAD, resin flow analysis using 3D models, prototyping using resin 3D printers, and mold and jig manufacturing using metal 3D printers.
In particular, the company has been working closely with Sodick, the manufacturer of metal 3D printers, to explore their usage and acquire expertise. The molds and jigs that can only be produced by laminated molding enable the company to consistently achieve the molding quality demanded by its customers. We interviewed the company to learn more about its efforts.
Mold (bottom) and its model (top) of the motor housing containing the conformal cooling water pipe.
Cooling efficiency increased and deformation of printed products were suppressed.
The company is a medium-sized molding manufacturer with approximately 780 employees in Japan and approximately 1,400 employees in the group as a whole, including those overseas. Headquartered in Itabashi-ku, Tokyo, the company has 10 factories in Japan, mainly in Ichinoseki-shi, Iwate, where the founder was born, and three overseas factories in Suzhou and Dalian in China and Mexico. The company's domestic molding plants have approximately 350 injection molding machines with clamping capacities ranging from 18 to 850 tons, and produce plastic parts for a wide range of fields, including automotive interiors and exteriors, toilets and water fixtures, sensor and capacitor housings, machine tools, and medical equipment. The molding factory uses both in-house and outsourced molds, and the molding factory (Ichinoseki-shi, Iwate) manufactures about 100 difficult molds a year, including molds that require a large number of molds and molds for which variation must be kept to a minimum. The company sends out about 100 difficult molds a year to factories in Japan and overseas.
The company believes that the key to differentiating itself from its competitors is its ability to achieve stable mass production of parts through both tooling and molding technologies. In the medical device field, where the company is focusing on orders, it offers fittings for intravenous drip tubing, in which mesh is molded directly into the tubing to remove impurities. The product was accepted by users who place importance on safety, leading to mass production. This joint, in which fine mesh is integrally molded with the tubing rather than inserted separately, makes full use of the company's technologies, including mold design, flow analysis, high-precision mold machining, and careful selection of molding conditions. Mr. Hisashi Hashimoto, molding factory manager, who oversees the mold division, says, "Our strength lies in our ability to handle the entire process from mold design and manufacturing to molding of parts, which enables us to stably mass produce difficult plastic parts such as mesh molding, thin-wall molding, and ultra-thick-wall molding, which no other company can imitate. We are confident in our company's comprehensive capabilities."
Mr. Hashimoto, molding factory manager which has been involved with Metal 3D Printer since its introduction
Using 3D Models to Their Fullest Potential
Another feature of the company is its efficient manufacturing using digital technology. As Mr. Hashimoto, molding factory manager, says, "We have been pursuing 'how to make full use of 3D models'", 3D CAD was introduced early on for product and die design, and 3D models are shared internally, with customers, and with partner manufacturers to facilitate operations. In addition, resin flow analysis using analysis software such as "3DTIMON" and "Moldflow" not only helps prevent rework in in-house mold design, but has also become a service in the form of analysis reports submitted to customers.
The company is also actively using 3D printers. Using the DigitalWax029J+ resin 3D printer manufactured by DWS and installed in the mold factory, the company creates prototypes of products for which it is contracted to mass-produce. The prototypes are then distributed to mold designers, molding factories, product measurement, sales, and quality assurance staff in preparation for the start of mass production a few months later. "When you hold the prototype in your hand, you can get an idea of the size, weight, and texture of the part. Having an image in advance leads to smooth mass production," says Mr. Hashimoto, molding factory manager. As part of these efforts, the OPM350L metal 3D printer from Sodick was introduced in 2018.
Scanning the molded product with a 3D scanner and superimposing it with a three-dimensional model to grasp measurement which can not be known by pinpointing.
The only machine that
takes post-processing into consideration
Mr. Hashimoto, molding factory manager, who had been researching and introducing resin 3D printers, was one day asked by President Takashi Hosokawa to research metal 3D printers. At that time, the mainstream metal 3D printers were made in Germany and used for modeling parts such as aircraft impellers, not molds.
As a result, many of the products were "left as-is" (i.e., left as-formed) and were not designed to create the standards that would be required for post-processing. Mr. Hashimoto, molding factory manager, who wanted to use the metal 3D printer for mold making, said, "If you are going to introduce a metal 3D printer, you must have standards for mold making, not for parts. I felt that a metal 3D printer that could not create standards would not be worth introducing," he recalls.
It was at this time that Mr. Hashimoto, molding factory manager, encountered the OPM series, which was developed for use in molds, and the OPM350L, a high-precision machine that combines laser melting and solidification of metal powder with finishing by milling, was released in 2016, following the OPM250L released in 2014. It can model 350 mm (width) x 350 mm (depth) x 350 mm (height), which is larger than the OPM250L. When Mr. Hashimoto, molding factory manager, learned that Sodick's metal 3D printer could create standards for post-processing, he was convinced, "If we are going to use it for molds, this is the one!". When he reported this to President Hosokawa, the decision to install the printer was made immediately.
“OPM350L” is a high-precision Machine that enables melt-solidification of metallic powder by Laser and finishing by milling.
Absorbing Sodick's Knowledge
The operational aspect was the hardest part. Unlike molds that are machined with a machining center or electrical discharge machine, metal 3D printers offer a higher degree of freedom in mold design because of the greater degree of freedom in modeling. However, he was not sure how the water cooling tubes should be aligned, what the cross-sectional area and diameter of the water cooling tubes should be, and how much space should be left between the water cooling tubes. The mold designers had so many options that they could not make a decision.
Therefore, Mr. Hashimoto, molding factory manager, asked Sodick for a six-month consulting service on the premise of purchasing the OPM350L. In addition to the basic design of conformal cooling water pipes, he also received guidance on modeling methods using 3D CAD to help his designers master mold design based on the use of a 3D printer. "Without Sodick's guidance, we would probably still be doing things by trial and error.
It is very important to know how to operate the printer after its introduction. I recommend that companies considering the introduction of a metal 3D printer receive as much support from the manufacturer as possible," said Mr. Hashimoto, molding factory manager.
Conformal Coolant Tubing Applied to Molds
Several years after its introduction, the operation of the metal 3D printer is getting on track. The conformal cooling water tube was first applied to a mold for a motor housing. A mold with a conventional straight cooling water pipe was also made, and the molded parts from the two molds were compared. There was a clear difference in "ease of assembly." When placing the conformal cooling water pipe, a semicircular groove was carved in advance on the base plate, and a semicircle was formed on top of it to shorten the molding time.
This is another finding obtained from Sodick.
The company is also working on the application of lattice structure molds. Originally, this was intended to shorten molding time and reduce material costs. However, unlike conventional molding, the lattice structure is not filled with contents, so deformation due to thermal contraction after molding is mitigated. The air in the lattice structure also had the effect of keeping the mold warm.
Strength is assured and part of the mold is made to lattice structure.
In addition to molds, there is an example of molding suction nozzles for robots used in the company's molding factories. The suction nozzle, which is used to set minute insert parts into the mold by suctioning them with air, originally consisted of 21 machined parts, but was replaced by a metal 3D printer, reducing the number of parts to three. The new suction nozzle solves this problem by making the suction hole area 10 times larger than that of the previous product.
Suction nozzle designed with attraction force. Metal 3D Printer can be used for making holes, which is difficult to make with machining.
Efficient Cooling by
Combination of Air and Water
In addition, the company intends to focus on the use of "air cooling" in the future. Air cooling, in which air is circulated to cool molds, has been around for a long time, but it is not widely used because the thermal conductivity of air is inferior to that of water. However, Mr. Hashimoto, molding factory manager, says,
"The advantages of air cooling are that there is no water leakage and the pipes do not rust. It is worth trying to use air cooling in areas where water cannot be circulated while using water cooling," and is promoting its application to molds.
Examples of where air cooling has been used to its advantage include the use of cooling pipes through slide cores that open in four directions, with air circulating only when the slide cores are closed, and the use of air circulation in narrow, deep areas where water cannot easily pass. Using thermal imaging cameras, the company has verified that the combined use of water and air is more effective in cooling molds than water cooling alone.
By increasing the cooling effect, the company expects to shorten the molding cycle and reduce distortion of the molded product.
Using Metal 3D Printer to
Propose Improvements to Customers
Mr. Hashimoto, molding factory manager, commented on the OPM350L: "We still have the same high regard for the machine. I think it is the one and only one to use in mold making," he says. Because it is a delicate machine, the slightest error in material supply can cause an error message to appear, but "if we call them, they come to us right away. They take good care of us as users."
For now, the metal 3D printers are used only for internal purposes, but in the future, the company plans to offer consulting services to solve customers' problems related to resin molding, and to sell the molded mold parts as a set. "We would like to propose improvements by utilizing our expertise in flow analysis and shape measurement," says Mr. Hashimoto, molding factory manager. In order to achieve customer needs such as higher precision and cost reduction of molded products, and to meet the SDGs (Sustainable Development Goals), and to differentiate themselves from competitors, they will continue to actively incorporate new technologies and know-how, including metal 3D printers.
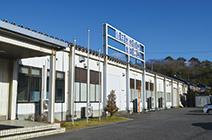
Production at a mold factory
(Ichinoseki-shi, Iwate) centered on molds with a high degree of difficulty
SANKO KASEI Co., Ltd.
- Company address
- 1-28-3, Narimasu, Itabashi-ku,
Tokyo 175-0094 JAPAN
TEL:03-3939-8201
- Representative
- Takashi Hosokawa, President and CEO
- Established
- 1965
- Business description
- Design, manufacture and sale of precision plastic parts for industrial use
Design, manufacture and sale of plastic molds
- URL
- https://www.sanko-kasei.co.jp/en/
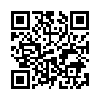